Based upon a presentation from the API RBI Software User Group Meeting, September 2021
Risk-based inspection (RBI) is an important inspection planning methodology in the refining, petrochemical, and chemical industries as it improves equipment reliability, reduces risk, and optimizes inspection plans by accounting for both the probability of failure (POF) and the consequence of failure (COF). Oftentimes, RBI is applied during or after commissioning when inspection intervals need to be established.
Advantages
Beyond the traditional application of RBI, it is important to consider starting an RBI program during the design phase when you are analyzing equipment life-cycle costs. At the design stage, companies can mitigate expected areas of concern by considering different materials of construction, coating, insulation, and reducing inventory groups for high-COF equipment. In addition, by applying RBI methodology at this stage, you can also evaluate the net present cost of an inspection due to anticipated damage mechanisms.
Additional benefits of embarking on an RBI program during the design stage:
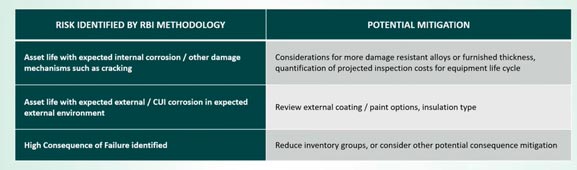
API 580 Risk-Based Inspection notes that conducting a risk assessment on new equipment while in the design stage can yield important information on potential damage mechanisms and allow risks to be minimized during design. The European standard, EN 16991 Risk-based Inspection Framework, notes that applying risk assessment in the design phase for analysis and determination of inspection strategies is a valuable application.
Implementing RBI at the Design Stage
RBI at the design stage requires a conservative risk approach based on the RBI team’s expertise and experience because there is limited data available, such as inspection histories. At this stage, implementing RBI undoubtedly requires assumptions about the assets being evaluated. Consequently, it is crucial the personnel making critical RBI decisions are properly qualified and prepared to make conservative and consistent assumptions for the RBI implementation.
Identifying potential damage mechanisms for all equipment and modes of operation is crucial in any RBI assessment. Oftentimes, many new plants experience significant damage that was not considered during the design stage. By considering all aspects of operations during the design stage RBI assessment, there are fewer opportunities for unanticipated damage or failures to occur. Experienced personnel are more likely to have experienced cases of upsets and be able to provide suggestions or considerations in the design stage.
Approach
In 2017, E2G completed an RBI assessment on an amine unit. The client asked our RBI consultants to review the previous inspection strategy, study how the strategy maintained risk, and compare the strategy to future risk, based on RBI. As a final step, our team reviewed the option of implementing RBI during the design stage rather than implementing an API 510 Pressure Vessel Inspection Code and API 570 Piping Inspector plan. Our team used API RBI to calculate the direct impact on risk by executing the proactive RBI assessment instead of the traditional inspection plan. In Figure 1, the chart compares inspections using the API 510/570 and RBI methodologies.
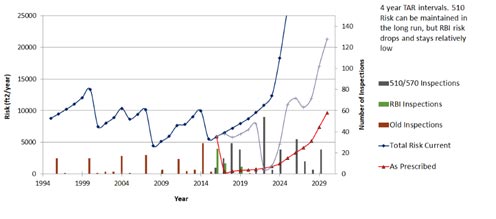
The client’s inspection histories dated back to 1994, and turnaround occurred every four years, as indicated by the red bars. In 2016, the client started using an RBI-based inspection planning methodology (green bars), and the prescribed risk is represented by the red line. When the RBI assessment was performed, several inspections were due right away; however, the number of inspections taper off over time.
The inspection intervals based on API 510/570 are represented by the grey bars, and the corresponding gray line represents risk. In 2020, the dip in the API 510/570 approach is potentially related to a credit from the damage mechanism review. The identified damage mechanisms, such as cracking, and the associated inspections would have been performed during the next turnaround. The increase in the risk for the API 510/570 approach is related to some piping that would have approached Tmin.
At the design stage for fixed equipment, Figure 2 demonstrates that even though the RBI risk remains relatively similar to the API 510 method, the RBI methodology requires substantially fewer inspections than API 510/570.

For fixed equipment, RBI recommended 7x fewer inspections with 7x greater effectiveness in reducing risk. These numbers represent a 97% reduction in scope for a mechanical integrity (MI) turnaround and 99% decrease in turnaround spending in 2026. In addition, piping required 6x fewer inspections and delivered a 7x greater effectiveness in reducing risk.
At E2G, we believe in using RBI principles at all stages of an asset’s life cycle, starting with the design stage. Companies will benefit from projecting costs to maintain and inspect equipment while staying focused on reliability. Using this innovative approach to RBI inspection planning may take more up-front effort to work; however, there is significant potential for long-term cost savings, reduced equipment failure, and increased operational reliability.
To learn more about applying RBI at the design stage, please fill in the form below: