FITNESS-FOR-SERVICE (FFS)
- Home
- Engineering
- Fitness-for-Service (FFS)
Make Informed Run, Repair, or Replace Decisions
Fitness-For-Service (FFS) is a multi-disciplined engineering assessment used to make run, repair, or replace decisions for equipment or piping systems that contain a flaw or are subject to a particular damage mechanism. FFS assessments are also used to determine remaining life and to optimize inspection plans (including inspection techniques and inspection frequency).
Implementing FFS into an asset’s lifecycle management program will improve safety, reduce risk, optimize design, maximize equipment availability, and reduce future maintenance and inspection costs. Our Mechanical and Structural engineering team provides proactive and reactive FFS assessments to help you extend equipment life and safely justify continued operation with known damage or defects.
Learn More About Fitness-for-Service From Equity's Experts
What is Fitness-for-Service
FFS assessments are conducted on in-service equipment to assess the structural integrity of pressure vessels, piping, and tanks to determine whether the component is fit for continued operation or if the flaw or damage will cause a failure. Implementing FFS into an asset’s lifecycle management program will improve safety, reduce risk, optimize construction, maximize equipment availability, and reduce future maintenance and inspection costs.
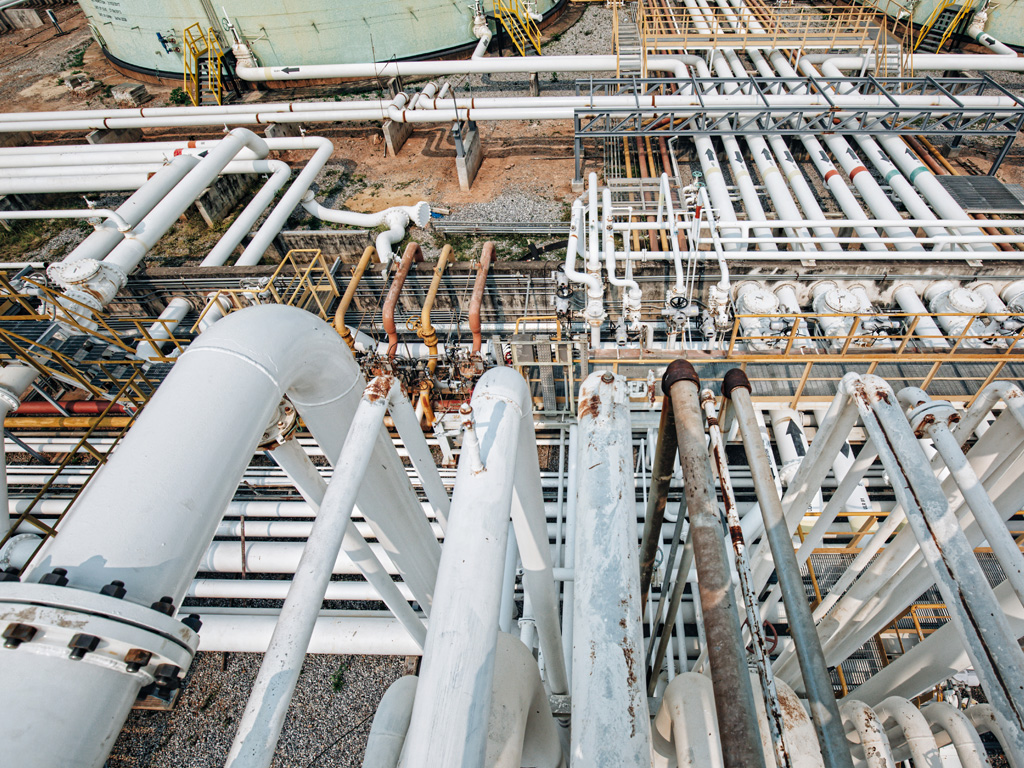
Proactive vs. Reactive Fitness-for-Service
FFS is typically used in a reactive mode to assist with critical run, repair, replace decisions once flaws or damage are discovered. Equity recommends implementing FFS technology proactively and reactively throughout your asset integrity management program to extend equipment life and optimize inspection plans and mechanical integrity decisions.
Proactive Fitness-for-Service
When? FFS technology can be utilized proactively to optimize decisions at every phase of the equipment lifecycle management process.
Benefit?
- Extend equipment life, and optimize equipment design, and refine inspection intervals and tasks
- Determine go/no-go acceptance criterion before an inspection
- Understand the effects and potential for future damage progression
- Establish screening tools to aid in non-destructive examination (NDE) and flaw sizing exercises
Reactive Fitness-for-Service
When? FFS assessments are traditionally used to determine whether equipment or piping systems are safe for continued operation with the presence of some type of damage or defect that is detected during planned outages or on-stream inspections.
Benefit?
- Make informed run, repair, or replace decisions on in-service equipment
- Determine future inspection or outage intervals
- Develop repair procedures
Equity's FFS Assessment Workflow
Our mechanical and structural engineering team combines the appropriate level of technology with their extensive industry experience to provide practical and cost-sensitive recommendations to challenging FFS problems. Our team offers many related services to help improve the reliability of and extend equipment life, from both a reactive and proactive approach, including:
- Brittle Fracture Screening and Minimum Pressurization Temperature (MPT) evaluations
- Volumetric Metal Loss
- Crack-like Flaw Assessments
- Turnaround support
- Distortion and Tank Edge Settlement
- Creep and Fatigue Life Estimation
- High Temperature Hydrogen Attack (HTHA)
- Mechanical Vibration of piping systems or equipment
- Fire Damage Assessments
Issue: The client identified multiple regions of extensive localized wall loss during a plant outage. Upon closer inspection, the damage was due to corrosion under insulation (CUI).
Solution: Our team performed a Level 3 FFS assessment to determine whether the process column could be placed back into service without repair. To prevent any delay in the process unit startup, an assessment was needed on an expedited timeline. The speed at which the assessment was completed was only feasible due to Equity’s tools and expertise in executing similar assessments.
Result: The assessment results provided the justification needed to continue safely operating the equipment without repair. The client was able to start-up the process unit without any delay.
Atmospheric storage tanks can present unique challenges that require experienced personnel. We combine the principles of API 653 and API 579-1/ASME FFS-1 to improve safety and reduce unnecessary and untimely maintenance costs on ASTs. We conduct FFS assessments to address a wide array of damage including shell distortions, foundational settlement, environmental damage, and corrosion issues.
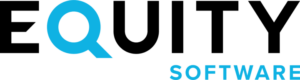
Equity Software: Evaluate & Analyze In-Service Equipment
Use Equity Software tools to conduct comprehensive evaluations and FFS analyses of the design, condition, and compliance of both new and in-service equipment. Equity Software offers multiple cloud-based options to help you achieve accurate Level 1, Level 2, and Level 3 FFS assessment results quickly and easily.
PlantManager SAGE is a collection of mechanical engineering and FFS modules for evaluating and analyzing the design, condition, and compliance of new and in-service equipment. PlantManager SAGE leverages SagePlus to incorporate the latest API 579-1/ASME FFS-1 standards to deliver accurate FFS assessment results quickly and easily.
Automated Finite Element Analysis Tools automates the entire Level 3 assessment workflow, making detailed FFS evaluations as accessible as traditional Level 2 methods. Use the new automated FEA tools for nozzles, pipeline dents, aboveground storage tanks, and local thin areas.
SIMFLEX-IV is a cloud-based piping stress analysis software for preventing potential failures by improving the structural integrity of piping systems and supporting structures. Calculate spring hanger design, rotating equipment load compliance reports, anchor and support load combination tables, and nozzle stresses, all in one run.
Equity's Role in Advancing FFS Methodologies
Our engineers pioneered the advancement of FFS technologies and were the lead investigators of the international standard API 579-1/ASME FFS-1, Fitness-for-Service. Today, the document is the FFS standard of choice for other industries such as pulp & paper, biofuels, food processing, and non-commercial nuclear.
Equity was the lead investigator of API 571, Damage Mechanisms Affecting Fixed Equipment in the Refining and Petrochemical Industry. Understanding the effects of and potential for future damage progression is critical in completing an effective FFS evaluation.
Recommended Reading
- Fitness-for-Service (FFS) /
- Industry Insights Articles /
- Mechanical & Structural Engineering /
- Turnarounds /
- Fitness-for-Service (FFS) /
- Industry Insights Articles /
- Mechanical & Structural Engineering /
- Midstream & Pipelines /
- Software /
- Industry Insights Articles /
- Mechanical & Structural Engineering /
- Storage Tanks /
- Structural Engineering /
- Fitness-for-Service (FFS) /
- Industry Insights Articles /
- Mechanical & Structural Engineering /
- Turnarounds /
- Brittle Fracture /
- Fitness-for-Service (FFS) /
- Industry Insights Articles /
- Mechanical & Structural Engineering /
- Fitness-for-Service (FFS) /
- Library /
- Mechanical & Structural Engineering /
- Midstream & Pipelines /
- Fitness-for-Service (FFS) /
- HTHA /
- Library /
- Materials & Corrosion /
- Mechanical & Structural Engineering /
- Webinars /
- Fitness-for-Service (FFS) /
- Industry Insights /
- Library /
- Mechanical & Structural Engineering /
- Risk-Based Inspection (RBI) /
- Turnarounds /
- Fitness-for-Service (FFS) /
- Industry Insights /
- Library /
- Mechanical & Structural Engineering /
- Tanks /
- Industry Insights /
- Library /
- Mechanical & Structural Engineering /
- Mechanical Integrity /
- Suitability-for-Service (SFS) /
Fitness-for-Service Expertise
Our mechanical and structural engineering team has completed thousands of FFS assessments for pressure vessels, piping systems, and storage tanks. As pioneers of FFS technologies and lead investigators on many international standards, our team combines their extensive experience with state-of-the-art technology to help extend the lifecycle of your existing assets and create safe operating environments.
Our experts:
- Have 200+ years of combined field experience
- Pioneered development of FFS
- Are the primary authors on WRC 528 and WRC 562
- Serve as lead investigators on API 579 and API 571
- Provide emergency onsite support within 24-hours
- Are the committee leader for the- API 579 Part 3 brittle fracture screening task group