- Home
- Engineering
- Fitness-for-Service (FFS)
- Brittle Fracture
BRITTLE FRACTURE
Is there a Brittle Fracture Failure in Your Future?
Many pressure vessels, piping, and storage tanks in operation today were designed and installed before the original brittle fracture screening rules were applied. Depending on operating, environmental, or upset conditions, these components may have an increased risk for brittle fracture.
It is important to know if your equipment is susceptible to brittle fracture and take steps to prevent a catastrophic failure. At Equity, our team works with you to detect potential brittle fracture risk, set safe operating limits, and develop long-term risk management plans.
What is Brittle Fracture?
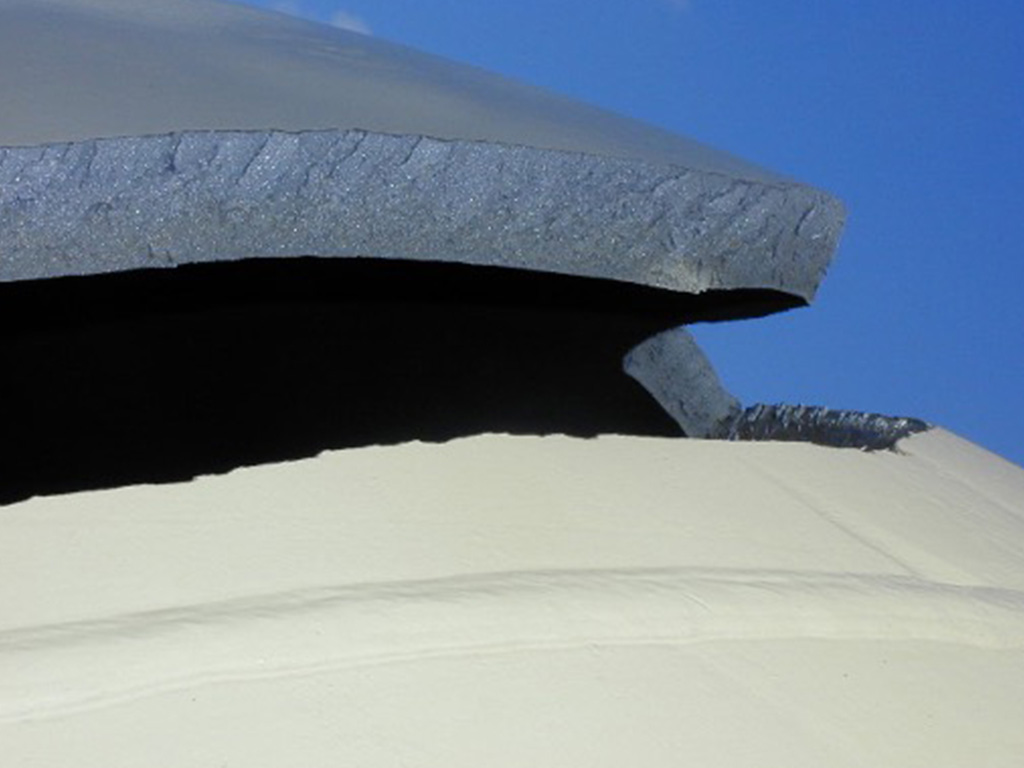
Brittle fracture is the sudden, rapid propagation of a crack-like flaw under stress where the material displays little or no evidence of ductility. Although rare, the consequences of brittle fracture are typically catastrophic, and preventing brittle fracture is essential when establishing fixed equipment lifecycle management strategies.
Brittle fracture is caused by:
- Magnitude of applied and residual stresses in the component
- Size of initiation flaw or defect
- Fracture toughness of the material
- Facility’s environmental conditions and ambient temperatures lower than MDMT of -20°F/-28°C
Operational Risk Areas
Within regular operations, pressure vessels, piping, and storage tanks may be at a higher risk for brittle fracture. Some scenarios that may increase the risk for brittle fracture are:
- Start-ups and shutdowns
- Weld repairs, particularly repairs without post-weld heat treatment (PWHT)
- Auto-refrigeration scenarios, such as:
- Depressurization with liquid petroleum gas (LPG) present
- Lowering pressure below liquid hydrocarbon boiling point
- Flashing across flow obstructions
- Operational upsets like loss of reboiler heat input on a distillation column
- Hydrostatic or pneumatic tests
When to Perform a Brittle Fracture Assessment
Brittle fracture assessments should be performed on higher-risk equipment and piping, even if it was built relatively recently, to prevent unexpected failures. Additional reasons or events that may trigger a brittle fracture assessment include:
- A change in process or operating conditions (e.g., re-purposed equipment, start-up/shutdown optimization, etc.)
- A process hazards review that indicates metal temperatures are lower than anticipated (e.g., auto-refrigeration events, operational upsets, pressure relief scenarios, etc.)
- Re-rating or fitness-for-service (FFS) for other damage
- Equipment repairs or alterations
Equity's Brittle Fracture Assessment Workflow
Equity works with you to identify the highest risk equipment and piping systems, set safe operating limits, and develop long-term risk management plans. We use industry-leading procedures and technology to conduct a comprehensive brittle fracture screening program for pressure vessels, piping, and storage tanks. Our services include:
- Minimum allowable temperature (MAT) assessments
- Screening of equipment for brittle fracture susceptibility (Levels 1 & 2)
- Detailed assessment using fracture mechanics (Level 3)
All brittle fracture assessments meet the 2021 edition of API 579/ASME FFS-1, OSHA 1910.119 process safety management, and RAGAGEP requirements.
Case Study: Large-Scale Brittle Fracture Screening
Issue: Due to low operating temperatures, a pipeline storage facility had identified several pressure vessels with a potential risk for brittle fracture.
Solution: We completed several Level 3 FFS assessments to determine the permissible safe operating limits for all equipment items. When necessary, an FEA was performed to quantify through-wall stress distributions at critical locations. In addition, fracture mechanics calculations were performed on the equipment to determine the minimumallowable temperature (MAT) limits, as a function of pressure, for each critical location.
Result: All equipment was qualified for continued operation at the current target operating and upset conditions. Our team provided guidance to assist the owner-operator in establishing an appropriate inspection plan for each pressure vessel.
Minimum Allowable Temperature
Minimum allowable temperature (MAT) describes the acceptable operating envelope, regardless of what damage mechanisms the equipment may be exposed to. The 2021 edition of API 579 includes guidance on how to adjust the material fracture toughness to address concerns for hydrogen and aging effects.
Recent Changes to API 579/ASME FFS-1
The brittle fracture screening procedures (Part 3) were rewritten to resolve discrepancies and deficiencies and include increased industry knowledge. The new standards also address how results obtained using a Level 2 fitness-for-service (FFS) assessment may be unconservative for certain situations, particularly for non-PWHT components.
The 2021 edition of API 579/ASME FFS-1 includes several changes to Part 3, Assessment of Existing Equipment for Brittle Fracture:
- Level 2 assessment for components not subject to uniform membrane stress loading; e.g., nozzle junctions in a pressure vessel or branch connections in the piping system
- Minimum allowable temperature (MAT) corrections for bolting and nut material specifications
- Shock chilling screening conditions require Level 3 evaluation
- Material fracture toughness guidance to address hydrogen and aging effects concerns
- Thickness limits for Level 1 impact test curves aligned with ASME VIII-1
- Inspection requirements for brittle fracture evaluations when metal loss exceeds original design tolerances
- Mill tolerance effects explicitly excluded from brittle fracture assessments
- Description that no PWHT credit can be afforded for repairs that included alternative weld procedures like high preheat or temper-bead techniques
- Clarification on explicitly neglecting pipe under-tolerance effects
- Fracture mechanics procedures for evaluation of crack-like flaws (under development)
SIMFLEX-IV, a cloud-based pipe stress analysis software, helps you proactively evaluate dynamic and static piping stresses to maintain integrity and code compliance across your entire piping system. Use the once-through workflow to create piping stress models, visualize geometry and support locations, analyze the effects of both dynamic and static stresses, and compare results to ASME piping code requirements.
Recommended Reading
- Brittle Fracture /
- Corrosion /
- Damage Mechanisms /
- Library /
- Brittle Fracture /
- Library /
- Mechanical & Structural Engineering /
- Piping /
- Webinars /
- Brittle Fracture /
- Industry Insights /
- Library /
- Mechanical & Structural Engineering /
- Welding /
- Brittle Fracture /
- Industry Insights /
- Library /
- Mechanical & Structural Engineering /
- Fitness-for-Service (FFS) /
- Library /
- Mechanical & Structural Engineering /
- Structural Engineering /
- Suitability-for-Service (SFS) /
- Fracture Mechanics /
- Industry Insights /
- Library /
- Mechanical & Structural Engineering /
Brittle Fracture Screening Expertise
Our mechanical and structural engineering team has completed thousands of brittle fracture screening assessments for pressure vessels, piping systems, and storage tanks. As pioneers of FFS technologies and lead investigators on many international standards, our team combines their extensive experience with state-of-the-art technology to help extend the lifecycle of your existing assets and create safe operating environments.
Our experts:
- Have 200+ years of combined experience
- Are the principal developer of API 579-1 / ASME FFS-1 and API 571
- Are the principal author of WRC 528 and WRC 562
- Are experienced with large-scale projects, including large-scale brittle fracture projects
- Serve as the committee leader for the API 579 Part 3 brittle fracture screening task group