HIGH-TEMPERATURE HYDROGEN ATTACK (HTHA)
Estimate Remaining Life & Manage Risk
When equipment is exposed to high-temperature hydrogen service environments, the impact can be catastrophic. HTHA is a challenging damage mechanism to detect and assess and has led to several significant industry failures.
Our materials and corrosion team specializes in HTHA analysis and uses state-of-the-art technology to guide inspection efforts and estimate remaining life. Our goal is to provide practical recommendations that help you manage the risk associated with HTHA.
What Causes HTHA?
Although often difficult to detect, HTHA is a primary concern for carbon or low-alloy steel equipment in the refining, ammonia, and coal gasification industries. Plus, as refineries repurpose equipment to process new feedstocks, biofuels, or low-sulfur fuels, there is an increasing importance for HTHA mitigation.
HTHA can lead to any of the following potential scenarios:
- Hydrogen gas atoms from the processing fluid dissolves and spreads through the vessel wall to create cavity growth
- HTHA cavities form methane molecules, which will grow until the pressure exceeds operating limits
- Combination of high temperatures and pressure will cause failure in the vessel wall
- Methane can create fissures, blisters, and decarburization of the surrounding metal
- HTHA is often evident in welds or weld heat-affected zones
We predict the conditions where HTHA is most likely to develop, and then focus inspections on the highest-risk components.
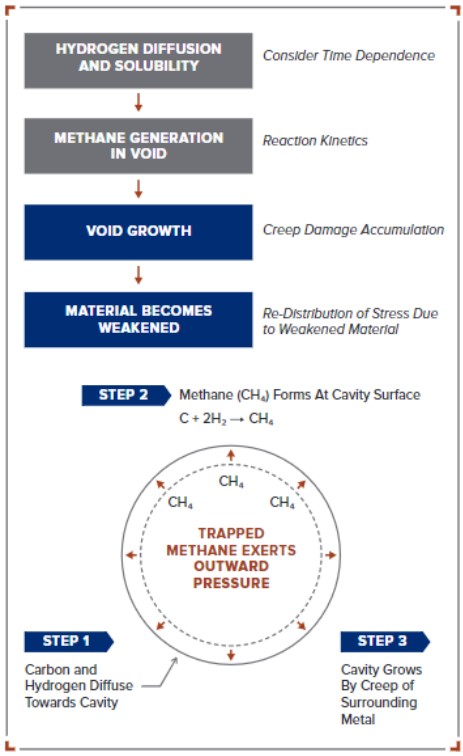
Equity’s High-Temperature Workflow
Our phased approach is designed to help you mitigate and manage the damage mechanisms caused by high temperatures, including HTHA. You will receive practical recommendations to help maximize production, extend the safe operating life of your equipment, and minimize costly component failures and unit downtime.
- Step 1: Review historical inspection records and past equipment repairs or alterations
- Step 2: Compile available operating temperature and hydrogen partial pressure data to establish meaningful loading histograms
- Step 3: Perform HTHA screening calculations to highlight critical or high-risk components
- Step 4: Conduct advanced stress analyses to estimate the current state of damage in critical components
- Step 5: Consider both volumetric damage and crack-like flaw propagation to estimate remaining life
- Step 6: Perform sensitivity calculations for varying pressure, temperature, etc., to determine practical inspection strategies and intervals
Using a Multi-Disciplinary Approach for HTHA
We can help your facility identify and mitigate potential HTHA issues by leveraging fitness-for-service (FFS) and inspection, and advanced analysis methods. Proper inspection planning and engineering evaluations will help you manage the risk associated with HTHA and make practical run, repair, or replace decisions. Our active participation in the joint industry programs sponsored by the Materials Property Council (MPC) gives our team exclusive knowledge of state-of-the-art technologies for equipment assessment.
Equity's Sampling Process
Effectively determine the remaining life of equipment and quantify risk by understanding the material properties and levels of material degradation. Equity’s proprietary technology, the Buckeye SamplerTM, takes small samples to help to identify equipment that’s vulnerable to HTHA damage, creep, fire damage, or other damage mechanisms and enables detailed microstructural laboratory analysis to determine the current state of damage progression.
The Buckeye Sampler will:
- Accurately control cut depths and match the dimensions qualified during the FFS assessment
- Eliminate mismatch or depth inaccuracies with the single-motion cutting action
- Remove samples from the inside diameter (ID) or outside diameter (OD) on carbon or low-alloy steels
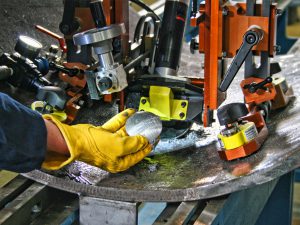
HTHA Joint Industry Project (JIP)
In 2013, Equity launched a joint industry project (JIP) focused on developing new FFS rules for HTHA assessments. This JIP has developed advanced HTHA inspection and nondestructive examination (NDE) techniques and established FFS as a credible method to predict HTHA and manage the associated operational risks. For more information, please contact Equity.
Recommended Reading
- Ammonia /
- Ammonia & Fertilizer /
- Corrosion /
- Damage Mechanisms /
- Fertilizer /
- HTHA /
- Library /
- Materials & Corrosion /
- Library /
- Materials & Corrosion /
- Fitness-for-Service (FFS) /
- HTHA /
- Industry Insights /
- Library /
- Materials & Corrosion /
- Mechanical & Structural Engineering /
Testimonials
Materials & Corrosion Expertise
Our team of corrosion and metallurgy experts combines their extensive experience with state-of-the-art technology to create safe operating environments while also guiding equipment design, material selection, inspection strategies, weld repair techniques, and process optimization.
Our experts:
- Have 350+ years of combined field experience
- Pioneered development of FFS and RBI
- Are the primary authors on WRC 528 and WRC 562
- Serve as lead investigators on API 571
- Have been members of Materials Property Council (MPC) Project Omega for creep evaluation since 1984
- Are active members of MPC MolyHy program