- Home
- Engineering
- Rotating Machinery & Vibration
- Computational Fluid Dynamics (CFD)
COMPUTATIONAL FLUID DYNAMICS
Solve Complicated Flow-Related Issues
It’s difficult to predict fluid flow or visualize the chemical reactions that occur in piping and other fixed equipment. Use computational fluid dynamics (CFD) to visualize the complicated flow-related problems found in refineries, petrochemical, chemical, or other industrial processing plants to remove conservatism in design and save money on new components.
Our team of rotating equipment and vibration specialists use CFD to investigate flow problems and address flow turbulence, mixing, and thermal fatigue issues. Using this information, we will develop cost-effective design iterations to reduce piping and structural vibration, remove conservativism in design, solve root cause flow-related problems, and develop mitigation strategies to prevent future failures.
What is Computational Fluid Dynamics?
CFD is a type of fluid mechanics that combines numerical analysis and data structures to analyze and solve fluid flow issues.
Typical applications of CFD include:
- Optimization of flow rates and pressure drops in equipment
- Flow instability predictions
- Root cause failure analysis
- Prediction of flow-induced vibrations
- Accurate prediction of heat transfer coefficients
- Efficiency of phase separation in a mixer (e.g., separation of oil from oil-sands slurry)
- Effect of fluid sloshing in a storage tank
Flow-Induced Turbulence (FIT)
CFD provides valuable insight into the source and location of FIT. We use root cause analysis to develop cost-effective design iterations to mitigate vibrations and prevent future failures of expansion joints.
- Address flow turbulence, mixing, or any fluid flow-related problems
- Maximize process flow rates while avoiding flow-induced vibrations
- Optimize piping designs to reduce FIT and high-stress, fatigue-prone locations
- Re-engineer piping systems to handle higher flow rates and increase profitability during scheduled outages
Case Study: Flow Behavior in a Dual Inlet Nozzle Coke Drum Using CFD
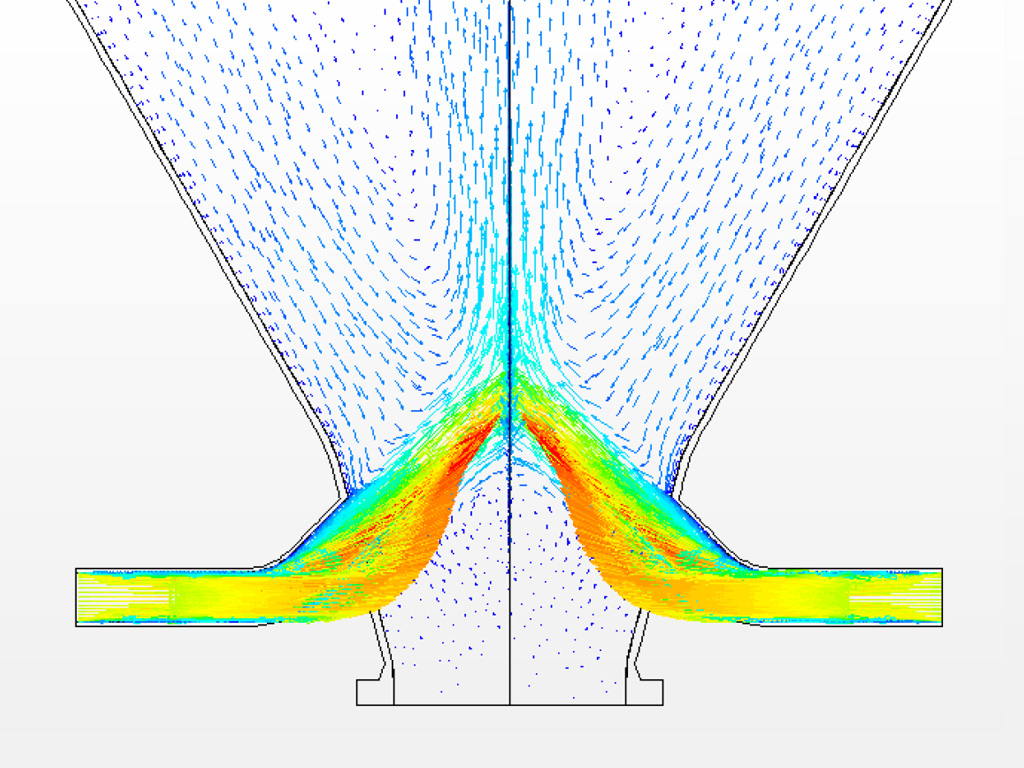
Equity used CFD to better understand the flow behavior in a coke drum with dual nozzle inlets and determine how to optimize the flow patterns, rates, and pressure drops. Our team simulated two flow rates:
- Slower fill rates: predicted symmetric circulation zones in the plane of the nozzle and no circulation zones in the plane 90° to the plane of the nozzles.
