What is Proactive FFS?
Proactive fitness-for-service (FFS) refers to quantitative engineering evaluations used to assess the mechanical integrity of damaged equipment before the damage has been fully categorized. Typically, FFS isn’t considered until after the vessel has been thoroughly inspected and the extent and severity of damage are identified. But there’s a better way: proactive FFS can save both time and inspection dollars.
Benefits and Drawbacks of Proactive FFS
With the traditional timeline of FFS assessments, the analysis may not begin until after the piece of equipment is already shut down. Thus, the urgency for the analysis findings leads to increased analysis cost (for expedited completion) and leaves owner-users with little time for repairs or replacements without costly turnaround window extensions. By performing the FFS assessment proactively, before the turnaround, the decision-making process following the inspection results can be expedited, saving analysis time and cost as well as on-site headache.
Additionally, providing proactive FFS results prior to the completion of inspection allows for more targeted inspection to take place. Different damaged areas may require varying degrees of inspection (e.g., spot UT checks vs. detailed grid scans) to achieve acceptable FFS results. Performing the FFS assessment early allows inspectors to differentiate between damaged regions that can be screened out (requiring minimal inspection) and critically damaged areas that would benefit greatly from more focused, intensive inspection.
Results of the proactive assessment can also be used to minimize repair scope or justify partial repairs as opposed to full restoration in areas that do not satisfy the FFS acceptance criteria.
A potential concern for performing FFS proactively is that the assumed damage used in the assessment may not closely resemble the actual damage found, but this risk can be minimized with good assumptions and iterations in assumed damage. Effective proactive FFS includes a wide array of assumed damage severity and locations to maximize applicability of the results and give site personnel maximum flexibility to justify continued operation.
In instances where a portion of the actual inspected damage is beyond the scope of the proactive FFS assessment, a follow-up assessment using the actual data can be performed quickly. Since the majority of the analysis work was completed prior to inspection and only a portion of the inspection results require follow-up, the cost and analysis time are considerably lower than a traditional FFS assessment.
Volumetric Damage Assessment Approaches
Multiple approaches to assessing volumetric damage are often employed in proactive FFS assessments to provide the owner-user a better high-level understanding of the general tolerance for metal loss as it relates to the requirements of API 579-1/ASME FFS-1 [1] (API 579) Part 4 Assessment of General Metal Loss and Part 5 Assessment of Local Metal Loss. Generally, reducing conservatism in the results also reduces applicability, but in many cases even the most conservative assumptions and assessment still provide acceptable results.
Due to the wide applicability of the results, including Level 1 and Level 2 general metal loss (GML) results provides a broadly applicable “catch-all” case to evaluate and screen out any minor metal loss, general or local, that may fall outside the applicability rules of other less conservative assessment procedures.
