This article was previously published in the Inspectioneering Journal, May/June 2022
API 579-1/ASME FFS-1 Fitness-For-Service (API 579) is the go-to standard for assessment of fitness-for-service (FFS) of fixed equipment in the petrochemical industry. Aboveground storage tanks (ASTs) designed to API 650 Welded Tanks for Oil Storage and API 620 Design and Construction of Large, Welded, Low-Pressure Storage Tanks are specifically included in the scope of API 579. The assessment procedures in API 579 may also be applied to pressure-containing equipment constructed to other recognized codes and standards, including international and internal corporate standards. E2G has substantial experience in the application of API 579 assessment techniques to ASTs. This article will examine the application of these API 579 FFS procedures to ASTs.
API 579 Applicability to ASTs
API 653 Tank Inspection, Repair, Alteration, and Reconstruction is the main in-service standard for ASTs. There are a few limited FFS methodologies provided in API 653, primarily for shell thinning and pitting, and shell and bottom settlement. In situations where API 653 has no FFS rules or when API 579 is specifically referenced, API 653 provides for the use of API 579.
API 579 is organized around damage mechanisms and the corresponding FFS methodology to evaluate each of the covered damage mechanisms. Parts 3 through 14 of API 579 provide FFS procedures for a dozen damage mechanisms. Of these damage mechanisms, all but a few apply to ASTs. In particular, brittle fracture and crack-like flaw assessments (Parts 3 and 9), metal loss assessments (Parts 4, 5, and 6), and distortion assessments (Part 8) are the most applicable sections of API 579 to ASTs. Other damage mechanisms covered in API 579 like hydrogen damage – blisters, hydrogen-induced corrosion (HIC), and stress-oriented hydrogen-induced corrosion (SOHIC) (Part 7); creep (Part 10); and dents and gouges in pipelines (Part 12) generally do not apply to ASTs. A few damage mechanisms covered in API 579 such as fire damage (Part 11), laminations (Part 13), and fatigue (Part 14) have limited applicability to ASTs. The following section will examine the half dozen sections of API 579 most applicable to ASTs.
AST Thinning Assessments (Parts 4, 5, and 6 of API 579)
API 653 includes requirements for the evaluation of thinning in tank shells and tank bottoms. A thickness averaging procedure is included in the shell evaluation section with a length of thickness averaging that is a function of tank diameter and minimum thickness reading. The required shell thickness is determined using a variation of the API 650 one-foot rule (for tanks not greater than 200 feet/61 meters in diameter). The required thickness is then compared to the average thickness determined over the length of thickness averaging, and the minimum thickness reading is compared to a structural minimum thickness. The API 653 method permits the use of higher allowable stresses than API 650, which is similar in concept to the main FFS criterion in API 579, remaining strength factor (RSF).
API 579 thinning methods are recognized as a permissible alternative in API 653 and, in many ways, are superior to those in API 653. API 579 Part 4 (General Metal Loss) and Part 5 (Local Metal Loss) also use a thickness averaging procedure to determine an average that is compared to code required minimum thicknesses or determine an RSF that is compared to an allowable RSF. The critical thickness profile (CTP) averaging procedure in API 579 is considered superior to the ones given in the inspection standards such as API 653. The length for thickness average in API 579 is a function of the remaining thickness ratio and the API 579 RSF. As a result, the API 579 method prevents a local depression in thickness measurements that may result in a failure from being smoothed out. The relationship to RSF allows the procedure to account for differences in design margins in various codes of construction. The CTP averaging procedures in Parts 4 and 5 are also consistent and allow the same data to be used in in Part 4 and Part 5 assessments.
Level 1 and Level 2 thinning assessments in API 579 have a few limitations on their use, the main one involving proximity to structural discontinuities. In terms of ASTs, these limitations make evaluation of thinning near the bottom or near the roof problematic using Level 1 or Level 2 procedures. The main concern in these regions of discontinuity is the existence of bending stresses exceeding the primary hoop stress seen in the shell away from the discontinuity. E2G has experience in these situations to determine the additional analyses or considerations required to evaluate the thinning in these regions using either modified Level 1 or Level 2 calculations that account for the additional bending stresses, or advanced Level 3 stress analyses (Figure 1).
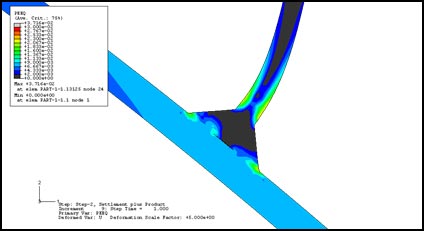
The third type of shell thinning addressed in both API 653 and API 579 is pitting. The only requirement for pitting in API 653 shell evaluations is that widely scattered pitting can be ignored if the length of pitting over any 8.0-inch (20 cm) vertical line does not exceed 2.0 inches (5 cm) and the minimum remaining thickness in the pitted area is at least 50% of the required minimum shell thickness. Beyond that, API 579 procedures would be required. In API 579, pitting (Part 6) is evaluated by one of several methods. Level 1 API 579 pitting assessments use screening figures to screen widely scattered pitting by comparing actual pitting densities (and the depth of the deepest pit) to one of eight control figures with varying pit densities. An RSF is determined from this information and compared to an allowable RSF. The Level 2 pitting method uses a significant amount of pit couple data to compute an RSF for comparison with an allowable RSF. Other pitting evaluations in API 579 use some of the same techniques for local metal loss that are found in Part 5.
API 653 also has minimum thickness requirements for a tank bottom. The requirements particularly of concern from a stress standpoint are the minimum thickness in the critical zone (near the shell) and in the minimum annular ring thickness (where an annular ring is used). In cases where the minimum values required by API 653 are not met, more advanced FFS techniques in API 579 can be considered.
AST Brittle Fracture and Crack-Like Flaw Assessments
API 653 has a procedure for evaluating an AST’s susceptibility to brittle fracture. The need for such an assessment might occur if the tank has experienced some type of damage or change in service, or information on the susceptibility of an AST to brittle fracture is undocumented. Brittle fracture assessments are also a key component of a hydrostatic test exemption evaluation. Much of the procedure in API 653 is a screening approach to brittle fracture susceptibility based on the code of construction, maximum thickness, minimum ambient temperature, product level-temperature history, and primary stress levels. In cases where the API 653 screening criteria fail, a rigorous brittle fracture assessment can be done. API 579 Part 3 and Part 9 form the basis for a more rigorous assessment. An API 579 Part 3 Level 3 brittle fracture assessment uses fracture mechanics concepts in Part 9 to evaluate a tank’s susceptibility to brittle fracture. E2G has developed a rigorous protocol for these types of assessments and has performed hundreds, either as part of the evaluation for a hydrostatic test exemption or to document brittle fracture susceptibility in an undocumented tank.
API 579 Part 9 fracture mechanics procedures can also be used to evaluate crack-like flaws found in tanks. While API 653 requires the evaluation of flaws such as cracks and laminations, it does not have specific requirements for assessment of the flaws themselves. In this case, API 579 would be the applicable standard. The Level 1 procedures in API 579 Part 9 use screening curves to evaluate crack-like flaws. Level 2 procedures take applied and residual stresses, material properties such as toughness, and flaw dimensions to calculate an assessment point on a failure assessment diagram (FAD). If that assessment point is within the acceptable region on the FAD, the component with the flaw is fit. The determination of weld residual stress (WRS) can be particularly important. API 579 Annex 9D provides residual stress relationships for typical weld geometries. In the case of the bottom corner joint in an AST, E2G has supplemented the WRS relationships found in Annex 9D with WRS modeling.
AST Distortion Assessments and Settlement Evaluation
Shell distortions including out-of-roundness, buckled areas, flat spots, dents, weld peaking, and weld banding are another damage mechanism where API 653 requires the evaluation of such damage but does not have specific requirements for assessment of distortion itself (with the exception of some types of shell settlement). ASTs are particularly prone to distortion given their general flexibility. Typically, shell distortions are caused by settlement, extreme environmental loads (wind or seismic), pressure excursions, and mechanical loads (dents). Part 8 of API 579 has procedures for the evaluation of distortion. Part 8 Level 1 screening is based on evaluating distortions using code of construction tolerances on such things as out-of-roundness. Seldom does a Level 1 evaluation provide satisfactory FFS results in an AST assessment. There are Level 2 assessment procedures for a subset of the types of distortion previously listed, particularly weld distortions such as peaking and banding. These procedures can be useful in some AST assessments. With most arbitrary AST distortions, Level 3 techniques are required. Part 8 Level 3 assessments are done using numerical analysis techniques found in Annex 2D of API 579. Often, shell distortions determined from 3D laser scanning (3DLS) are mapped onto finite element analysis (FEA) models and one or more of the various stress analysis techniques in Annex 2D are utilized. As distortions significantly affect buckling susceptibility, compressive loads and buckling strength in the distorted condition can also be assessed using Annex 2D procedures. E2G has developed rigorous protocols and performed numerous AST distortion assessments. Figure 2 illustrates the FEA modeling (Level 3 analysis) of one of these assessments.
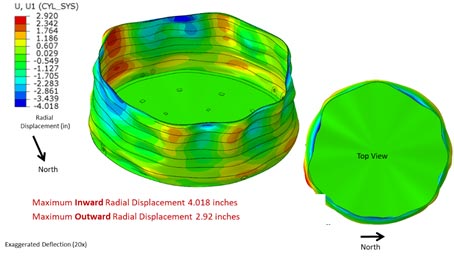
An AST assessment area where E2G has particularly specialized is settlement evaluation. E2G subject matter experts (SMEs) developed several of the settlement evaluation procedures found in Annex B of API 653. The current edge settlement procedure and one of the two shell differential settlement procedures were developed largely based on parametric FEA modeling of ASTs done by E2G using a strain limit criterion. In cases where the Annex B settlement limits are exceeded, more rigorous analyses are permitted by API 653. Stress analyses in accordance with Annex 2D of API 579 would be the methodology recommended in such cases. Including the parametric studies performed to develop API 653 Annex B procedures, E2G has performed hundreds of settlement evaluations, some including other coincident damage like bottom shell or critical zone thinning (Figure 1).
Upcoming Storage Tank Training Opportunities
The proper application of the procedures in API 579 to ASTs, or any fixed equipment, requires knowledge of the characterization of the damage, the data needed, and the assessment techniques. E2G has experienced tank SMEs who also apply API 579 techniques in their day-to-day work. As part of a main company objective, we look to pass on our knowledge to industry. Two upcoming courses are aimed at inspectors and engineers involved with ASTs.
Joel Andreani will be presenting a half-day course on FFS of ASTs on August 8 at the 2022 API Inspection and Mechanical Integrity Summit. The course will provide an overview and comparison of the FFS and suitability-for-service (SFS) requirements for storage tanks found in API 653 and API 12R1 and an overview of the FFS techniques in API 579 applicable to ASTs. Additionally, other aspects of SFS assessment of ASTs will be discussed, such as the minimum calculations required for undocumented tanks, assessments of change in service, the evaluation of a safe operating envelope based on operating history, and the evaluation of other tanks systems and components as part of an SFS evaluation, such as foundations, pressure relief, and overfill protection systems. Registration is available through the API Summit website.
In addition, the Equity Technical Institute (ETI) Storage Tanks virtual training course will be held July 18-22, 2022, by three of E2G’s tank SMEs. The course will focus on design of API 650 tanks and will also include sessions on the evaluation of existing tanks in accordance with API 653 and tank FFS in accordance with API 579. Register today.
If you have any questions regarding FFS of ASTs, please fill in the form below.