- Faster fill rates: determined the flow becomes unstable at the faster rate and small perturbations in the inlet velocities switched the circulation zone pattern from one side to the other.
Result: The CFD simulation showed circulation zones in the plane 90° to the plane of the nozzle. The unstable circulation zone pattern can result in temperature gradients more than 100°F (37°C) around the circumference of the bottom cone.
Case Study: Mixing Quill Design & Flow-Induced Vibration Analysis
Used CFD analysis to determine if a quill design can minimize the risk of thermal-fatigue cracking. The CFD analysis looked at turbulent thermal mixing and global operating fluctuations to predict the behavior of the cold fluid in the branch pipe. The analysis found the cold fluid did not hit the inner surface of the run pipe until a long distance from the junction, which resulted in reduced temperature gradients at the tee junction and minimized the risk of thermal-fatigue cracking at the junction.
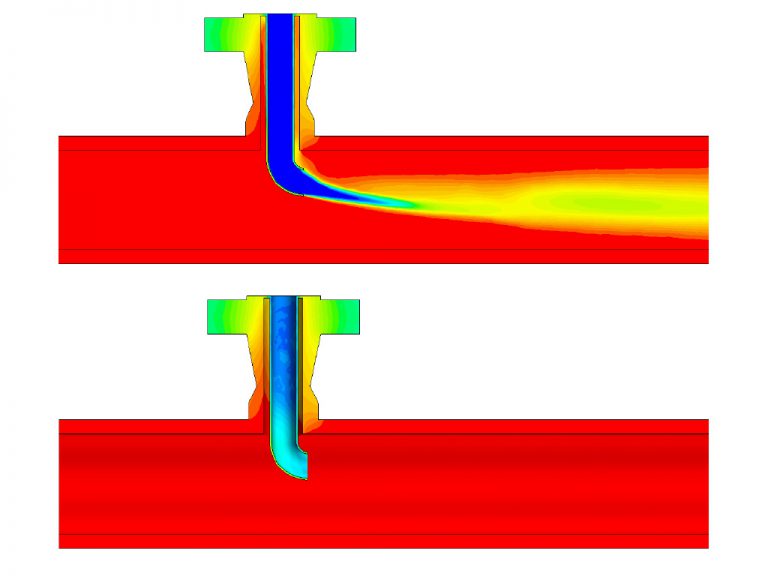
Result: the CFD analysis helped to choose the geometry of the quill to avoid flow-induced vibrations. The frequencies of the vortex shedding around the quill were not close to natural frequencies to avoid flow-induced vibrations.
Root Cause Failure Assessments
If there’s been an equipment failure at your facility, you need a team who can provide immediate answers, outline practical recommendations, and offer corrective solutions. We will identify what happened, why it happened, and present solutions to prevent future failures. Using our team’s expertise with process simulation and fluid dynamics, we solve root cause problems for rotating equipment and piping vibration.
- Conduct a metallurgical failure analysis, CFD, and finite element stress analysis (FEA)
- Predict acoustic-induced vibration (AIV) failures and provide remedial actions
- Conduct onsite interviews with personnel
- Collaborate with metallurgy and corrosion experts
Recommended Reading
- Asset Management /
- Library /
- Mechanical Integrity /
- Webinars /
- Library /
- Piping /
- Rotating Equipment /
- Vibration & Dynamics /
- Library /
- Piping /
- Vibration & Dynamics /
Rotating Equipment, Vibration, & Dynamics Expertise
Equity’s team of rotating equipment and vibration specialists combines its unique and specialized mechanical engineering expertise with field testing and advanced stress and fluid mechanics analysis to diagnose, evaluate, and mitigate failure risks associated with the mechanical vibration, acoustic pulsation, and flow-induced forces in machinery, vessels, piping, and structures.
Our experts:
- Have 40+ years of combined field experience
- Are certified ISO VCAT-IV vibration analysts
- Are voting members of API 579 committee and develop standardized pipe vibration assessment methods
- Are members of API Sub-committee of Mechanical Equipment (SOME)
- Collaborate with fitness-for-service (FFS) and materials & corrosion experts to manage an asset’s lifecycle