Deteriorating structures, foundations, and other infrastructure cost U.S. businesses billions of dollars per year. Oil & gas, petrochemicals, and other process industries are not immune to the problems deteriorating infrastructure can cause. Problems with structures and foundations, much like mechanical equipment, are a result of design deficiencies, construction defects, deteriorating conditions, extreme environmental events, and changes in applied loads. Much like a Mechanical Integrity (MI) program, an effective Structural Integrity (SI) program should address all aspects of the life cycle of a structure from design to retirement. An effective SI program must be multidisciplinary and informed by knowledge of a myriad of industry codes and standards (RAGAGEP). In this article, we will answer several key questions related to SI programs that should help you develop or improve you own program, and some of the related products and services the E2G | The Equity Engineering Group, Inc. has developed to meet your SI needs.
What are the Basic Components of an SI Program?
What structures and foundations should be included in a sound SI program? At a minimum, structures supporting equipment and piping covered in the MI program should be included in the SI program, along with some other structures that might not be as obvious. These are the OSHA 1910 Subpart D Safety Structures (walking surfaces/platforms, ladders, etc.) that have a very direct impact on personnel safety.
What RAGAGEP knowledge is required? There are numerous structural codes and standards, recommended practices, and publications that form RAGAGEP for process industry structures and foundations. The primary code organizations for structures and foundations in the United States are the American Society of Civil Engineering (ASCE), the American Concrete Institute (ACI), the American Institute for Steel Construction (AISC), and the International Building Code (IBC). There are numerous other standards and publications that can be considered RAGAGEP for in-service structures that are analogous to some of the API MI and PCC standards.
What Inspection, Testing, and Maintenance of Structures and Foundations are Involved?
How, when, and where do I inspect?
These key questions answered in an MI program are equally important in an SI program. E2G has created a Special Emphasis MI program (SEMI) for structures in our Equity Engineering Practices (EEPs) which includes best practices for inspection and testing of structures and foundations, among other RAGAGEP for in-service structures. The EEPs address these three key questions.
How do I inspect?
Inspection and testing of structures and foundations may involve some of the similar inspection techniques used with facility equipment (visual inspection, ultrasonic thickness inspection, and various surface crack inspections). Techniques outside of the normal realm of fixed equipment inspections are generally related to concrete inspection and may include coring, acoustic methods, radar techniques to locate reinforcing steel or buried structures, various probes and rebound hammers to measure condition, and other specialty techniques. The EEPs discuss where each of these techniques is best used and what ASTM or other standard is the basis for the technique.
When do I inspect?
There is no single, equivalent industry standard for prescriptive structural inspections of the non-building type structures found in process facilities. Building codes have some basic inspection interval requirements, but the types of structures and expected types of damage found in process facilities differ from the structures typically covered in the building codes. E2G has developed a grading or classification system, like that used with piping and equipment, to determine prescriptive inspection intervals, as well as a risk-based approach to determining inspection frequency. In the prescriptive approach, certain structures, such as frames supporting elevated heavy equipment or dynamic loads, have prescribed initial inspection intervals shorter than those of on-grade or near-grade structures supporting lighter equipment, shorter vertical vessels, or small drums.
In the risk-based approach, E2G has developed a procedure (and tool) to prioritize inspection needs for structures based on probability of failure (POF) and consequence of failure (COF). The procedure accounts for the complexity and use of the structure, its built-in redundancy, its age and condition, inspection and maintenance history, COF of the supported equipment, personnel safety aspects of a structure, and similar factors. Risk can be plotted on a risk matrix (Figure 1) and used to guide inspection focus and frequency.
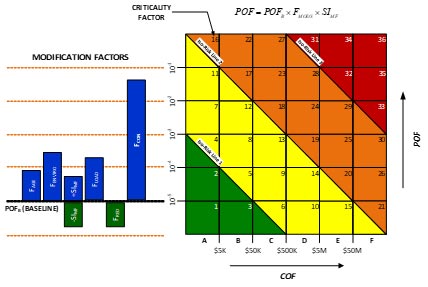
Where do I inspect?
SI monitoring locations (SIMLs) can be established for various types of structures based on the criticality of the structural member and the type(s) of loads supported. Our EEPs provide guidance on structure inspection SIMLs. Data at SIMLs should be electronically stored and evaluated to determine the next inspection interval, whether determined in a prescriptive or risk-based manner.
How Do I Do a Structural Assessment or Repair?
Finally, what do I do if I find a problem with a structure, want to repurpose a structure, or plan to modify equipment supported by a structure? Addressing these issues involves many of the same steps found in the evaluation of existing equipment: performing inspection(s), identifying applicable damage mechanisms, calculating structural loads, designing repairs and/or mitigation systems if necessary, and determining the need for future monitoring.
There is no single equivalent standard to API 579-1/ASME FFS-1 (API 579) for structures when performing a reassessment. The new International Existing Building Code (IEBC, formerly Chapter 34 of the IBC) provides some guidance, but much of the evaluation, particularly of damage, requires good engineering practice. Like any FFS evaluation, the evaluation of existing structures is a multidisciplinary effort involving engineers knowledgeable in the design of structures and foundations, engineers with process equipment expertise, and inspection personnel. Often, a key to the evaluation is the interaction of the equipment (or piping) and the structure itself (stiffness/natural frequencies, temperature effects, etc.).
Optimally, engineers evaluating process facility support structures will be knowledgeable in the equipment and piping design (ASME, API, etc.) as well as the structural design (ASCE, AISC, ACI, etc.). E2G’s Mechanical & Structural (M&S) Engineering team has engineers with this breadth of expertise. We have evaluated numerous structures for fitness, repurposing, increasing loads, and mitigating equipment (or piping) problems such as mechanical vibration.
When repairs or modifications are required, there is no single U.S. standard for structural repair like the ASME PCC standards. Alterations and repairs can take many forms including: the replacement, addition, or reinforcement of members; grouting and stitching concrete cracks; post-tension repairs of concrete; and shoring, underpinning, and ground improvement for foundations. The M&S team and the EEPs can provide assistance with structural repairs (Figure 2).
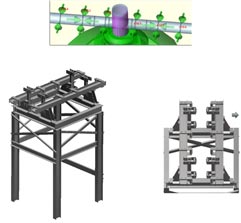
How Good is My Current SI Program?
Is your current SI program robust?
Much like our MI gap assessment consulting service, E2G can evaluate the SI program at your site. A gap assessment can not only determine inadequacies in your current SI program, but it can help identify ways to elevate your SI program to industry best practice level. We believe an SI program should be part of any comprehensive MI program. Without question, a sound SI program will improve safety, improve facility reliability, and improve environmental performance!
For more information on our SI services, please fill in the form below.