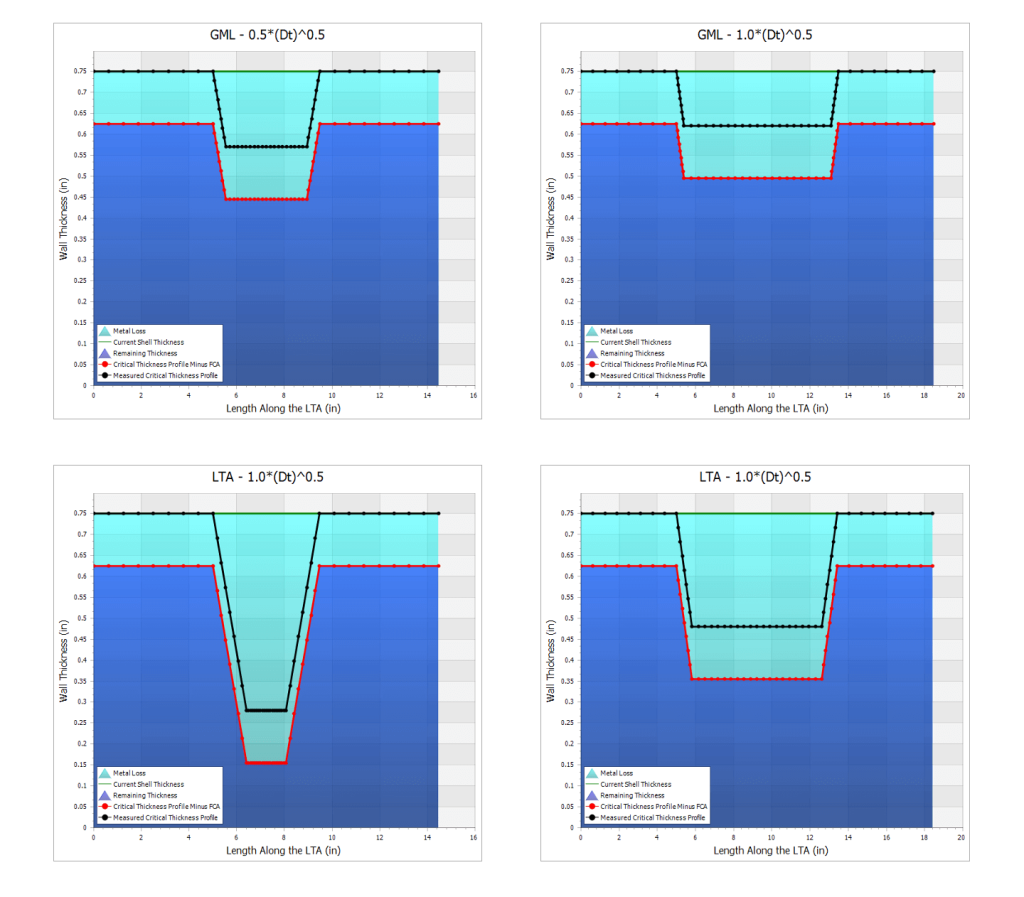
To provide results to evaluate/screen out more localized and severe damage, Level 1 and Level 2 local metal loss assessments can be used. The results of such assessments will depend on the assumed size and location of the local thin area (LTA) but are typically much less conservative than GML results. For example, minimum required thickness (treq) results will differ significantly between a 2-inch by 2-inch (5 cm x 5 cm) LTA in the top shell course of a tower and a 9-inch by 9-inch (22.86 cm x 22.86 cm) LTA in the same location, or a 9-inch by 9-inch (22.86 cm x 22.86 cm) LTA in the bottom shell course. At the owner-user’s discretion with input from the analyst, multiple LTA sizes and orientations may be assessed based on historical inspection findings for the equipment. Larger assumed LTAs may be beneficial to screen out widespread damage or multiple smaller regions that meet the LTA interaction criteria in API 579. Smaller assumed LTAs may be beneficial to screen out damage that is more severe but localized, such as flow-induced erosion or ground-out areas from crack-like flaw elimination.
While location and extent of the damage contribute significantly to acceptability, modifying the design loads applied to the equipment is a potential avenue to achieve FFS as well. A rerate of the equipment (e.g., reduce pressure, lower fill height, remove unneeded external pressure rating) may be an option to achieve acceptability. The viability of these options can be explored in proactive assessments.
The large number of possible scenarios to proactively assess demonstrates the importance of selecting the best iterations that will maximize the result’s effectiveness at screening the actual damage. By performing the analysis prior to critical times, more scenarios can be explored at a lower cost to the owner-user.
E2G Recommended Proactive FFS Scope
Proactively assessing the equipment with assumed damage that exactly matches the real damage would be ideal but isn’t practical if inspections can’t be performed online. In the absence of other data that might help predict the actual damage, the following recommendations will help maximize the effectiveness of the proactive results.
- For each shell section and head with unique thickness requirements:
- Perform Level 1 or Level 2 GML calculations to determine treq for uniform metal loss for shell sections (both near & away from welds) remote from any major structural discontinuities (such as nozzle or manway junctions, skirt support junctions, etc.). This one value can be used as a simple go/no-go for inspectors in the field; if the minimum measured thickness (tmm) adjusted for future corrosion allowance (FCA) is greater than this treq, no further measurements are required.
- If less conservative results are required:
- Perform Level 2 GML calculations for an assumed flaw size or range of sizes for each major component (shell or head with unique thickness requirements). A good starting point is to assume a rectangular flaw with sides of approximately 1.0√Dt in length. If more scenarios are desirable, perform the same calculations for flaws half as large and twice as large.
