Introduction
Mechanical integrity (MI) programs are an important part of the safety and reliability of processing facilities. MI is one of the main components of OSHA’s Process Safety Management (PSM) of Highly Hazardous Chemicals, 29 CFR 1910.119. Special emphasis MI (SEMI) programs are a vital subset of an MI program that address specific critical processes, specific damage mechanisms, and/or specific equipment, piping, and/or structures with critical design, operations, and/or inspection considerations.
SEMI programs exist around three main categories:
- Process: SEMI related to specific processes or products such as hydrofluoric acid, ammonia, or chlorine
- Damage: SEMI related to specific damage mechanisms such as high-temperature hydrogen attack (HTHA), sulfidation, or corrosion under insulation (CUI)
- Equipment: SEMI related to specific equipment, components, or equipment geometries such as small-bore piping, injection & mix points (IPs/MPs), critical valves, critical flanges, or support structures
SEMI programs should address all phases of the life-cycle management of a facility’s assets (Figure 1) from the selection of materials and other design and operations considerations to the inspection, evaluation, maintenance, and repair of existing assets. E2G | The Equity Engineering Group, Inc., has developed numerous Equity Engineering Practice (EEPs) and consulting services that address these SEMI areas. This article explores some key considerations involved in any SEMI program.
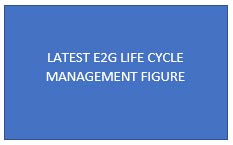
RAGAGEP Considerations
The integrity of equipment, piping, and structures affected by any one of these SEMI areas may require that attention be given to additional Recognized and Generally Accepted Good Engineering Practices (RAGAGEP). For example, ammonia production, storage, and handling RAGAGEP may include documents such as 29 CFR 1910.111 and various ANSI/CGA standards. In a fuel-grade ethanol (FGE) facility, the additional RAGAGEP may include API TR 939-D, Stress Corrosion Cracking of Carbon Steel in Fuel-Grade Ethanol: Review, Experience Survey, Field Monitoring, and Laboratory Testing, API Bulletin 939-E, Identification, Repair, and Mitigation of Cracking of Steel Equipment in Fuel Ethanol Service, and API RP 1626, Storing and Handling Ethanol and Gasoline-Ethanol Blends at Distribution Terminals and Filling Stations. These RAGAGEP supplement the basic RAGAGEP such as ASME Codes and API Standards with additional design, construction, location, safety, operation, and maintenance requirements that are good engineering practice. Design considerations in potential cracking services like ammonia or FGE may include additional stress relief and design details that reduce the concern for stress corrosion cracking (SCC). Safety considerations may include such things as siting, marking, and use of additional or specialized safety equipment.
For each of the SEMI categories identified earlier (process, damage, and equipment), there will be additional RAGAGEP to consider. E2G’s SEMI EEPs help our Practices users identify and use this additional RAGAGEP and guide them through the other components of an SEMI program.
SEMI Design and Operations Considerations
Each of the SEMI areas has additional design considerations, whether from the supplemental RAGAGEP identified previously or from other good engineering practice. The additional stress relief example was given before for equipment in SCC services. Other additional design considerations may include minimizing or eliminating the use of cold bending and forming, use of a reduced set of materials, certain fatigue-mitigating design details for nozzles and other components, etc. One example on the material selection side is the use of limited permissible API 620 materials on ammonia tanks with SCC concerns. Materials having tensile strength greater than 70 ksi (480 MPa) are generally considered more susceptible to SCC. Another example is the avoidance of some carbon steel materials, such as A53 pipe, in sulfidation service given low-silicon content. With some existing equipment and piping, retrospective PMI may also be called for when SEMI damage mechanisms like sulfidation are a concern. Corrosion control documents (CCDs) and integrity operating windows (IOWs) become an important consideration in these SEMI areas since the process and damage-related SEMI categories frequently involve temperature, pressure, water content, and other process variables that can significantly affect the integrity of the equipment. When equipment goes outside the ranges given in the IOW, an assessment of the impact of the excursions on the fitness of the equipment should be performed. In some cases, such as HTHA, short swings of temperature or pressure can significantly expose equipment to damage, and monitoring process conditions relative to the IOWs is crucial. For this reason, the quality of the instrumentation and process controls is also critical.
When being brought into or taken out of service, equipment in many of the SEMI program areas have additional considerations for commissioning, decommissioning, and even mothballing the equipment. Proper control of temperatures, pressures, oxygen content, and other variables during commissioning and decommissioning can be important to avoiding damage during start-up and shutdown.
The SEMI EEPs provide our Practices users with these additional design and operational considerations. E2G subject matter experts (SMEs) also provide consulting in the design of this specialized equipment for SEMI services, including material selection, design reviews, development of CCDs and IOWs, instrumentation and control designs for critical equipment, assessment of equipment having experienced process excursions, assessment of risk of brittle fracture, and guidance on commissioning and decommissioning equipment. E2G is advancing the technologies in areas like HTHA and developing tools to assess damage as well as assist in other assessments such as evaluation of safe shutdown conditions.
SEMI Inspection & Testing Considerations
Inspection and testing are a key part of any MI program, especially in SEMI program areas. Much like design and operations, there are additional inspection, testing, and preventative maintenance (ITPM) considerations in these services. With SEMI programs, the decision to defer an inspection that has been scheduled should be done with additional scrutiny, and in some SEMI services, not at all. In addition to when to inspect, some SEMI areas lead to additional scrutiny on how to inspect (what is the best technique? – spot or automated UT, RT, SWUT, etc.) and how much or where to inspect. One key question with SEMI service and equipment is where should condition (or thickness) monitoring locations (CMLs or TMLs) be located? As an example, our Injection & Mix Point EEP provides guidance on placement of CMLs for these types of systems (Figure 2).
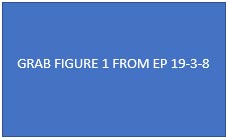
NOTE: Additional text and figures provide details on number and location of CMLs around components, such as bends, shown in the figure right.
As another example, injection or mixing point quills have additional inspection (and evaluation) needs. Fatigue and cracking issues may be a concern. E2G has performed numerous analyses of quill fatigue, including assessments involving advanced finite element analyses and computational fluid dynamics. Results of these assessments, and E2G’s expertise in piping vibration, have led to several best practices being written into our EEPs. In terms of inspection, SWUT should be done in quill areas as part of normal inspections. Infrared scans and additional inspections may be warranted if routine inspections show any fatigue concerns.
Finally, risk-based inspection (RBI) has a place in SEMI programs as a viable alternative to developing inspection plans with prescriptive intervals. The consequence of failure (COF) in many of the services covered by an SEMI program warrants additional care in the RBI process. Also, in these same services, the damage mechanism review (DMR) is possibly more critical than the DMR in processes not covered by an SEMI program. Materials & corrosion expertise, and personnel experienced in COF modeling, are even more crucial to the success of the RBI process in these instances.
Like any part of an MI program, proper documentation is key. In SEMI programs, equipment and locations, such as dead legs, should be specifically identified in the facility’s inspection data management system (IDMS). CML locations, thickness data, and other inspection results and recommended intervals should all be captured.
E2G’s SEMI Practices and Consulting Service
E2G is putting our knowledge of SEMI into practice–literally–in the form of almost two dozen SEMI EEPs covering processed damage mechanisms and equipment that deserve additional MI consideration. We are also providing consulting expertise in all the areas discussed in this article. We continue to advance technology in these areas by performing cutting-edge research and development to develop software tools and procedures to improve industry practice.
For more information on our MI-related services or our EEPs, contact Joel Andreani by submitting the form below: