In an effort to capture and transfer knowledge as well as define corporate requirements to improve facility reliability, many corporations consider developing a collection of Best Practices. With the “great retirement/resignation” hitting all industries, more than ever, the capture of corporate memory is crucial. A Best Practice is defined as a technique or methodology that, upon rigorous evaluation through experience and research, has demonstrated success, had an impact, and can be replicated. Best Practices are frequently used by facility owners and operators to provide their requirements and guidelines for construction and maintenance. As required by Recommended and Generally Accepted Good Engineering Practices (RAGAGEP), Best Practices must meet minimum industry requirements but may be more stringent based on experience and unique attributes of a facility. For this reason, Best Practices typically utilize and direct users to a published industry standard to set baseline requirements and then clarify options or provide additional requirements above the industry standard based on company preferences and experience.
When companies seek a solution for adding a collection of Best Practices to their organization, the options most often considered are purchasing a general industry Best Practices collection and using it without customization; utilizing an Engineering, Procurement, and Construction (EP&C) firm’s collection previously used for projects; or creating an internal Best Practices collection by updating a legacy collection. Building a Best Practices collection becomes more complicated for companies that have been created through mergers or acquisitions because of cultural differences and approaches to new construction and mechanical integrity.
In this article, we will explain why E2G | The Equity Engineering Group, Inc. advocates developing an internal Best Practices collection over other options, and provide recommendations on how to best develop, implement, and maintain an internal Best Practices collection.
OSHA Interpretations and Recommendations
In June 2015, the Occupational Safety and Health Administration (OSHA) published new guidance for industry standard 29 CFR Part 1910.119 “Process Safety Management of Highly Hazardous Chemicals” with interpretations for Process Safety Management (PSM) and RAGAGEP, including clarifications and interpretations regarding the following:
- The definition of RAGAGEP and its sources
- The use of “shall” vs. “should”
- The use and acceptance of internal employer documents such as RAGAGEP
- Considerations for maintaining compliance with the standard
In this published memorandum, OSHA not only provides clarification that appropriate internal standards are considered acceptable RAGAGEP documents, but it also includes reasons why OSHA recommends facilities develop and use internal standards. Per the memorandum, facility internal standards can serve the following purposes:
- Translating the requirements of published RAGAGEP into detailed corporate or facility implementation programs and/or procedures
- Setting requirements for unique circumstances for which no published RAGAGEP exists
- Supplementing published RAGAGEP that partially or inadequately address the employer’s needs
- Controlling hazards more effectively than available codes and standards
- Addressing hazards when the codes and standards used for existing equipment are outdated and no longer describe good engineering practice [1]
As a provider of customizable Best Practices for 20-plus years, in use by almost 40 clients with hundreds of facilities, E2G wholly agrees with OSHA’s recommendation for internal standards. We would add that internal Best Practices offer additional benefits such as:
- Promoting safety, managing risk, and improving reliability
- Capturing corporate memory
- Transferring knowledge
- Providing cost-effectiveness
Lifecycle Management and Improved Reliability
To improve reliability, facility owners and operators need to address the overall process of whole lifecycle management for their equipment. Lifecycle management (LCM) is the process of managing the cradle-to-grave life of assets including design, construction, in-service use, repair if required, and retirement. The LCM process for fixed pressurized equipment (including pressure vessels, piping, and tankage) is shown in Figure 1. Each step is required for comprehensiveness. It starts with consideration of potential damage mechanisms in the design process and selection of appropriate construction codes to ensure reliable designs. LCM continues with the establishment of in-service inspection programs to monitor anticipated damage and determine the presence of unanticipated damage mechanisms, application of fitness-for-service (FFS) technology if unanticipated damage is discovered, and implementation of effective repair procedures as required to ensure mechanical integrity of in-service equipment[2].
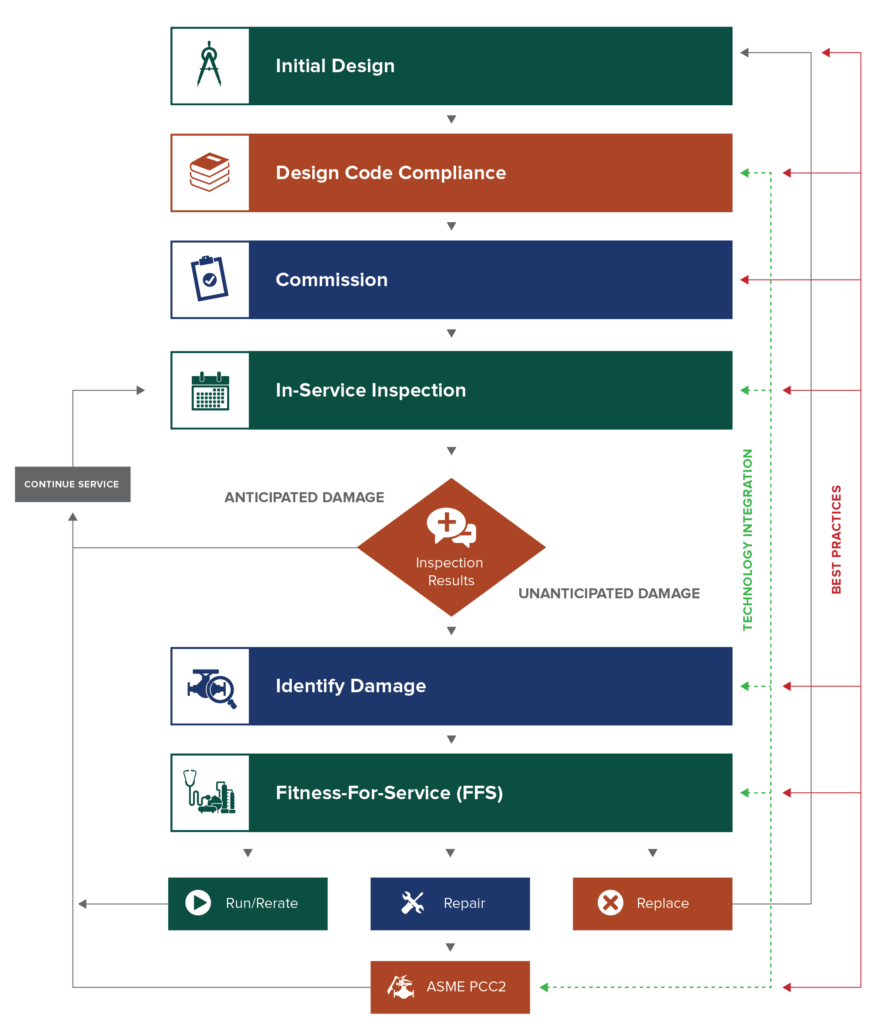
The LCM framework shown utilizes published industry codes and standards to implement the process. Figure 1 illustrates how the industry codes and standards relate to the LCM, creating a common technology core. While technology integration provides the relationship roadmap, the current challenge is that most industry codes and standards do not provide complete guidance, and additional information in the form of corporate memory and Best Practices is required for complete guidance. Best Practices overlay the LCM framework to document requirements from construction to in-service equipment issues (e.g., inspection, FFS, and repair guidelines). With the “great retirement” following the pandemic, it is becoming even more difficult to cultivate corporate memory and/or expertise.
Customized Best Practices – A Best Practice
The challenge in selecting a Best Practice platform is that neither general industry Best Practices nor an EP&C firm’s Best Practices account for the retention of corporate memory. E2G defines corporate memory as the total body of knowledge, comprised of both documented and undocumented memories and experiences, created over the course of an individual organization’s existence. Corporate memory may also come from an organization’s documentation of equipment deficiencies and failures through its mechanical integrity (MI) program, its lessons learned. To take full advantage of corporate memory, each organization should have a goal to document accumulated knowledge so that information is not lost over time. As its core function, an internal Best Practices collection provides an ideal forum to document corporate memory and capture lessons learned from the MI program as the organization’s experience evolves. Having been in existence for over 20 years and now with almost 40 clients, the Equity Engineering Practices® (EEPs) have captured over 1500 years of E2G’s subject matter experts’ (SMEs’) corporate memory and lessons learned, and many thousands of “client SME years” of corporate memory and lessons learned.
