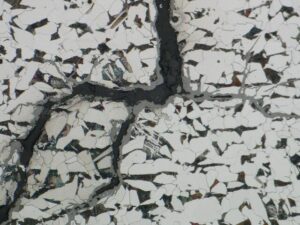
Boilers and Common Damage Mechanisms with Real-World Case Studies
Boilers are essential for industrial steam generation, but corrosion issues can disrupt operations, making prevention and mitigation critical. In this article, Nate and Luke explore common damage mechanisms, discuss effective prevention strategies, and share recent case studies demonstrating the value of expert analysis in maintaining reliability. Read the full article to learn how to keep your systems running smoothly.