Did you know 66% of turnarounds (TARs) finish late and overrun budget by 10% or more? In fact, 40% of TARs exceed budget by 30% or more, costing facilities tens of millions of dollars. There are several key strategies to the execution of a successful TAR such as project scope management, minimizing schedule delays, controlling costs, and transparent communication. These strategies can be employed through planning and execution of the following five main TAR stages. E2G can support our clients with any one of these stages.
- Setting Goals (Budget, Reliability/Capital Improvements, Production Plan, and Market Influence)
- Scoping Phase (Planned Repairs, History, RBI Inspections, Proactive FFS, etc.)
- Detailed Planning (Job Plans, TAR Organization, Gantt Charts, Securing Labor Resources)
- Execution (Damage Assessment [FFS], Execution of Improvements, Inspection/NDE, Repairs, etc.)
- Post-TAR Planning (Planned Repairs Next TAR, Lessons Learned, Update RBI, etc.)
This article focuses on the Execution stage of the TAR for an efficient triage of new inspection discovery. The nightmare of any TAR manager is the discovery of unanticipated damage to a piece of equipment that results in a new critical path which extends the TAR and overruns the budget. Based on a 15-year average US refinery profit margin of $17.50 per barrel of crude, the average TAR outage costs $2.5 million/day ($105,000/hr) in lost opportunity for an average US refinery production rate of 145,000 bpd. Daily maintenance costs can increase this loss rate. There are large economic advantages, such as minimizing lost opportunity costs, to reducing schedule delays during TARs. This article focuses on the advantages of properly staffing a TAR Problem-Solving Team to resolve equipment inspection discoveries quickly and efficiently to help minimize lost opportunity costs. Although not a topic for this article, the execution of proactive FFS can also have a significant reduced in triage execution time for expected/known damage (e.g., tower Tmins, local thin area [LTA] assessment for local corrosion under insulation [CUI], critical flaw sizing, etc.).
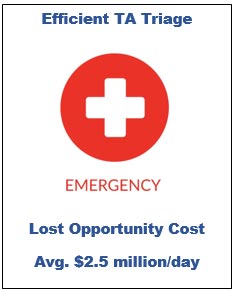
Resolving TAR Discovery Items
Historically, the resolution of equipment inspection discovery has been resolved by four different groups:
- Unit/Contract Inspectors
- Maintenance Engineers
- TAR/Project Engineers
- TAR Problem-Solving Team
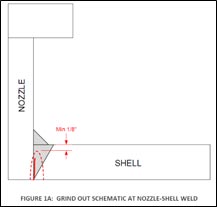
The first three groups each have a particular skill set that can be utilized during the TAR. However, these groups typically do not have the necessary skill set to provide quick and efficient resolution to damage requiring Fitness-for-Service (FFS) during a TAR. Additionally, they may not be able to identify and resolve the impact a particular repair path might have on refinery operation/economics. Often these situations are resolved by reaching out to an outside contractor or corporate office engineer who specializes in these assessments, both of whom may not share the same desire for urgent resolution of the matter as needed during a TAR. Delays in getting full engagement can be measured in days, especially if travel is required. Such delays could result in an extension to the TAR (if critical path) and large dollars in lost opportunity. The best approach to improve efficiency and reduce lost opportunity costs is the creation of a Problem-Solving Team that meets daily to log new discovery, discuss plans for resolution of discovery, and report on resolution of old discovery items. Such a team should be comprised of experienced engineers with expertise in damage mechanisms, FFS, ASME and API equipment/piping design, welding/materials, repair plans, plant operations, and TAR execution. E2G has provided support to supplement these lacking skill sets among plant personnel to aid in operations and TAR execution. E2G has a wealth of experience with such skill sets as they were the lead author for industry standards on damage mechanisms (API 571), fitness-for-service (API 579-1/ASME-FFS-1), and equipment design (ASME Section VIII Division 2) along with active participation in industry standards (API 579 and various API equipment standards, ASME B31.3, ASME Section VIII Divisions 1 and 2, NACE, etc.).
TAR Problem-Solving Team Structure
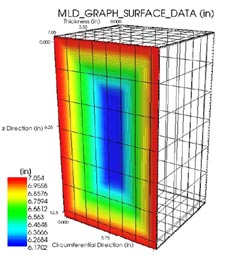
Depending on the size of the TAR, E2G has provided Problem-Solving Teams that range from one mechanical engineer to as many as five engineers and specialists (materials, welding, mechanical) to support the facility’s Problem-Solving Team. Regardless of the number of engineers assigned to the TAR, the client will have access through the engineer(s) to the many years of mechanical, materials, and welding engineering experience within E2G. Such a team ensures timely execution of ASME Code and FFS calculations to establish remaining life, creation of weld and PWHT procedures, material selection for improved reliability, and resolution of unique problems. Execution of TAR support has typically been performed onsite, providing 10 to 12 hours of support 7 days/week ranging from 2-6 weeks during the TAR. Onsite support allows for in-person communication, visual inspection of the damage, field measurements, in-field inspection guidance, gathering of equipment documentation, and TAR execution meeting attendance.
ON-SITE TAR SUPPORT
Remote TAR Support Has Its Advantages
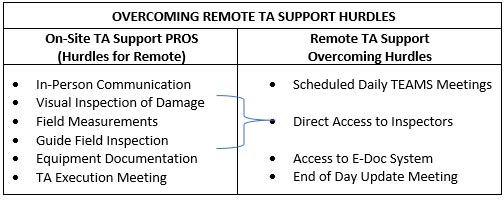
Prior to the pandemic, and especially during the pandemic with COVID-related travel restrictions, E2G has provided remote TAR Problem-Solving Team support. Although there are some limitations with remote support, well-designed and well-managed remote TAR support can overcome these hurdles. It is very important to have daily scheduled meetings with the Problem-Solving Team within E2G and with the site personnel to ensure the flow of new discovery and resolution of old discovery. Direct access to the site inspectors (company or contractor) for discussion of discovery items, requests for follow-up inspection, and field dimensions and photos are critical. There are too many delays and potential miscommunication if an intermediate company site personnel is utilized. Lastly, access to the site electronic documentation system (E-Doc) is required to avoid delays in obtaining the required equipment information for assessment. These items can go a long way to reduce and even eliminate remote support hurdles.
OVERCOMING REMOTE TAR SUPPORT HURDLES
Once the hurdles are addressed, remote TAR support has been proven to provide several pros such as elimination of on-site safety risk, elimination of safety training and travel costs, and a larger resource pool to allow parallel execution of work as needed. An additional benefit is the back office face-to-face interaction amongst E2G’s experts for efficient resolution for the more challenging discovery items. Recent remote TAR support utilized Microsoft Teams for real-time file sharing and review/updating of files (SharePoint behind the scenes). Teams file sharing eliminated the inundation of emails and proved to be a more organized process of sharing and reviewing files, which should be implemented whether on-site or remote support is being provided.
REMOTE TAR SUPPORT
E2G’s TAR Problem-Solving Team Solution
A properly staffed Problem-Solving Team can significantly reduce the resolution time for new discovery and in turn minimize the potential for a possible TAR extension and the associated millions per day lost opportunity costs. With properly structured plans, both on-site and remote Problem-Solving support has been proven effective. Whatever the choice for your Problem-Solving Team structure, E2G can support your needs.
For more information on executing a TAR, please fill in the form below or contact us to request access to watch the June 2021 webinar.