- Home
- Engineering
- Rotating Machinery & Vibration
- Vibration Risk-Based Inspection
VIBRATION RISK-BASED INSPECTION
Find Your Vibration Problems Before They Find You
Small-bore piping failures due to vibration are one of the most common loss of containments in our industry. Once failures occur, many root-cause failure assessments have the advantage of hindsight when determining that the branch connection would have benefited from improved bracing.
Equity has developed a scalable tool — vibration risk-based inspection (VRBI) — to identify high-risk, vibration-prone piping circuits so proactive measures can be taken in the design stage or as part of debottlenecking projects and rate increases. VRBI expands upon the Energy Institute guidance by incorporating consequence analysis into the assessment, similar to standard risk-based inspection (RBI) practices. Conducting a comprehensive vibration risk assessment of your entire facility will prevent failures before they occur.
VRBI helps you proactively identify risk on a facility-wide scale by:
- Risk-ranking piping circuits to prioritize retrofits of existing systems, or identify changes in new designs
- Calculating risk before changing flow rate or embarking on a costly expansion projects
- Evaluating and identifying and evaluating retrofits or design changes to pressure relief piping to protect against acoustic-induced vibration (AIV) failure
- Prioritizing inspection and remediation in existing systems
How can you improve your facilities to reduce the risk of small-bore failures without bracing every connection?
Screen Your Entire Facility for the Following Risks
- Flow-Induced Turbulence (FIT)
- Pulsation from Surge or Rotating Stall
- High-Frequency Acoustic Excitation (AIV)
- Pulsation in Positive Displacement Systems
- Flow-Induced Acoustic Pulsation
- Surge/Momentum from Fast Actuating Valves
- Small-Bore Connections (SBCs)
- Thermowell Vibration
Two-Phase Approach
At Equity, we approach vibration problems differently. We recognize not all equipment needs to be fixed. We specialize in the evaluation of in-service equipment to determine risk factors and make the most informed decision regarding run, repair, or replacement.
- Phase 1 – vibration risk ranking of piping circuits using the Energy Institute likelihood of failure and Equity’s consequence modeling to prioritize vibration surveys
- Phase 2 – using results of Phase 1, conduct a field survey of highest risk systems and perform vibration fatigue screening
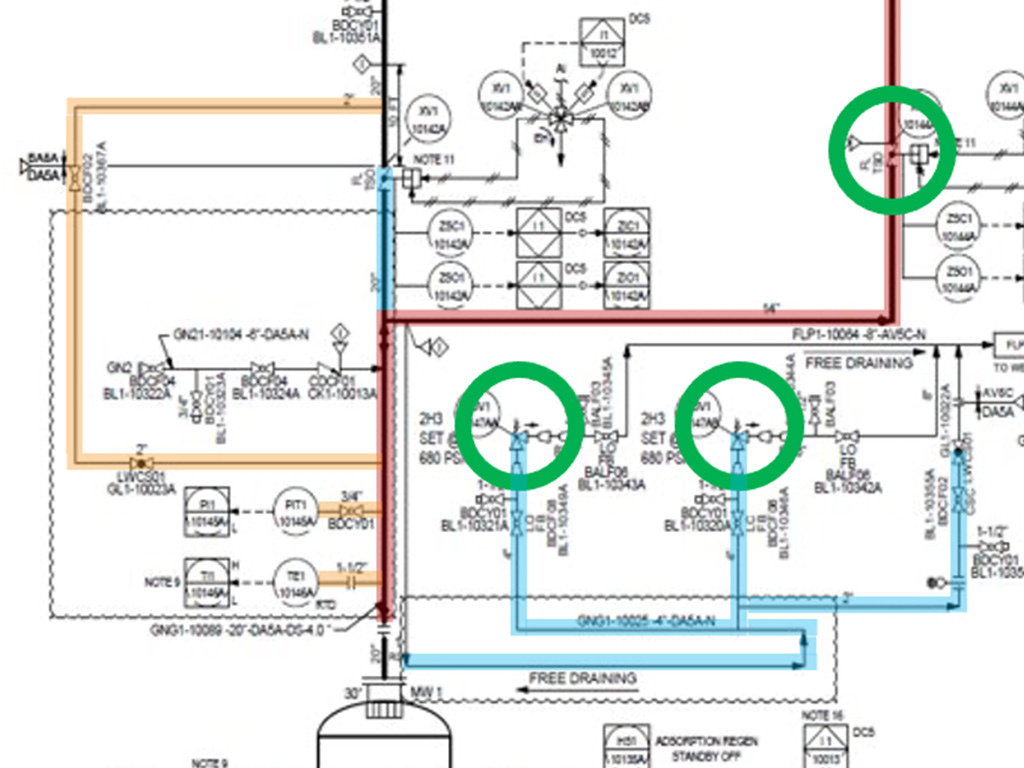
Recommended Reading
Rotating Equipment, Vibration, & Dynamics Expertise
We are vibration experts who deliver practical solutions to complicated problems. We offer turnkey services – field data capture, personnel interviews, vibration measurements, and analysis – to deliver technically superior recommendations.
Our experts:
- Have 40+ years of combined field experience
- Are certified ISO VCAT-IV vibration analysts
- Are voting members of API 579 committee
- Develop standardized pipe vibration assessment methods
- Are members of the API Sub-committee of Mechanical Equipment (SOME)
- Collaborate with fitness-for-service (FFS) and materials & corrosion experts to manage an asset’s lifecycle