- If still less conservative results are required:
- Perform Level 2 LTA calculations for an assumed flaw size or range of sizes. Use the same sizing guidelines as suggested above for Level GML.
- Perform code treq calculations using guidance from the original design code and API 579 Annex 2C for nozzles and manways.
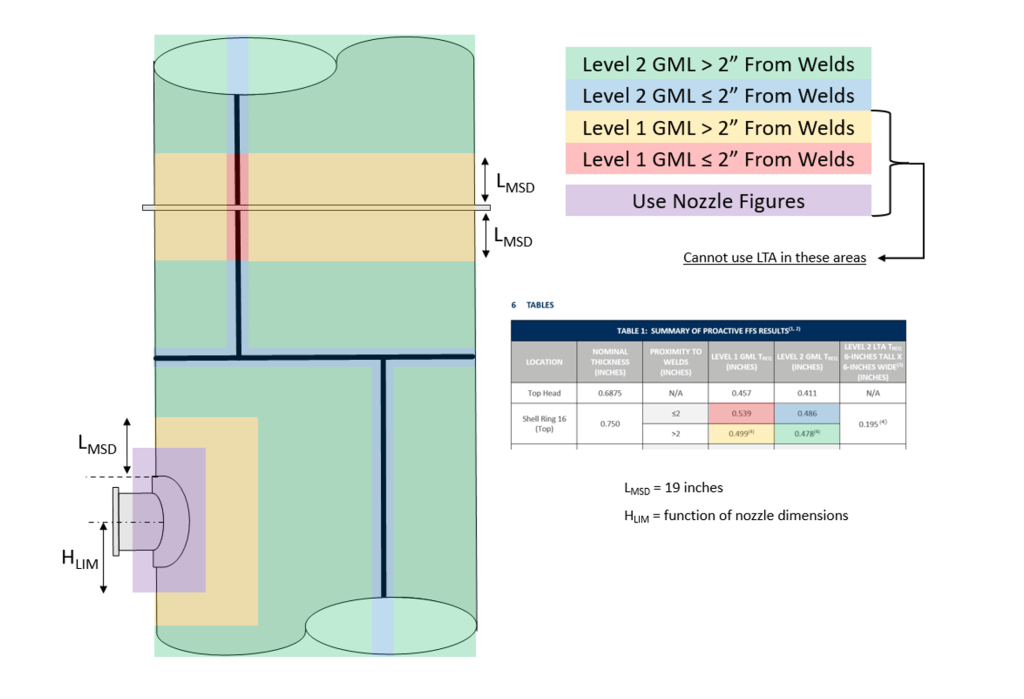
Using Proactive FFS Results in the Field
Field application of the proactive FFS results can follow the same pattern as the recommended scope. If the tmm, adjusted for FCA, is greater than the Level 1 GML thickness, no further inspection is required. Otherwise, compare the overall dimension of the region of metal loss and the tmm to the results of the Level 2 GML assessment for those dimensions. If that still doesn’t provide acceptable results, compare tmm to the Level 2 LTA results. If results still aren’t acceptable, it may be worthwhile laying out an inspection grid to collect more data for analysis outside the proactive scope. Once back in the office, generate critical thickness profiles from the grid data.
Additional Tips for Proactive FFS
- If the equipment has a joint efficiency less than 1.0, the joint efficiency is typically only applicable to the weld joints and the immediate vicinity. Any base metal locations can usually be assigned a joint efficiency of 1.0.
- Generally, FFS assessments for metal loss decrease in conservatism and increase in location restrictions in the following pattern:
- Level 1 GML (Part 4)
- Level 2 GML (Part 4)
- Level 1 LTA (Part 5)
- Level 2 LTA (Part 5)
- Note that critical thickness profile data can be used in all four of the assessments noted above, so if field screening indicates that grid data should be collected, there’s no need for additional data gathering because the same critical thickness profiles can be assessed using any of the Level 1 or Level 2 methods.
- Level 3 assessments are the least conservative and have no restrictions on locations for use.
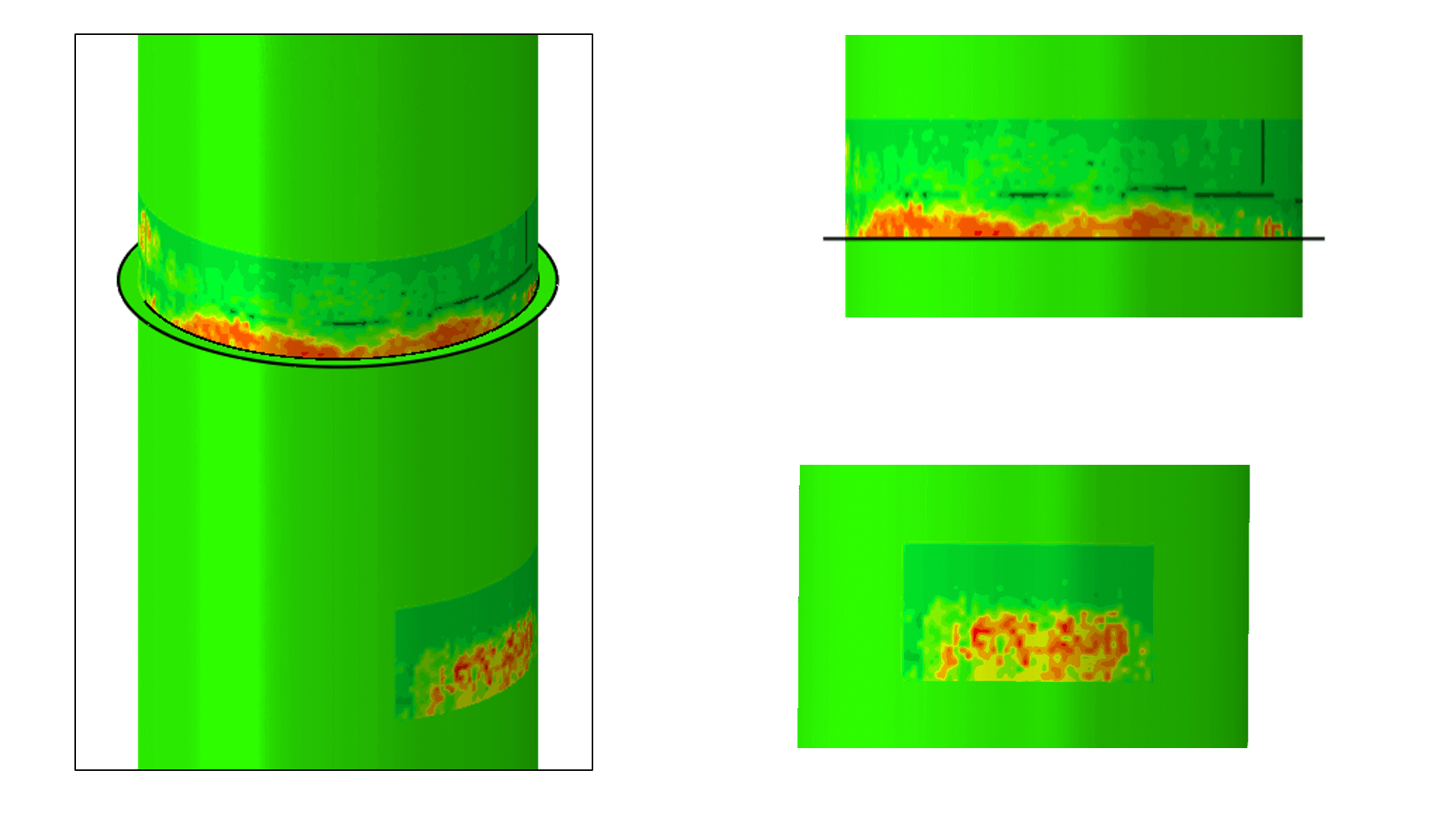
Conclusion
Performing proactive FFS for equipment that an owner-user suspects or knows will have some volumetric wall loss can save significant time and expense during a turnaround. Inspection scope can be minimized by having a set of well-defined ‘goal posts’ for acceptability, and even if the proactive results don’t indicate acceptability, the work used to generate them can be easily reused to perform analysis on the actual inspection data.
Reference
- API/ASME, 2021. API 579-1/ASME FFS-1 Fitness-For-Service. The American Petroleum Institute and The American Society of Mechanical Engineers, Washington, D.C./New York.