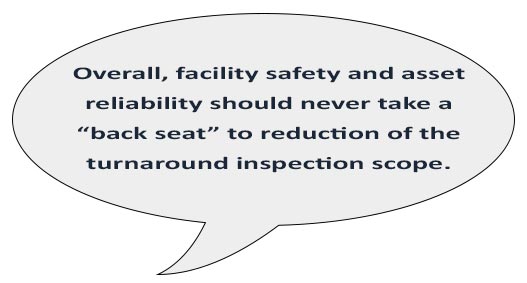
Introduction
Efficient completion of the turnaround (TA) work scope (i.e., scheduled maintenance) is arguably one of the largest factors in determining if a given site will satisfy the annual budget. Of course, opportunity feedstocks, increased charge rates, unplanned shutdowns, among many other items can significantly impact the annual budget. However, when the opportunity cost impact of a TA is millions of dollars a day, time becomes the most important factor when aiming to meet budget. As a result, most facilities should begin planning for a TA several years ahead of the planned shutdown. Essentially, the cost impact to the facility due to a TA can be managed by minimizing the unplanned work scope (safety and reliability not withstanding) and proper planning to minimize the overall downtime required to complete the work scope. Additionally, if TAs are executed properly, then the frequency of unplanned shutdowns should greatly diminish, again aiding in satisfying the annual budget. TAs are an investment in the reliability and future performance of a site’s assets.
Inspection Prioritization and Risk-Based Inspection
When evaluating the TA work scope, the first premise that should be challenged is “what assets am I inspecting, and why?” Many modern mechanical integrity (MI) programs will rely on risk-based inspection (RBI) to determine what assets will require inspection for a given TA. In general, a facility will aim for a maximum allowable risk target (often company-specific), and if a piece of equipment is approaching the allowable risk target then an inspection will be performed.
Equipment risk is often used to evaluate if an inspection is required during the upcoming TA or if it can be reserved for a later date. The risk for a given vessel is partly defined by probability of failure, which is further defined by the applicable damage mechanisms. The importance of the RBI program having been recently verified then becomes readily apparent.
In a hypothetical situation where the applicable damage mechanisms have not been verified by an experienced corrosion engineer in over five years, lower confidence exists in the RBI program itself. Therefore, it cannot be confirmed that the appropriate pieces of equipment are included in the inspection scope (either too many vessels, or worse, a high-risk vessel is not included). Feed slates, throughput (i.e., charge rate), heating/cooling duty, new installation, or removal of existing equipment, operating philosophies, etc. all change over time, which may have a direct impact on the applicable damage mechanisms.
If a specific piece of equipment is on the upcoming TA inspection scope despite the RBI program not indicating an inspection is required, then this should be interrogated further. There may be many reasons that this is the case (e.g., known “problem” vessel, verification of new material of construction performance, API 510 requirement, etc.), and if a reasonable justification for inspection is provided, then inspection should still be performed. However, this may also be an indication that the RBI program is not accurately representative of the component (e.g., an un-conservative damage rate). Again, the goal of this review is to verify that the correct pieces of equipment are included in the inspection scope, while unnecessary pieces of equipment are excluded, without compromising safety or reliability.
TA Preparation: Inspection Planning
After the candidate assets for TA inspection are verified, the next step is to ensure that the inspections can be performed as efficiently as possible. Any “dead time” or lag in inspection can cost the facility a significant amount of money. Initially, the facility should confirm that certified inspectors are available to inspect equipment. Sourcing the inspectors should be completed well ahead of the actual TA date. Additionally, the required non-destructive examination (NDE) surface preparation should be communicated clearly to avoid delays. Note that extent of required surface preparation will likely be strongly dependent on the inspection techniques that will be used. This can be achieved by developing clear instructions, instituting hold points, and providing acceptance criteria related to the surface preparation. Re-cleaning a vessel because the surface was not originally prepared properly can be a costly delay. A process should also be established to facilitate the delivery of inspection results so that run, repair, replace decisions may be executed quickly following completion (e.g., results should be available in a matter of minutes after inspection is complete). This may be achieved by “digitizing” the inspection data as much as possible with possible entry into an Integrated Database Management System (IDMS). Decision-making should never be reliant on delivery of a physical inspection report.
Of course, the detailed inspection plan for each component should be evaluated and developed well ahead of the actual inspection date. A facility should not simply communicate “open, clean, and inspect.” This inspection plan shall include the locations in the vessel that will be inspected (e.g., top head-to-shell weld, longitudinal welds 1 and 2, top nozzle-to-head weld, etc.) along with the inspection techniques that will be performed by the already sourced qualified inspectors. It must also be determined if the inspection is intrusive or non-intrusive. If intrusive, additional requirements may be necessary for confined space entry and the appropriate permits should be in place prior to the TA.
When developing a detailed inspection plan, an experienced NDE practitioner should work directly with an experienced corrosion engineer (internal or external resources). This combination will ensure that the inspection plan is properly prioritized (i.e., inspecting the highest-risk locations), preventing “unnecessary” inspection that can cost precious time. If the same level of quality can be achieved with a non-intrusive inspection, then many steps can be eliminated (relative to intrusive), which can be a significant cost saver. The ability to prioritize an inspection requires a thorough understanding of the component and applicable damage mechanisms, which can be achieved through the recently validated RBI program and the assistance of an experienced corrosion engineer.
For example, the primary damage mechanism of a pressure swing adsorber (PSA) vessel is mechanical fatigue (often surface-breaking crack-like flaws) due to the cyclical nature of operation. These vessels are also filled with a desiccant material that is costly to remove and replace, which would likely be required for an intrusive inspection. Common areas of fatigue damage in PSAs include the longitudinal weld seam at the inner diameter (especially if peaking or weld misalignment is present), top head-to-nozzle weld at the outer diameter where stresses are the highest, and welded internal attachments. The top head-to-nozzle weld is also exposed to the highest concentration of H2, which is understood to influence fatigue damage. Consequently, the inner diameter of the longitudinal weld seam (location of expected damage) can be interrogated through external ultrasonic techniques (e.g., Phased Array or Time-of-Flight Diffraction) and the outer diameter of the top head-to-nozzle weld can be examined with magnetic particle inspection and follow-up Phased Array if indications are identified.
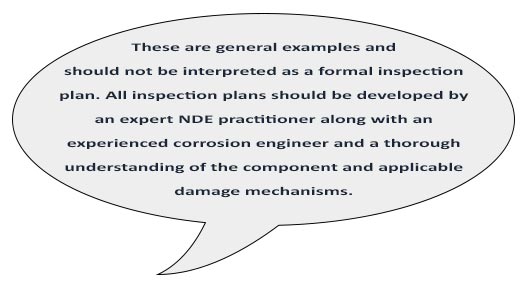
However, note that if a nozzle repad is present, external inspection may not be feasible. In general, given that a full PSA unit may contain as many as 8 or 12 PSA vessels, the facility must also consider how to prioritize each vessel. Since the multiple PSA vessels are in similar service (generally the same operating pressure cycles and temperature), some owners may “rotate” which specific vessels are rigorously inspected each TA and are, therefore, afforded the ability to potentially assume the inspection results are representative of the remaining vessels (this would require confirmation from an experienced corrosion engineer). Overall, this inspection plan addresses the primary damage mechanism and is potentially completed non-intrusively, saving time and consequently money. As with any damage mechanism, when damage is identified, the facility should consider expanding the inspection scope (relative to the originally planned inspection scope) to confirm that the “worst-case” location is discovered.
For a vessel in wet H2S service (e.g., Amine Contactor), the wet H2S inspection may be focused on certain wetted locations in the component based on industry experience (i.e., feed zones often contain the most severe damage). Since this damage is generally expected to be sub-surface with possible inner-diameter surface-breaking crack-like flaws, external UT techniques are likely capable of identifying the damage. Again, the primary damage mechanism is addressed sufficiently, a non-intrusive inspection can be performed, and overall time is saved. Note that an additional damage mechanism may be more limiting (e.g., Amine corrosion) and that this should be considered as well.
TA Preparation: Streamlining
There are many complementary efforts to the TA that can and should be completed prior to the planned shutdown. The intent of these efforts is to streamline maintenance and inspection actions during the actual TA. First, based on the inspection plan and operating temperature of a specific asset, online inspection may be able to be completed prior to shutdown (i.e., if operating temperature does not inhibit successful operation of the NDE transducer). If so, this can eliminate a portion of the work scope required to be completed while the facility is offline. All personnel safety risks should be understood and considered when performing online inspection. Additionally, this can serve to eliminate the “work density,” or amount of personnel in a given location. If multiple crews are performing tasks adjacent to the same location, then some work may be inhibited or delayed. This is another item that should be considered during the TA planning stage.
Proactive fitness-for-service (FFS) activities should also be considered. Minimum pressurization temperature (MPT) envelopes should be in place to guide de-pressurization/shutdown procedures prior to the TA for critical components. These MPT envelopes should also consider future start-up of the vessel in the event that crack-like flaws may be identified during the discovery phase (if damage is anticipated to be present), especially for high brittle fracture risk components (e.g., heavy wall, 1960s-1980s vintage, low-alloy equipment in hydrogen service). The MPT envelopes can be complemented by crack-like flaw assessments/crack growth calculations to establish go/no-go criteria based on inspection results. Subsequently, run, repair, replace decisions during the TA can quickly be determined. For vessels in wet H2S service, proactive local thin area (LTA) FFS assessments can be completed to calculate an acceptable grind-out allowance if wet H2S damage is identified (e.g., cracking). Minimum thickness (Tmin) calculations can be provided in an easy-to-use table for vessels in thinning service. Therefore, a quick decision can be made based on the amount of wall loss identified.
Proactive FFS efforts will afford a facility the ability to make quick decisions and will more than offset the up-front cost. Note that “per hour” costs during a TA can be extremely high due to lost production. If an RBI program is in place, downtime costs will likely be readily available (in the consequence of failure “section”) to allow for a quick cost-benefit analysis of proactive FFS versus the extended downtime required to make a run, repair, replace decision “on the fly” during the TA. The facility should also ensure that resources are available during the TA for an “engineering triage” when unanticipated damage is identified. This group (the Problem-Solving Team) generally consists of a combination of experienced FFS and corrosion engineers, and other specialists. In general, it is cheaper to “reserve” these resources ahead of time as opposed to attempting to source emergency assistance the day the damage is identified.
Some facilities have ordered materials and reserved a portion of a fabrication shop ahead of time in case an immediate replacement is required. This allows the facility to have a shell can or head of a vessel fabricated relatively quickly as opposed to trying to identify a fabricator in real time. It is also generally good practice to ensure welding consumables (especially for high, or “exotic,” alloys) are purchased and available ahead of time in the event that an emergency weld repair is required. An experienced, qualified welder should also be sourced ahead of time to perform the repair.
Weld repairs may often become “problem” locations for a vessel, eventually leading to additional damage with continued operation. This is especially true for originally post-weld heat treated (PWHT’d) vessels. Although some weld procedures allow for a high pre-heat and temper bead application in lieu of PWHT, a high weld residual stress profile will still exist at the weld repair location. This can propagate stress-driven damage mechanisms and would also likely require an update to the MPT envelopes to account for the non-PWHT designation, likely resulting in a longer start-up. Furthermore, local PWHT performed in the field is not without its own challenges (e.g., thermal distortion, material strength at temperature, uniform temperature profile, etc.). Any local PWHT plan should be developed by an advanced mechanical engineer to properly optimize the soak band. Ultimately, the pros and cons of advanced FFS (e.g., Level 3 FFS) combined with the required monitoring and inspection required for future operation, versus the challenges and risks of a weld repair, should be carefully considered before determining a path forward for the component.
Lessons Learned
Finally, after the TA is completed successfully due to excellent planning and proactive activities, the TA execution should be reviewed for lessons learned and potential improvements for future TAs. “Choke points” or considerable delays that occurred should be reviewed to understand why they occurred and determine how these can be prevented in future TAs. The applicable damage mechanisms listed for each vessel in the RBI program should be reviewed based on the recent inspection results. The facility should confirm that the correct damage types (e.g., localized thinning, general thinning, environmental cracking, etc.) and damage rates are currently represented in the RBI program. If unanticipated damage was identified, the asset should be updated accordingly in the RBI program. Post-TA review is critical as it is estimated that approximately 80% of the scope for the next TA can be identified after a recent TA.
For more information, please fill in the form below, or request access to the webinar on turnaround planning.