Introduction
In recent editions of API STD 653, Tank Inspection, Repair, Alteration and Reconstruction, the use of risk-based inspection (RBI) has been permitted as a means of determining the next inspection date for initial and subsequent internal inspection of storage tanks. In accordance with API 653, the RBI assessment must consist of a systematic evaluation of risk, which is the product of the likelihood, or probability, of failure (POF) and the associated consequence of failure (COF) in accordance with API RP 580, Risk-Based Inspection. To evaluate a tank’s risk of failing, tank RBI methodologies range from highly qualitative (various tank experts subjectively ranking POF and COF) to quantitative (POF and COF calculated based on a various design, inspection, operations, and maintenance factors). One highly quantitative method of performing the systematic risk evaluation required by API 653 is the tank RBI technology detailed in API RP 581, Risk-Based Inspection Methodology.
Tank RBI has often been used by owner-users as a means of evaluating a deferral of an internal inspection that was scheduled based on a prescriptive (or time-based) interval, when RBI was permitted to be used in this manner by the jurisdiction. However, tank RBI has other uses, such as determining and optimizing inspection activities for all tanks in a terminal or facility’s tank farm. In this issue of Industry Insights, we have seen that API 579 fitness-for-service (FFS) methodologies can be applied to storage tanks to make optimal run-repair-replace decisions. This article will examine the quantitative tank RBI method found in API 581 (Part 5), discuss how tank RBI is another integral part of the facility’s overall tank integrity management program (IMP), and examine uses for tank RBI other than deferral of scheduled internal inspections.
API 581 Tank RBI Overview
In API 581 tank RBI, the risk of each shell course and the bottom is calculated from the POF and COF. The POF is defined as a loss of containment and the COF is defined as the effects of the loss of containment.
The API 581 POF is the product of a generic failure frequency, a damage factor, and a management systems factor. Generic failure frequencies are detailed in API 581 Part 2 and are based on actual industry failure data for different component types, including tank shells and bottoms. The generic failure frequency is intended to be the failure frequency of a component prior to any specific damage occurring from exposure to the operating environment. A damage factor is determined based on the applicable damage mechanisms (e.g., local or general corrosion, environmental cracking, etc.) relevant to the materials of construction, the process service, the physical condition of the component, and the inspection techniques used to identify and quantify damage. The effectiveness of past inspections is accounted for during the damage factor calculation. The management systems factor is the result of an evaluation of a plant’s process safety management (PSM) program through a series of questions answered by various site personnel and has a value between 0.1 (best PSM practices) and 10 (worst PSM practices).
Per API 580, all applicable damage mechanisms should be considered in the RBI assessment. Some of the more common ones for storage tanks are internal corrosion (shell and bottom), soil-side corrosion (bottom), external shell corrosion/corrosion under insulation (CUI), and various cracking mechanisms. API 581 provides a means to calculate bottom corrosion rates based on various factors such as operating temperature, soil resistivity, soil-side pad type, presence of drainage, cathodic protection, and use of water draws. Similarly, API 581 also provides a method of determining CUI corrosion rates as a function of the operating temperature, external environment, insulation type, and insulation condition. There are also calculation methodologies for various stress corrosion cracking mechanisms. All of these procedures use data that is easy to determine and very basic to a tank’s design.
In terms of COF, the methodology in the current edition of API 581 allows the determination of the shell course COF to be based on both safety area (like other fixed equipment covered by API 581) and in terms of financial consequence. In API 581, a tank bottom’s COF is determined strictly using a financial consequence analysis. The financial consequence of a bottom failure is the sum of three costs: environmental clean-up, repair, and production. The environmental clean-up costs are calculated by determining the volume of the product lost during a leak or rupture and estimating where that volume may migrate, such as (1) in the dike, (2) outside the dike but onsite, (3) outside the dike and offsite, (4) in the subsurface soil beneath the tank’s bottom, (5) in the groundwater, and (6) in the surface water. Figure 1 (from API 581) provides an illustration of these locations relative to the tank.
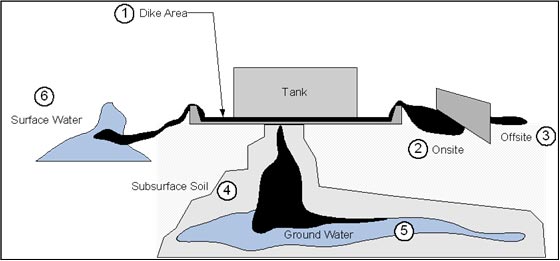
Repair costs are based on the likelihood of the tank suffering a leak related to various holes sizes and the cost of repairing each hole size. Production costs (i.e., business interruption) are based on the outage days to repair a leak and the daily cost of the tank being out of service. The specific calculations to determine repair and production costs are detailed in Part 5 of API 581.
In addition to assessing financial risk, modeling tank shell COFs based on safety risk allows for a more rigorous calculation of safety area consequence associated with a loss of containment, particularly for services that can have substantial flammable or toxic consequences. This is often used with stored products, such as ammonia, where the safety risks are high. In this methodology, the inventory of the various shell courses and properties of the stored product are used to calculate the impact area (in square feet) for equipment damage, personnel, and toxic injuries using the consequence analysis technology found in Part 3 of API 581. The largest of the three areas is chosen for the COF value used in the risk calculation.
Once the POF and COF are determined, they are multiplied together to calculate the tank’s risk of failure. This risk is used to plan inspections as shown in Figure 2. This graph shows how risk may increase after installation, continue through the RBI date (analysis date), and increase until the risk target is exceeded. When the risk of a tank’s component reaches a defined risk target (or threshold), an inspection activity of sufficient effectiveness is required and the inspection due date is established. Once the inspection activity is performed, the confidence in the known damage state increases, the uncertainty of it decreases, and the risk is lowered in proportion to the effectiveness of the inspection executed. An “A” inspection equates to a Highly Effective inspection, whereas an “E” inspection indicates an Ineffective inspection. API 581 provides guidelines for inspection effectiveness for various damage mechanisms and components. For example, an “A” external thinning inspection for uninsulated shells would require >95% visual inspection with UT or pit-gauge follow-up as needed.
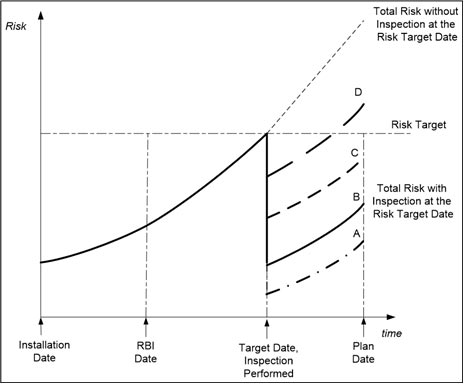
The Case for Quantitative Tank RBI
Quantitative tank RBI, if appropriately documented, is repeatable. As required by most inspection codes and company IMPs, an RBI program should not be a one-time study but should be reviewed and updated after inspections, after unplanned events, after changes in operation or service, or at a prescribed interval to keep future inspection plans up to date. While qualitative RBI is subjective, a documented quantitative assessment, regardless of personnel turnover, can be updated with new information and rerun with the knowledge that the future assessments are consistent with earlier ones. For reasons of consistency and repeatability, quantitative RBI is also more defensible if jurisdictions require convincing that RBI should be allowed to determine an inspection due date or defer an upcoming inspection. E2G has represented several owner-users when presenting tank RBI usage arguments in various jurisdictions. This consistency and repeatability are appreciated by the regulators. Moreover, the publicly available and well-documented tank RBI calculations in API 581, sourced from current consensus industry technology, provide a persuasive case for quantitative RBI in these discussions.
Tank FFS and Quantitative Tank RBI in Comprehensive Assessment
For tanks in safety critical services, a more rigorous program of tank RBI combined with proactive tank FFS may be desirable. Some types of tank FFS that may take place are brittle fracture screening, the proactive development of permissible crack-like flaw sizes prior to inspection, the proactive development of permissible CUI contours prior to inspection, and the determination of critical areas for concentration of inspection activities. For example, proactive crack-like flaw or CUI assessments may indicate certain shell courses, stiffener locations, nozzles, or other tank locations where inspection should be concentrated. If an inspection effectiveness category required 50% of some type of inspection nondestructive examination (NDE), the areas determined most critical by proactive FFS should be targeted among this 50% considered for inspection. Additionally, the proactive FFS can also provide the pass/fail criteria for the eventual inspection(s) of these same areas.
Uses of Quantitative Tank RBI
RBI is not just for one-off deferrals of storage tanks inspections. RBI implementation of all tanks in a facility can be used to develop a basis for prioritization and an optimized inspection schedule. Since a calculated financial risk is considered, the quantitative API 581 tank RBI will focus the inspection budget on the tanks, tank components, and damage mechanisms that are driving risk.
RBI can also be used to evaluate what impact a change in service will have on a tank’s inspection frequency, or to perform a due diligence review of a site with many tanks being considered for purchase. With many companies considering changing to the production of renewables, changing operating plants to terminals, or selling assets, tank RBI can be an invaluable tool to evaluate the viability of these changes.
Finally, RBI can be performed in the design phase (or when evaluating modifications) to determine what design features improve a tank’s long-term IMP costs. Since API 581 tank RBI is financial-based, the upfront costs of thicker bottom plate (or annular plates), use of cathodic protection, or the installation of a release prevention barrier can be compared to the long-term risk reduction and inspection savings they generate.
E2G’s Tank RBI Consulting Services, Practices, and Software
E2G has performed tank RBI on thousands of storage tanks covering a multitude of products and tank designs: from simple, small API 650 tanks storing refined products and chemicals to API 620 double-containment tanks storing ammonia and various liquified gases. To enhance the API 581 technology, E2G has developed methods for evaluating the POF of complex designs features used in some of the industry’s most severe services. We have put our knowledge of storage tanks, tank RBI, and tank FFS into Equity Engineering Practices (EEPs) and software (API RBI and SagePlus™) to help terminal and plant facility personnel with their tank IMPs. E2G continues to advance technology in tank RBI, and RBI in general, by performing cutting-edge research and development to develop software tools and procedures to improve industry practice.
For more information on tank RBI, contact Joel Andreani and Phil Henry by filling out the form below: