- Home
- Engineering
- Materials & Corrosion
- Weld Repair
WELD REPAIR & HOT TAP ASSESSMENTS
Why Do You Need a Welding Assessment?
Understanding the residual stresses associated with welds in pressure vessels, piping, and other structures is essential when designing or repairing equipment for the oil and gas, petrochemical, chemical, fertilizer, and other industrial processing industries. However, it’s important to know the differences between repair welding versus fabrication. Knowing those differences and applying that knowledge in the field will prevent catastrophic failures.
Equity’s welding engineers will review your current welding procedures and provide practical repair guidance for any type of damage mechanism to ensure new construction or planned maintenance is compliant with the latest industry standards.
Equity's Weld Repair & Hot Tap Assessment Services
Review welding procedures and provide inspection recommendations
Determine materials or filler electrode requirements
Conduct onsite failure analysis and root cause investigations
Specify weldability concerns and discuss welding metallurgy
Identify preheat, interpass, and post-weld heat treatment requirements
Provide technical advice on welding and fabrication
Conduct cleaning and preparation
Hot Tap Assessment
In-service welding, or hot tapping, is required when in-service equipment needs repairs or when nozzles, tees, sleeves, or other fittings need to be added without bringing the unit offline. However, if fluid dynamics, heat transfer, and welding parameters aren’t properly understood, the result can be catastrophic. We perform detailed hot tap assessments to provide optimized welding parameters that address the risks of burn-through, fluid decomposition, unintended chemical reactions, and delayed weld cracking. We also offer practical guidance related to hot taps.
Our hot tap assessment services include:
- Evaluate high-risk scenarios on a case-by-case basis
- Develop special guidance for preparation, including washout or flush for contaminated services
- Perform detailed sensitivity analysis modeling to identify changes in fluid conditions
- Address specific application risks (e.g., fluid decomposition, or unintended chemical reactions)
- Recommend modified welding parameters and techniques
- Develop specific inspection recommendations
- Calculate mechanical loads and design loading for existing piping system during and after the hot tap connection
Repair Welding
There are many nuances associated with carrying out repair welds. When repairing in-service equipment, it is essential to understand equipment metallurgy, material properties, potential damage mechanisms, welding procedures, inspection techniques, and many other variables.
At Equity, we help you with:
- Weld solidification and liquation cracking
- Preheat, interpass, or post-weld heat treatment (PWHT) limitations
- Weld corrosion or stress corrosion cracking (SCC)
- Welding of in-service pipelines
- Weld residual stress and distortion
- Dissimilar materials welding
- Cladding or buttering requirements
- Failure investigation, analysis, and root-cause analysis
- Inspection recommendations
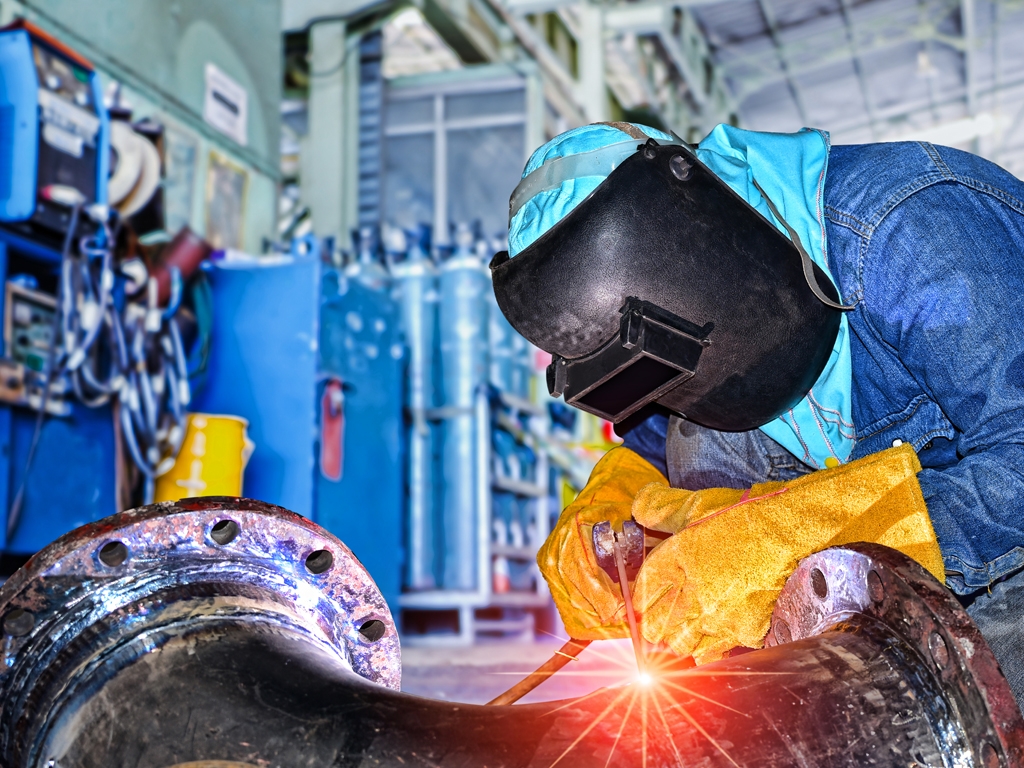
Post-Weld Heat Treatment (PWHT)
PWHT effectively minimizes weld residual stresses in pressure vessels and piping equipment. Conducting PWHT on carbon and other low-alloy steels will generally help mitigate the risk of crack initiation and ultimately, brittle fracture; however, PWHT layouts need to be properly engineered. Equity routinely provides practical recommendations for local PWHT layouts and heating parameters to mitigate the risk for weld cracking or distortion due to severe metal temperature gradients.
Creep Damage
Creep damage progression is known to be accelerated by the mismatch in creep properties of the weld deposit, heat-affected zone (HAZ), and adjacent base metal. This property mismatch results in stress intensification and triaxial tension that can accelerate creep damage near the weldment. Equity specializes in high-temperature analysis of welds and can offer practical inspection guidance for components operating in the creep regime.
The cloud-based eecHotTap software tool assesses the suitability of hot tap welding procedures or repair welds by evaluating the risk of burn-through and cold cracking due to rapid cooling. eecHotTap uses the latest advances in weld thermal simulation technology to:
- Support historic eecHotTap welding models, including weldolets and user-defined custom fluid mixtures
- Use finite element analysis (FEA) solver to simulate the weld’s thermal history
- Evaluate the effects of preheating
- Analyze liquid boiling cases, including nucleate, transition, and film boiling
Recommended Reading
- Brittle Fracture /
- Industry Insights /
- Library /
- Mechanical & Structural Engineering /
- Welding /
- Creep /
- Industry Insights /
- Library /
- Materials & Corrosion /
Weld Repair Expertise
We provide practical repair guidance for any type of damage or for planned equipment modifications based on years of welding experience and advanced analysis. Equity’s welding engineers will review current company welding procedures and provide general repair guidance to ensure the construction of high-quality welds that are compliant with industry standards.
Our experts:
- Have 350+ years of combined field experience
- Pioneered development of FFS and RBI
- Are the primary authors on WRC 528 and WRC 562
- Serve as lead investigators on API 579-1/ASME FFS-1 and API 571
- Provide on-site support within 24 hours