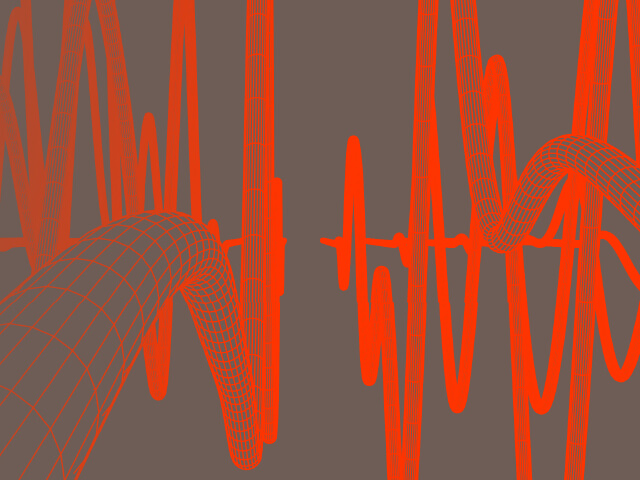
Addressing Piping Vibration in the Oil, Gas, and Petrochemical Industries: The Upcoming API 579 Part 15
With the recent API Fall Meeting, it is timely to revisit this November 2023 article on API 579 Part 15, Methodologies of Piping Vibration, featuring insights from one of the new standard’s co-authors, Mike Bifano. This article discusses the three-tiered evaluation system and explains how vibration fits into a mechanical integrity program. Read more and learn about the highly anticipated improvements to our industry standards.