Knowledge Transfer and The Why
It is well documented that many organizations battle with the potential gap in expertise further aggravated by the “great retirement.” If these experienced employees’ knowledge and expertise are not recorded as corporate memory, 40-plus years of practical experience and knowledge will be lost. E2G believes organizations should focus on capturing corporate memory to support knowledge transfer. By making the effort to transfer expertise, organizations can be confident their next generation of employees will be trained and provided with valuable resources to continue operating the facility safely and with improved reliability. The EEPs are a great training ground. With The Why being added to Practices in the EEP collection, E2G is furthering this capture of corporate memory and knowledge transfer. The Why is added information in the Practices indicating the SMEs’ reasons and background for specific requirements in the Practices – for instance, why a certain pressure vessel nozzle detail is used to make future rerating more practical or improve fatigue life, or why annular rings are used in many tank designs for total lifecycle reliability.
Cost-Effectiveness
The LCM serves as a reminder that costs may occur at different stages during an equipment’s life. Components purchased at a lower cost may be sufficient for certain applications, whereas the same components may lead to significant long-term expenses stemming from unanticipated damage in a different application. By documenting these lessons learned as corporate memory in Best Practices, corporations can greatly improve their MI, resulting in higher equipment availability.
To greatly increase long-term savings, internal Best Practices indicate where over-engineering is not required and where there are benefits to larger initial purchase costs to limit the need for ongoing inspection and maintenance costs. For example, if a certain type of pump seal proves to be successful for a particular application, an organization should document its use as a Best Practice to prevent over-engineering and over-spending on similar future designs. In addition, for some wet H2S services, carbon steel clad plate is initially more expensive, but the upgraded material significantly reduces inspection and maintenance costs over the life of the equipment, making the decision to upgrade material cost-effective.
There are costs associated with maintaining internal Best Practices, capturing corporate memory, and transferring knowledge. However, the benefits from reducing risk through improved reliability, minimizing future engineering efforts by capturing corporate memory and transferring knowledge, and reducing costs by reducing inspection for unanticipated damage greatly outweigh the costs to maintain the collection.
EEPs and E2G Training – Transferring Knowledge to Future SMEs
At a recent API Inspection and Mechanical Integrity Summit, a panel of experts talked about the future of MI. The eight panelists represented almost 300 years of experience in the MI field. As they spoke, one big concern resonated – the capture of the expertise on that panel and among the dozens of other SMEs in the audience so the next generation could continue the important work of maintaining safe, reliable, and profitable facilities. The EEPs are a source of capturing that knowledge and transferring it to future generations. At E2G, we have started that knowledge transfer. In many of the 21 sections in the EEPs, there is one senior SME and a mid-level engineer being mentored to take on some of the EEP responsibilities. We are committed to developing OUR next generation of industry SMEs. Within our Training business, we have begun providing our internal, early engineer training curriculum, Fundamentals of Asset Lifecycle Management (FALCM) to the public. We are committed to developing YOUR next generation of industry SMEs.
As always, E2G will continue to pass along and transfer our knowledge in the MI area at our annual FFS and MI Symposium. Look for information coming soon on the Fifth Annual Symposium to be held in February 2023. We will also be introducing another product aimed at SME knowledge transfer and SME access. Look for announcements on this in early 2023.
For more information on our EEPs or training programs, please submit the form below:
References
- Galassi, Thomas. (2015 June 5) Memorandum for Regional Administrators and State Plan Designees, RAGAGEP in Process Safety Management Enforcement. Retrieved from: https://www. osha. g o v /pls/ osha w e b/ wadisp.show_document?p_ table=INTERPRETATIONS&p_ id=29414.
- Osage, David. (2009 May 21) European Federation for Welding, Joining and Cutting. Presented at Eurojoin 7. Modernization of Pressure Vessel Design Codes, ASME Section VIII, Division 2, 2007 Edition and Fitness-For-Service Codes, API 579-1/ASME FFS-1, 2007 Edition with Applications.