RELIABILITY. INTEGRITY. SAFETY.
FOCUSED ON WHAT MATTERS TO YOU.
Safe operation of your equipment and facilities is essential to protecting your employees, the community, and the environment. You need to be confident in the long-term reliability and safety of all equipment and assets in an industrial plant.
At Equity, our engineering and consulting services are focused on managing the entire asset lifecycle to provide you with practical recommendations to improve safety, increase equipment reliability, and mitigate risk
- Home
- Engineering
Asset Lifecycle Management
Adopting an equipment lifecycle management process will help you to reduce risk, optimize design and construction, predict future maintenance and inspection costs, maximize equipment availability, and comply with local regulations.
Our engineering consulting services are focused on delivering a comprehensive asset lifecycle management framework, including:
- Damage mechanism identification
- Construction codes and design standards
- In-service maintenance and inspection planning
- Fitness-for-Service (FFS) and Suitability-for-Service (SFS) standards
- Post-construction and repair guidelines
Consult With Our Experts
Engineering Service Areas
Promote compliance, safety, and reliability across all facilities using standardized Best Practices to improve the quality of engineering programs, project execution, and asset lifecycle.
Identify and understand potential damage mechanisms that may cause equipment failure or create adverse operating or maintenance issues.
Achieve safe, efficient, and reliable operations by implementing proactive and reactive MI strategies that address every stage of an asset’s lifecycle.
Assess the structural integrity of assets and components to proactively increase operational safety, minimize failures, and save money.
Ensure that safety critical pressure relieving systems provide adequate protection to processes and meet the latest RAGAGEP.
Refocus maintenance dollars to priority areas by using risk as a basis for prioritizing and managing in-service inspection programs.
Identify the highest-risk equipment and piping systems, prioritize field screening, and decrease the risk of vibration fatigue failures.
Increase operational reliability and extend equipment life by making informed run, repair, or replace decisions on in-service equipment.
Establish measurement objectives and constraints to improve the safety and reliability of instrument and control systems.
Industry Insights
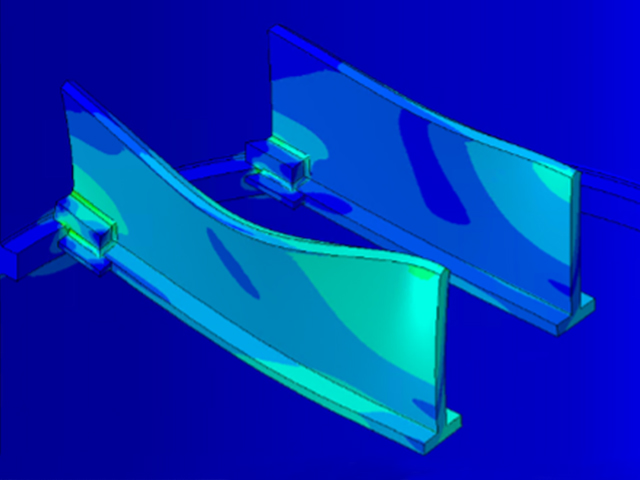
Structural Engineering Applications for Fixed Equipment Analysis
Typically, maintenance teams are focused on a facility’s pressure vessels, piping, and tanks, which leaves structural infrastructure to be overlooked. In this article, Derek shares several case studies that highlight how combining structural and mechanical engineering approaches can solve several unique fixed equipment challenges.
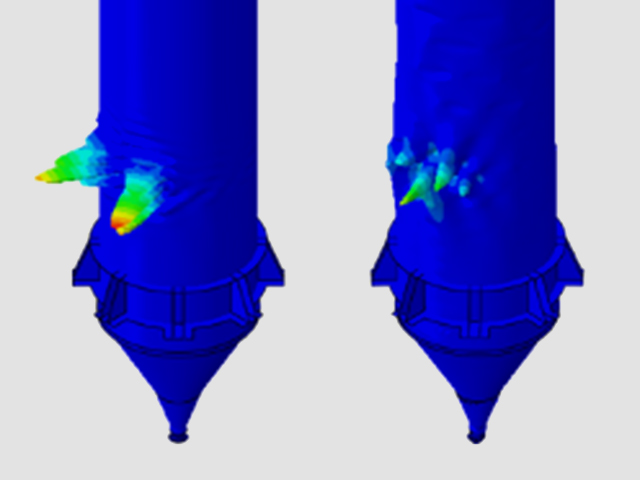
ASME Silo Design: An Introduction to ASME SBS
Up until the recent publication of ASME SBS-2023: Structures for Bulk Solids (ASME SBS), there has not been a comprehensive American standard for the design and construction of metallic structures