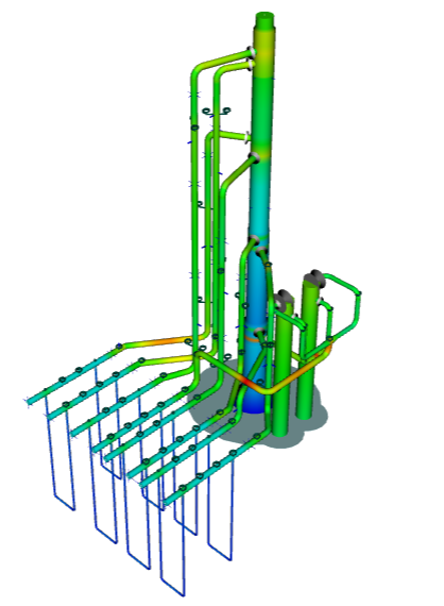
SIMFLEX-IV is the next generation of the SIMFLEX Pipe Stress Analysis program. To ensure the maintainability and extensibility of the program for years to come, E2G has rewritten the SIMFLEX program from the ground up. With the new implementation, SIMFLEX-IV is well poised to complement both SagePlusTM and the Equity Engineering Cloud (eec), both of which E2G has spent years developing and maintaining to meet current industry needs and ensure compliance with the newest regulations, codes, and standards.
As you may know, Liang-Chuan Peng, the original author of SIMFLEX, worked on these pipe stress programs for several decades. Peng literally wrote the book on Pipe Stress Engineering, and as such, SIMFLEX is a vast, sophisticated program. However, the SIMFLEX source code E2G acquired in 2017 was difficult to modify, adapt, and grow at the rate that our industry demands. Around 2 years ago, the Applied Research & Development Team at E2G began a complete rewrite of the source code from scratch. After this extended effort, we now have a new and improved version of the program that is more adaptable to our fast-changing industry.
To be sure, there is still work to be done to tackle the challenges in modern day pipe stress engineering and push SIMFLEX-IV to even greater heights. Today though, SIMFLEX-IV offers some new features, enables a tighter integration with existing workflows and tools, and will act as a springboard for new high-value additions.
Highlights of the Functionality of the SIMFLEX Program
Piping systems are designed to withstand a variety of external and internal stresses; however, any variation in mechanical or thermal loading, fluid flow, or weight may cause failure. With SIMFLEX-IV, a cloud-based pipe stress analysis software, you can proactively evaluate dynamic and static stresses to maintain integrity and code compliance across your entire piping system. Apply the once-through workflow to calculate code compliance analysis, spring hanger design, rotating equipment load compliance reports, anchor and support load combination tables, and nozzle stresses, with or without friction, all in one run.
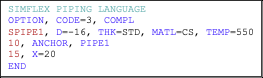
Standardized piping language. The SIMFLEX interface is text-based, using a standardized piping language as opposed to graphical user interface. This permits the analyst to directly use production or fabrication drawings in preparing input.
A smooth workflow to results. With SIMFLEX-IV, you can quickly model your piping system, allowing for rapid prototyping. The stepper-based workflow enables easy visualization of your geometry and support locations. The robust calculator allows you to analyze the effects of both dynamic and static stresses and compare results to ASME piping code requirements.
Advanced nonlinear analysis capabilities. Account for fully nonlinear restraints in the piping design process, including limit stops with lift-off, gapped restraints, and translational and rotational friction. The numerical implementation of SIMFLEX-IV is modern, allowing for a stable solution to be achieved even with multiple single-acting and nonlinear restraints. SIMFLEX-IV is a fast and easy way to integrate advanced nonlinear piping stress analysis into your daily workflow.
Dynamic analysis. Be prepared to address any dynamic load change. Proactively calculate the natural frequencies and modal shapes of the piping system; determine loads, displacements, and stresses; and evaluate code compliance.
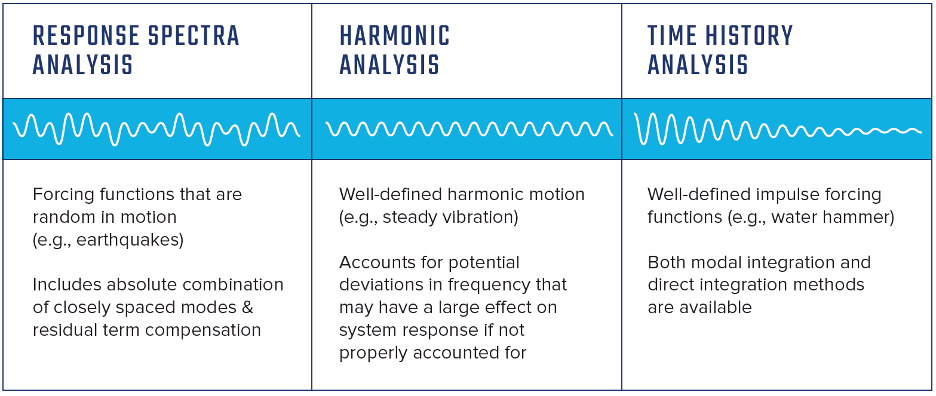
Modern visualization. Model piping systems and explore calculation results using SIMFLEX-IV’s advanced 2D and 3D visualization capabilities. The modern graphics make it easy to check your input piping system and view deformations and stress contours for all load cases analyzed.
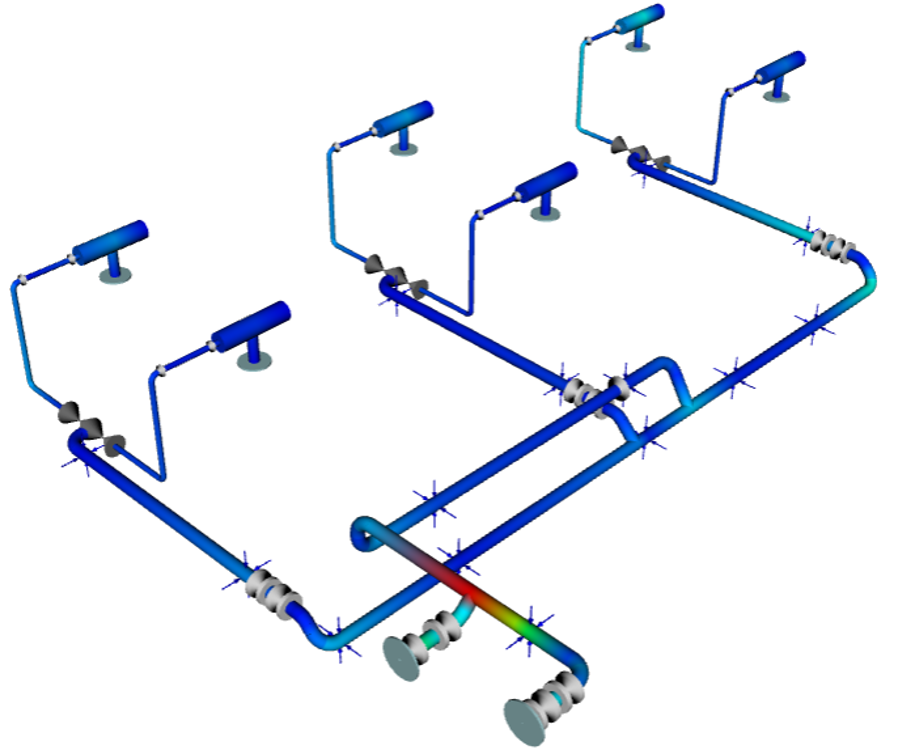
Improvements and New Features in SIMFLEX-IV
The goal of the SIMFLEX-IV rewrite was to capture the decades of experience baked into the SIMFLEX program while making the new version more amenable to changes and future extensions. Broadly speaking, the main improvements already available in SIMFLEX-IV are as follows.
Addition of new code calculations & standards. The new rules in ASME B31.J require different flexibility factors and stress intensity factors (SIFs) at various branch connections. These rules are implemented and automatically detected in SIMFLEX-IV. Other code calculations will also be available soon. For example, EN13480 and the hydrogen pipeline code B31.12 are currently being implemented in SIMFLEX-IV and will be available in an upcoming release.
Integrability into current tools. Due to some inherent limitations in the legacy SIMFLEX program, extending or amending it was near impossible. This made integrating the core application very difficult and required the building of many interfacial layers. The SIMFLEX-IV program has been redesigned with extensibility in mind. The program is written in a much more modern style, and extending the program to new solution types is vastly simpler.
Modern programming practices, high-performance libraries, and removal of input restrictions. SIMFLEX-IV is built on scientific computing libraries from E2G’s first Small Business Innovative Research (SBIR) grant from the Department of Energy. With these libraries, the program is capable of greater scalability, speed, and accuracy in many of the core numerical procedures in the finite element program.
Fixed bugs in the legacy SIMFLEX program. One of the main features of the SIMFLEX program has always been its robustness and ability to always deliver solid results. It is a notably battle-hardened program. However, like any complex computational engine, there are bugs that slip through cracks over the years. During the development of SIMFLEX-IV, bugs discovered in the legacy program were documented, thoroughly verified, and fixed.
For more information, please submit the form below: