INDUSTRY INSIGHTS ARCHIVE
- Home
- Industry Insights Newsletter
Filter:
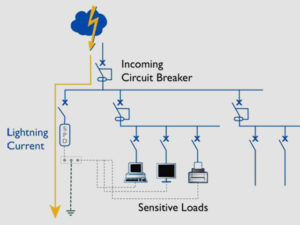
Practical Electrical Considerations in Process Plants
Electrical systems are often overlooked in process plants—that is, until something goes wrong. This article shares practical best practices to improve power reliability, reduce downtime, and strengthen the safety and resilience of your facility’s electrical infrastructure.
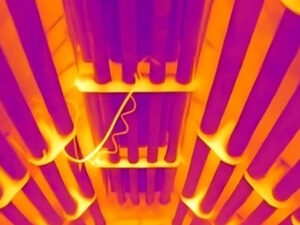
Practical Guidance for Plant Turnarounds
Typically, turnarounds pack months of work into a very short time period—what you do before, during, and after can make or break long-term reliability. In this article, Kraig and Neal provide practical guidance to help you better plan, execute, and close out TARs turnarounds with confidence.
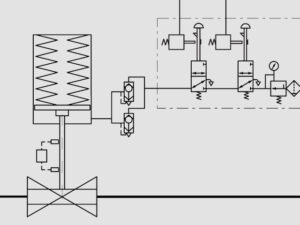
Applying High-Integrity Pressure Protection Systems (HIPPSs) in Petrochemical Plants: Reducing Overpressure Risk Through Instrumented Solutions
HIPPS are emerging as a key alternative to conventional overpressure protection in upstream and pipeline operations. In this article, the author explores how HIPPS improves safety, reduces emissions, and addresses the limitations of traditional pressure relief methods.
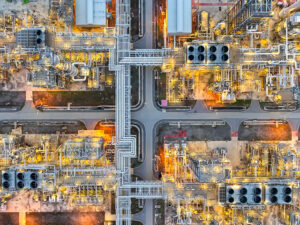
Equity Engineering Practices: Q&A with Joel Andreani
In an era of rapid digital transformation, it is often easy to overlook the foundational role that best practices play in safe and consistent decision-making. In this exclusive Q&A interview with Joel Andreani, Senior Vice President of Knowledge Management, you will learn more about the Equity Engineering Practices (EEPs), the value these documents bring to operating facilities, and how our team keeps this library of technical guidance current and relevant to industry needs.
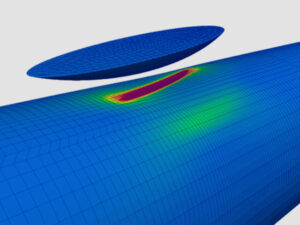
Reimagining Level 3 FFS: How Cloud Computing and Automation Are Transforming Asset Management
Cloud computing and automation are reshaping what’s possible in asset evaluation and management. In this article, the author provides a look inside the architecture of the new FEA Suite, shares real-world case studies, and explains how distributed computing helps overcome common barriers to Level 3 assessments. Get a glimpse into the future of faster, more reliable analysis.
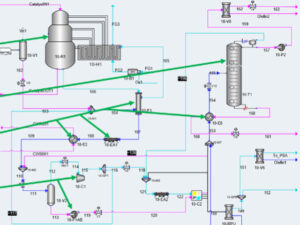
The Expert’s Guide to Process Simulation
Discover the essential principles of process simulation for chemical engineering. In this article, Victor provides a detailed discussion into how to design, troubleshoot, and optimize processes efficiently using modern simulation software. You will learn how to select thermodynamic models, set up accurate simulations, and implement optimization techniques for maximum performance.
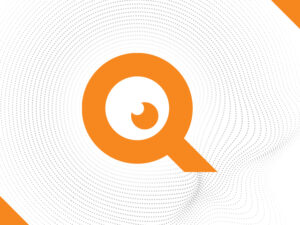
Embracing the AI Revolution: Unveiling Q – The Future of the EEPs
When implemented thoughtfully and carefully, artificial intelligence (AI) has the power to vastly revolutionize your proprietary corporate standards. In this article, you will learn about Q, new AI capabilities, purpose-built for Equity Engineering Practices (EEPs) subscribers. Using a closed-source AI engine, Q can enhance the full potential of your intellectual assets, paving the way for increased productivity and improved knowledge transfer.
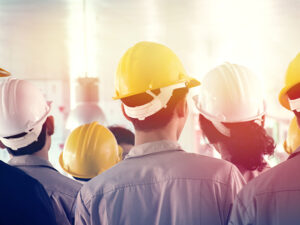
Educating the Next Generation – Training SMEs
Integrating cutting-edge solutions into proactive knowledge-sharing programs ensures the seamless transition of expertise from retiring subject matter experts (SMEs) to the next generation. Read about ETI’s mechanical integrity and lifecycle management training designed to increase knowledge transfer, while also helping engineers learn new technologies and achieve operational excellence.
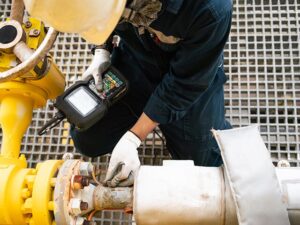
Instrumentation and Control Systems Reliability and Maintenance: Best Practices
Instrumentation and control systems are critical components to long-term plant safety and reliability. In this article, Rohan examines several maintenance and reliability best practices, including reliability-centered maintenance (RCM) principles, risk assessments, and advanced maintenance strategies. You will also learn how advancements in artificial intelligence (AI) and data analytics are shaping the future of industrial maintenance.
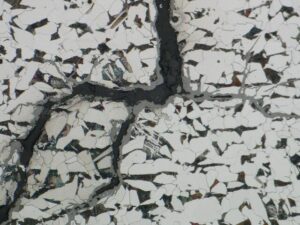
Boilers and Common Damage Mechanisms with Real-World Case Studies
Boilers are essential for industrial steam generation, but corrosion issues can disrupt operations, making prevention and mitigation critical. In this article, Nate and Luke explore common damage mechanisms, discuss effective prevention strategies, and share recent case studies demonstrating the value of expert analysis in maintaining reliability. Read the full article to learn how to keep your systems running smoothly.
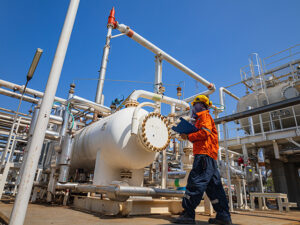
Vessel Overpressure Protection Using System Design – No Relief Valve? You’re Kidding, Right?
Even though PRDs are the industry standard for overpressure protection, there are cases when an instrumented system design approach can be a good alternative, if it meets ASME Section XIII, Part 13 requirements. Within this article, Phil Henry outlines key considerations, from assessing feasibility to ensuring compliance, and the key questions all owner-users should be asking.
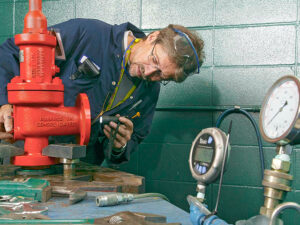
Ensuring Pressure Relief System Integrity Using a Comprehensive PRS Audit Approach
A well-structured PRS audit process helps verify system integrity, update records, and ensure overpressure protection remains effective. In this article, Phil Henry outlines the key elements of an effective auditing program, from planning and execution to reporting and continuous improvement.
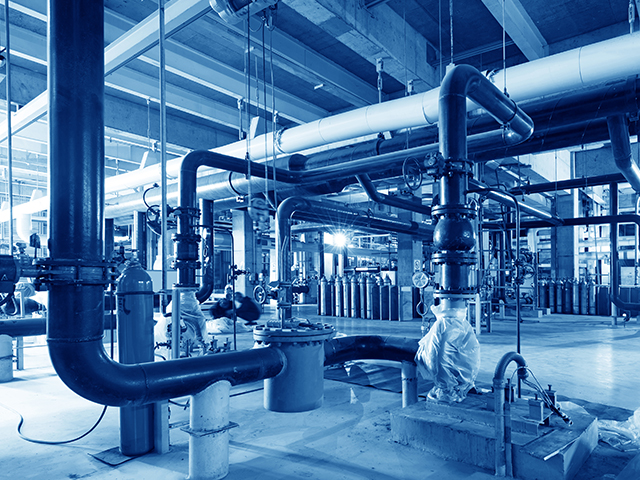
Analysis of Piping Surge Events
Surge events in piping systems can lead to severe displacements, loud noises, and operational challenges. Using a case study, this article highlights the factors behind surge events, including rapid changes in liquid velocity and pressure, and how forces generated during these transient events can impact piping systems. The authors discuss how a few targeted support modifications effectively resolved these issues without resorting to costly system overhauls or potentially problematic specialty equipment.
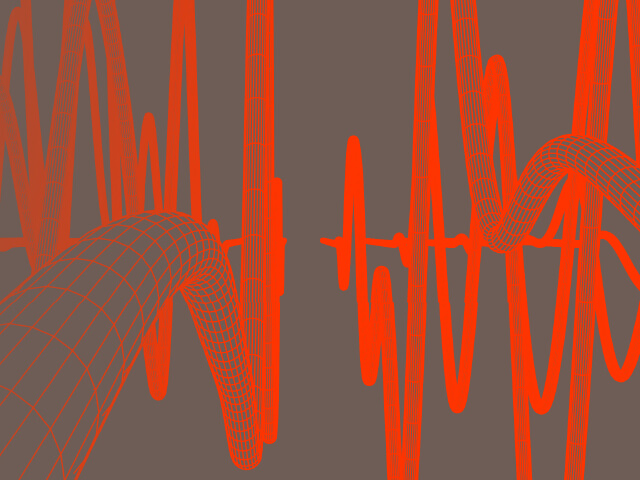
Addressing Piping Vibration in the Oil, Gas, and Petrochemical Industries: The Upcoming API 579 Part 15
With the recent API Fall Meeting, it is timely to revisit this November 2023 article on API 579 Part 15, Methodologies of Piping Vibration, featuring insights from one of the new standard’s co-authors, Mike Bifano. This article discusses the three-tiered evaluation system and explains how vibration fits into a mechanical integrity program. Read more and learn about the highly anticipated improvements to our industry standards.
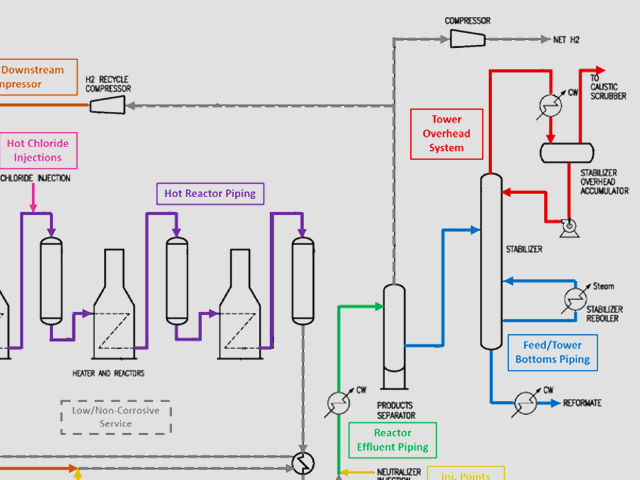
Damage Mechanisms Affecting Catalytic Reformer Units
This article offers a detailed look at catalytic reformer units, highlighting key components and operations like octane improvement and hydrogen production. The discussion on damage mechanisms, from high-temperature hydrogen attack to chloride stress corrosion cracking, provides valuable insights and lessons learned from industry experience which address common operational challenges and failures.
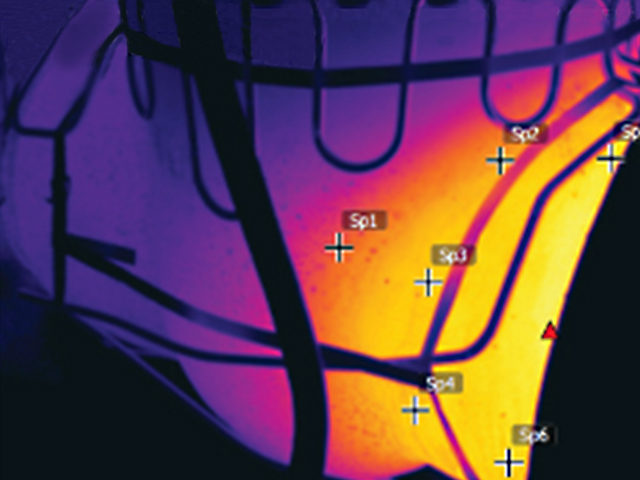
Reformer MOV Cracking FFS Case Study
This case study explores fatigue cracking in motor-operated valves (MOVs) used to cycle flow in and out of reformer unit reactors. Surface flaws were discovered during a recent turnaround which prompted further investigation. As only a few of the MOVs were opened and inspected, the owner-user was concerned about the extent and severity of cracks in additional valves. In this article, the authors share the details of the case study and how Equity’s recommendations helped the client make informed repair decisions.
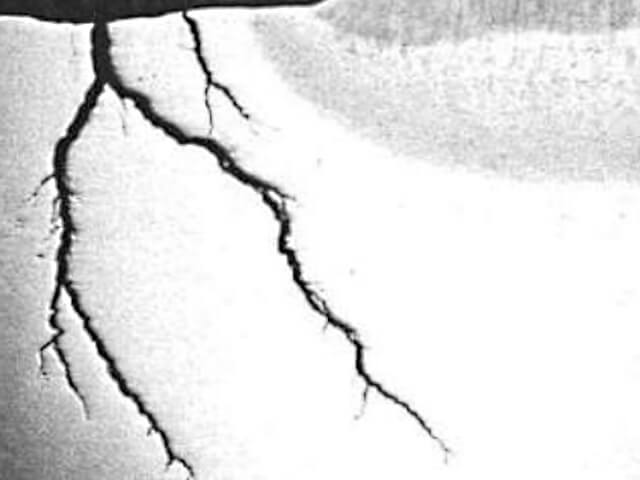
Damage Review and Risk Assessment of Midstream Amine Processing Units
For those who had the opportunity to watch last week’s webinar presented by Brian and Shane, this article expands on the benefits of risk-based inspection (RBI) for amine processing units and offers a multidisciplinary approach. It begins with an overview of the process and rich/lean amine loading, identifies key damage mechanisms and areas of concern, and proposes options for corrosion mitigation.
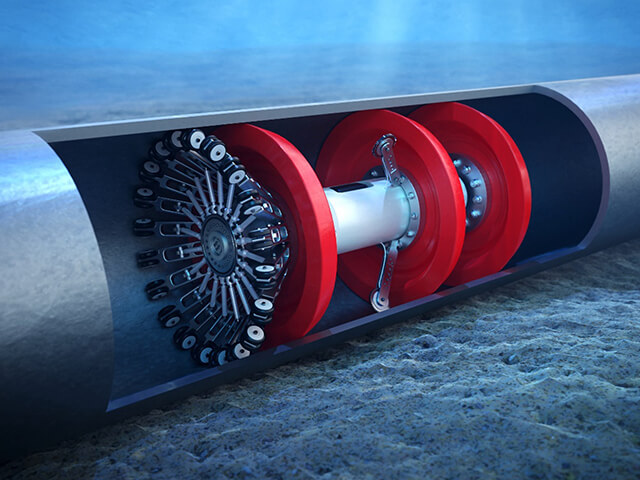
Are Dents Really a Problem?
There are several assessment procedures available for evaluating dents and determining whether a dent poses a viable threat to the integrity of a component. Read about common analysis methods for the critical failure mechanisms, potential failure mechanisms such as creep, complex dent configurations, and highlight the value of using a Level 3 finite element analysis (FEA) to determine whether the dent is truly a problem.

Pipeline Monitoring and Leak Detection: Essential Technologies and Practices
Due to length and complexity, midstream pipelines are prone to leaks. In this article, Rohan provides a detailed overview of the technologies and practices used in pipeline monitoring and leak detection. In addition, he discusses the importance of leak detection programs for the long-term operation of pipeline infrastructure.
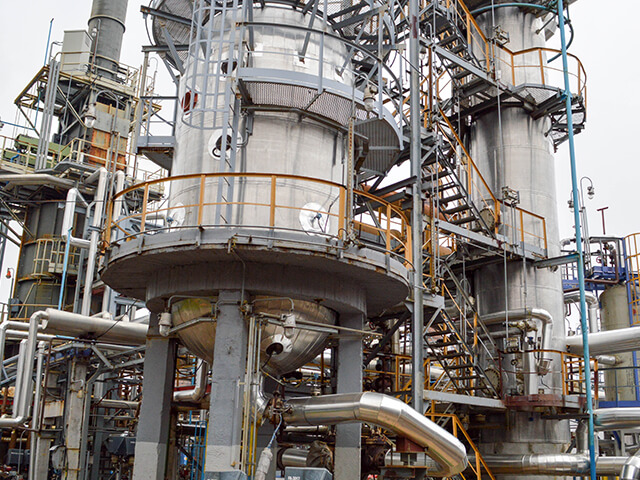
Effect of Sigma Phase on FCC internals
Sigma phase embrittlement is a concern for austenitic stainless-steel components in FCC units and other internal welds in FCC regenerators. Prolonged exposure to high temperatures can lead to sigma phase formation, reducing toughness and ductility and increasing the risk of creep cracking. In this article, the authors explore preventive measures to mitigate sigma phase formation and the importance of weldability testing to increase the reliability of FCC units.
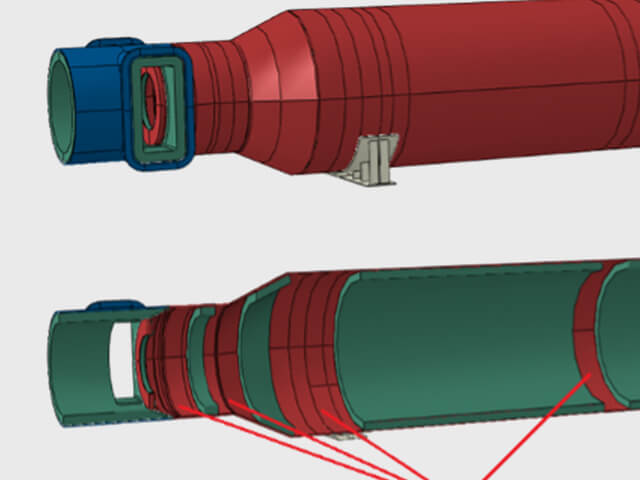
Managing Refractory Degradation and Hotspots in Cold-Walled Equipment
Refractory linings are used to protect pressure vessels and piping components from hot process conditions but can degrade over time, leading to hotspots, creep damage, and potential failure. In this article, the authors discuss the benefits of conducting periodic inspection programs to manage refractory degradation and share an example to highlight the importance of detecting permanent material damage caused by creep or creep-fatigue.
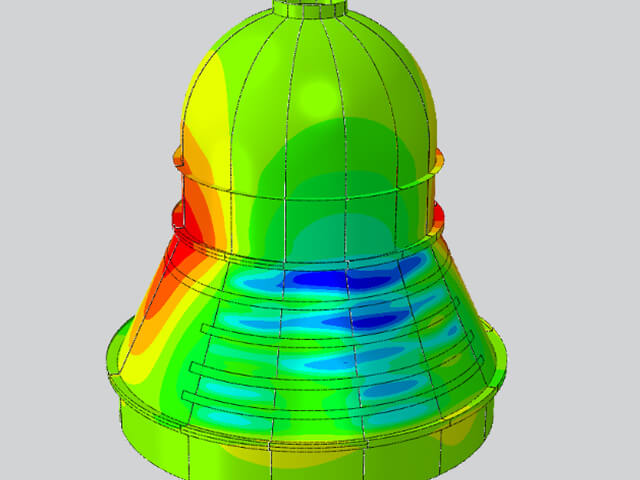
Advanced Analysis of Equipment Repairs and Alterations
Maintenance programs require a significant investment of time, energy, and money to keep facilities and equipment operating safely and reliably. Despite these efforts, there will always be a need for repairs, replacements, or alterations. In this article, the authors use a variety of case studies to discuss how advanced analysis techniques can support several post-construction activities. They offer insight into how to evaluate weld repair plans and post-weld heat treatments, validate rerate conditions, and ensure structural integrity.
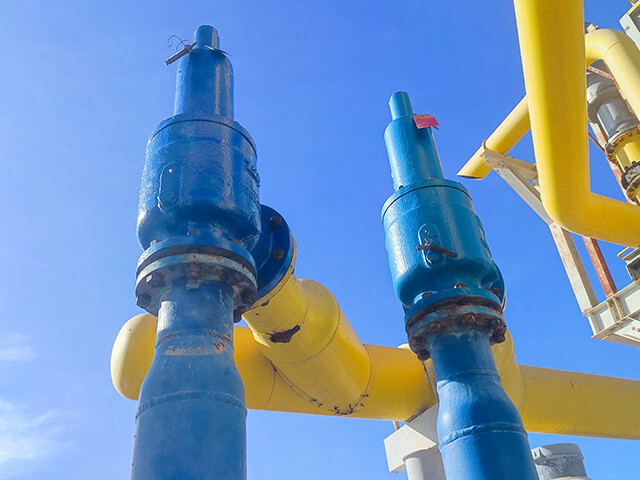
Are There Gaps in Your Pressure Relief Program?
Pressure relieving systems serve as the last line of defense against the dangers of overpressures in our facilities, but this protection can be jeopardized by poor maintenance and degradation. Active safeguarding of this protective system is crucial to preventing catastrophe. While the requirement for pressure relief is rooted in the ASME code, it is the US CFR 29 1010.119 [1] that requires the proper documentation of relief system design and design bases.
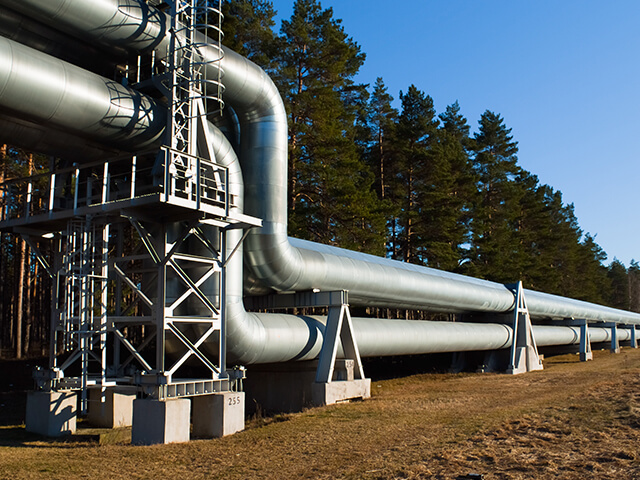
Reuse Practices, Midstream Engineering Practices, and Other Additions to The Equity Engineering Practices
Corporate standards or engineering best practices are help owner-users manage equipment and facilities by promoting safety, managing risk, improving reliability, capturing corporate memory, and transferring knowledge. In this article, Joel highlights two new collections that were recently added to the Equity Engineering Practices (EEPs) to support clients in the midstream and renewable energy industries, plus he provides a sneak peek into some of the innovative tools currently in development. The EEPs are the gold standard for all your engineering standards needs.
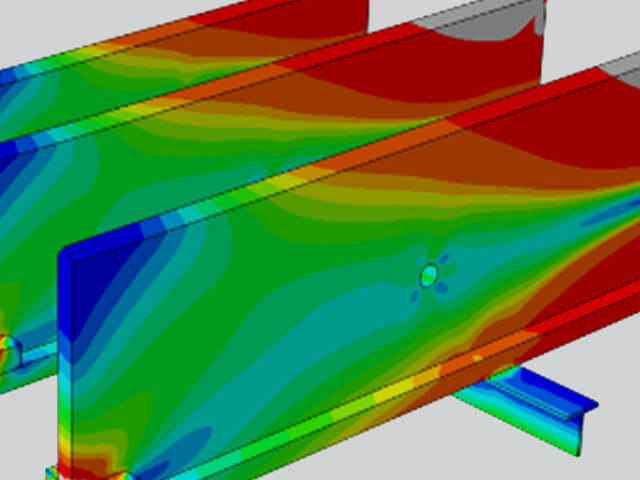
Understanding Operating Limits on Reactor Internals
Hydroprocessing equipment is an important component that helps increase production at refineries. However, during regular operations, the efficiency and run life of these reactors can be compromised by build up on the catalyst surface, leading to costly shutdowns or reduced production. In this article, Adam and Matt discuss how monitoring bed support differential pressure can maximize runtime. They use a recent case study to demonstrate how their analysis of the catalyst bed effectively delayed a shutdown at refinery.

Temperature Measurement Hydrocracking Reactors
As more refineries begin to process biofuels, it is important to establish a consistent and accurate temperature measurement program to ensure the hydrocrackers are capable co-processing the new feedstock safely and reliably. In this article, Rohan and Ahmed review the fundamentals of temperature measuring devices and discuss key maintenance and reliability techniques that you can apply to prevent unplanned shutdowns.
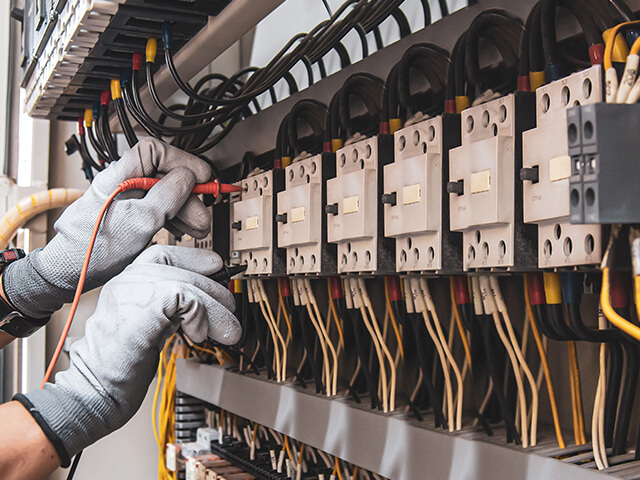
Enhancing Electrical Infrastructure: The Importance of Electrical Safety and Reliability Audits
In today’s rapidly evolving technological landscape, ensuring the safety and reliability of electrical systems is paramount. Electrical failures can lead
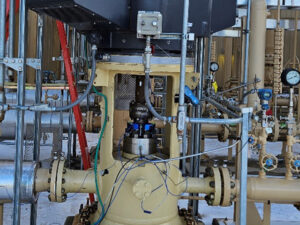
Case Study: Diagnosing the Root Cause for High Vibrations on a Vertical Pump
Determining the cause of a change in machinery condition can be a difficult task, and vibration analysis is a valuable

Advancements in Risk-Based Inspection Strategies for Ammonia Storage Tanks
Developing a repeatable, in-service inspection strategy for ammonia storage tanks is difficult; however, it will help improve operational reliability and minimize the probability of failure from several damage mechanisms, including ammonia stress corrosion cracking (SCC). In this article, the authors discuss Equity’s multi-disciplinary approach to navigate the challenges of these high-consequence ammonia storage tanks. Read how we integrate risk-based inspection (RBI), fitness-for-service (FFS), and materials and corrosion expertise to provide a comprehensive and practical inspection strategy.
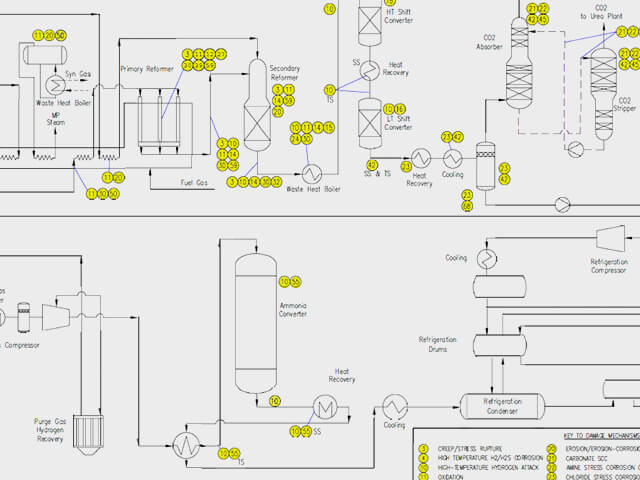
Materials & Corrosion Considerations for Ammonia, Urea, Nitric Acid, & UAN Units
Over the past 20 years, the fertilizer industry has experienced several metallurgical and operational advancements for process equipment. In this article, Raj and Phil discuss the ongoing challenge of damage mechanisms and corrosion-related issues in fertilizer plants and highlight the critical role of materials selection and process monitoring in managing equipment degradation rates. Read more and learn how to achieve long-term equipment reliability and maintain a robust mechanical integrity program through the routine collaboration between materials/corrosion, mechanical, and process engineering subject matter experts and inspection specialists.
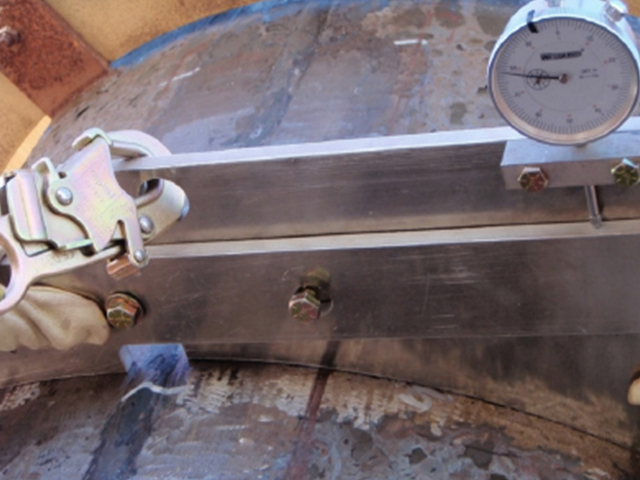
PSA on PSA Reliability
Learn how pressure swing adsorbers (PSAs) are crucial yet challenging in gas separation, and how a comprehensive lifecycle management plan based on engineering and fitness-for-service (FFS) can enhance reliability and extend equipment life. In this article, Neal and Kate discuss the importance of remaining life and inspection optimization studies in managing severe cyclic fatigue service, highlighting how pre-emptive fatigue studies guide inspection plans for PSA vessels. You will learn about inspection strategies and how to maximize capital investments through engineering strategies.
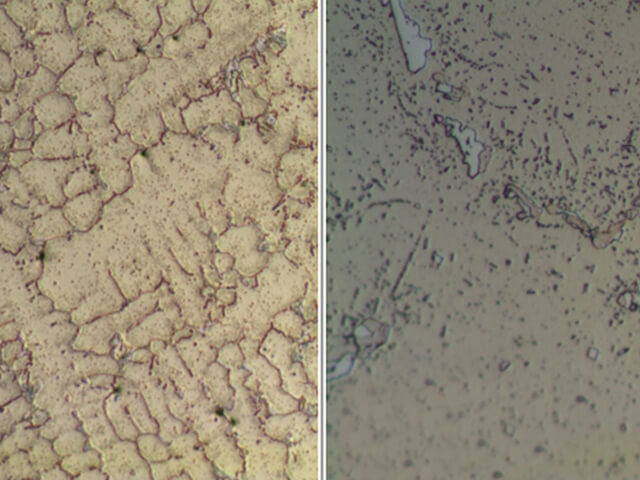
Understanding Damage Mechanisms in Industrial Gas Applications
Metallurgy and corrosion experts a key to identifying damage mechanisms and predicting corrosion rates for equipment used in processes like steam methane reformers (SMRs) and air separation units (ASUs). In this article, you’ll read how important it is to recognize which damage mechanism can be reasonably captured with risk-based inspection (RBI) methods and which ones require more detailed analysis using FFS principles. In addition, you will also gain insights into how to create robust mechanical integrity programs for industrial gas production units.
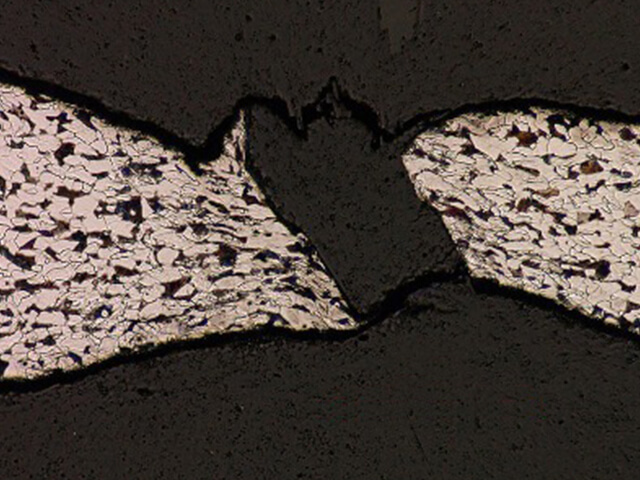
Case Studies of Failures in Crude / Vacuum Units
The contaminants found within crude oil can lead to numerous types of damage mechanisms that impact the crude unit. Unfortunately, multiple damage mechanisms can be the cause of an in-service failure. In this article, two case studies discuss the need to conduct in-service failure analyses for uncovering the root causes and developing practical risk mitigation strategies.
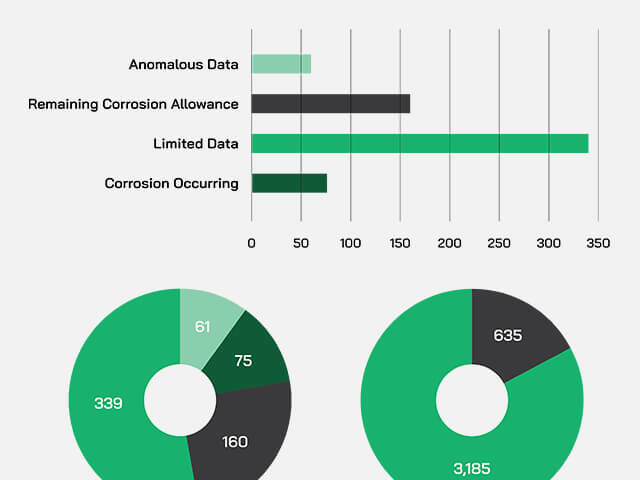
Optimizing Corrosion Monitoring Programs with Bayesian Analysis
In this Industry Insights article, Rob Clarke uses a case study to explain how advanced analytics and expert collaboration revolutionized asset integrity management, setting a new standard for industry excellence. You’ll read about how a facility transformed its corrosion monitoring program using CorrSolutions’ BOAR analysis to enhance efficiency and develop proactive maintenance strategies.
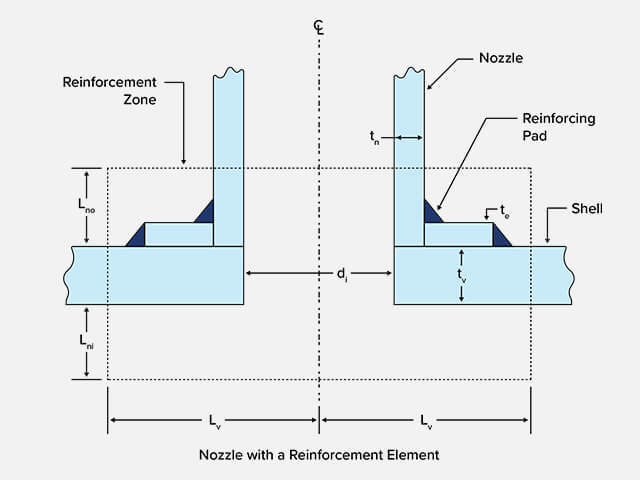
Inspectioneering: Damage Management Locations (DMLs) – Connecting Inspection Data with Asset Lifecycle Management
We’re highlighting an article written by David A. Osage from the Inspectioneering Journal’s July/August 2023 issue, in which he discussed E2G’s new inspection scheduling methodology that is reshaping asset integrity and equipment lifecycle planning and management. Using his vast knowledge and expertise in fitness for service (FFS), David outlines how E2G’s groundbreaking new maximum allowable working pressure (MAWP) approach aligns with API 579-1/ASME FFS-1 standards, ensures integrity with continued operation, and works with the damage classes listed in API 579.
This article appears in the July/August 2023 issue of Inspectioneering Journal.
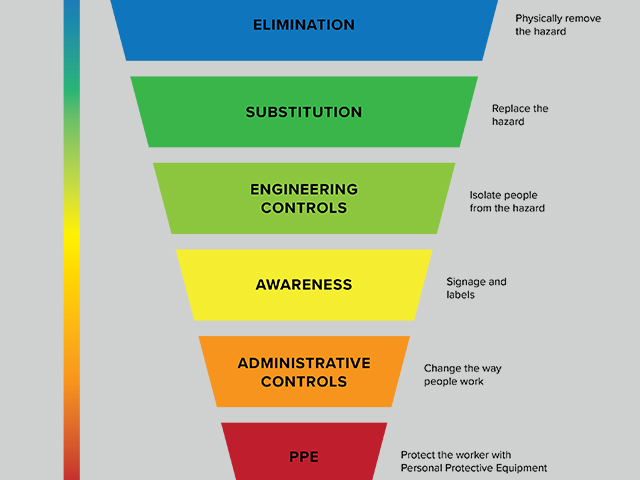
NFPA 70E: Creating an Electrically Safe Work Condition
Electrical failures can impact safety, production, and overall business operations; the simplest way to create an electrically safe workplace is to implement programs that eliminate the hazard. In this article, the author uses NFPA 70E as a foundation to provide practical recommendations you can implement to create an electrically safe work environment.
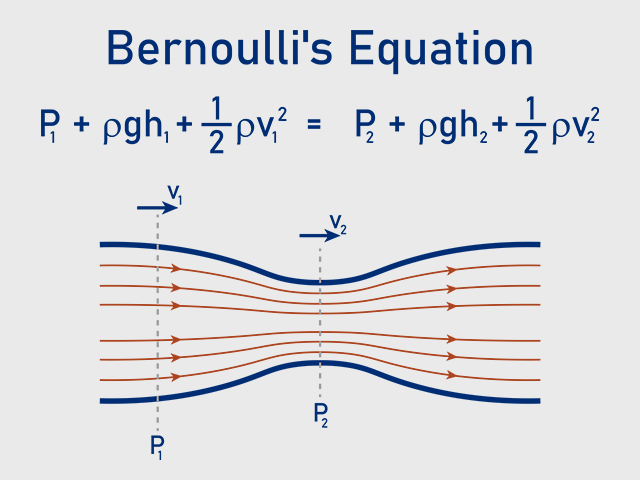
Understanding Differential Pressure (DP) Flow Meters: A Comprehensive Overview
In petrochemical plants, flow meters are designed to enhance efficiency, improve safety, and meet regulatory compliance. Real-time insights regarding fluid movement help to develop sustainable practices and enable precise monitoring for optimal resource management. In this article, you will read about differential pressure, volumetric, and mass flow meters; as well as their working principles, advantages, and installation methods.
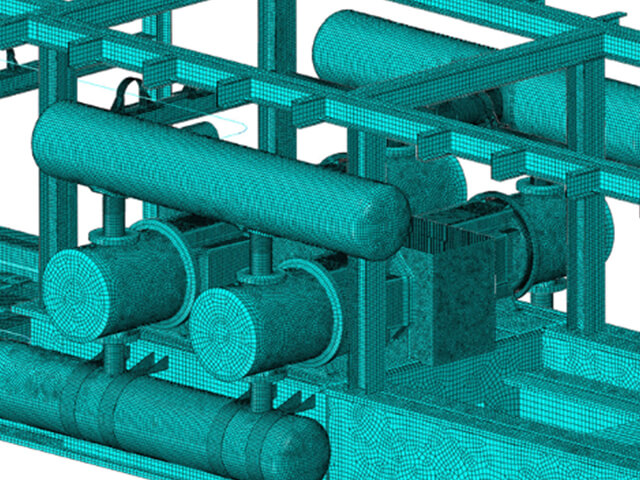
Guide to API 618 Acoustic-Mechanical Design Validations for Repurposed or Modified Reciprocating Gas Compressor Systems
Pulsation-induced forces can damage compressor foundations, reduce valve life, and lead to fatigue in piping and components. In this article, Dr. Bifano explains acoustic pulsation basics in reciprocating gas compressor systems and offers practical guidance on applying original acoustic-mechanical design principles during system modifications or repurposing. It’s essential to understand how these changes may affect system acoustics to prevent future vibration issues.
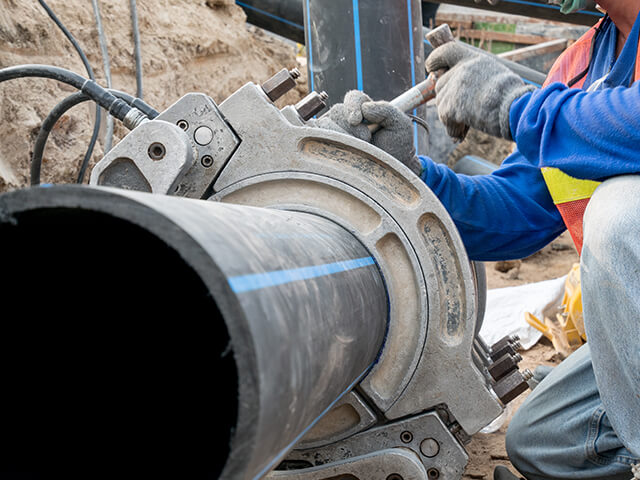
Hot Tap Evaluations and Practical Guidance for In-Service Repair Welding
In-service welding as part of a maintenance program is a practical and economical way to address leak repairs or new nozzle installations; however, it does come with a few risks, including burn-through and hydrogen-induced cracking. In this article, Raj will discuss the risks involved with in-service welding, thermal analysis to quantify the risks, and practical in-service welding considerations to ensure safe and successful hot tap connections.
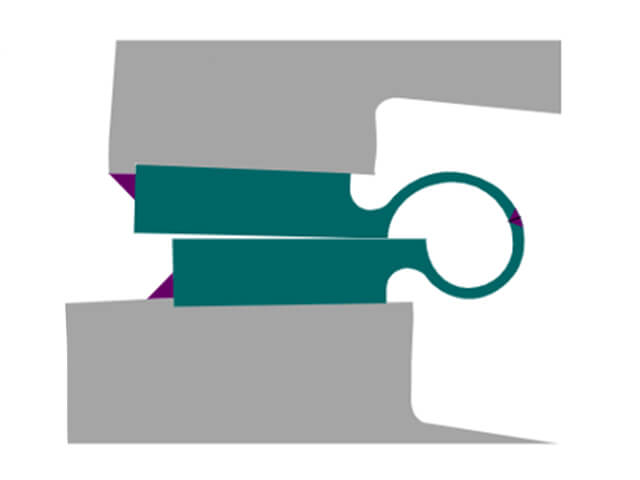
Leveraging EP-7-3-3 Series for Equipment Repairs
The need for post-construction equipment repairs and maintenance best practices has led to ASME PCC-1 and PCC-2 standards becoming valuable resources for many owner-operators, yet these standards inherently maintain a level of generality. In this article, Derek and Neal will explain how the Equity Engineering Practices (EEPs), specifically EP 7-3-3, address the gaps and provide the extra context, details, and guidance to provide more comprehensive solutions for post-construction equipment repairs.
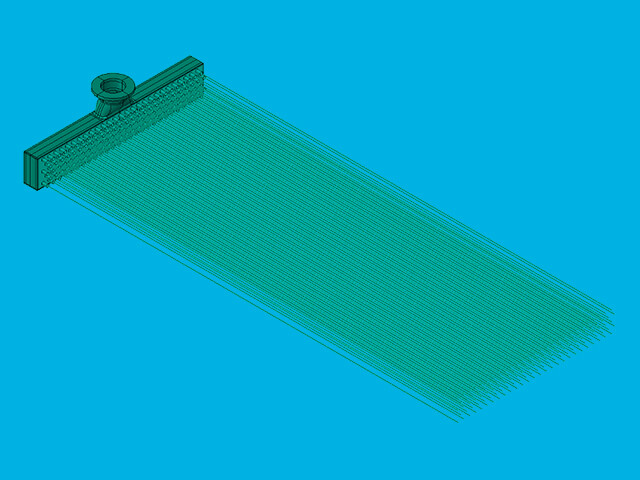
Fitness-for-Service for Asset Management of Air Coolers
Air-cooled heat exchangers (ACHEs) are designed to use ambient air to cool or condense a process fluid, which eliminates the need for large cooling water capacities. In this article, Kate and Ben discuss how a fitness-for-service (FFS) assessment can be a very powerful tool in air cooler lifecycle management to improve inspection planning and guide run, repair, or replace decisions.
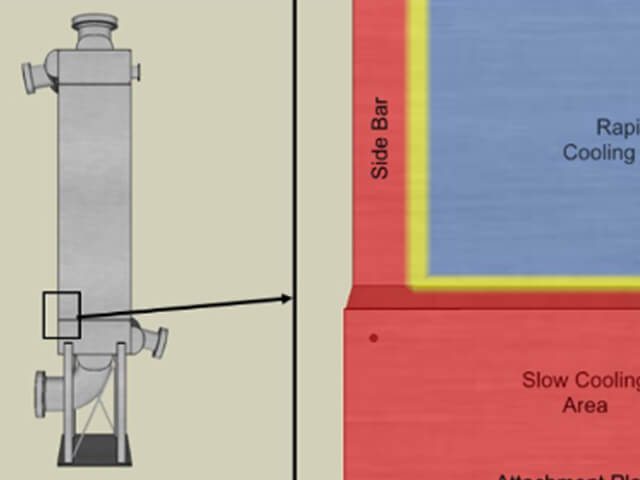
Reliability Issues Associated with Brazed Aluminum Heat Exchangers
Brazed aluminum heat exchangers (BAHXs) are distinctly prone to several damage mechanisms, including thermal fatigue, cracking, and corrosion. In this comprehensive article, the author uses a 2016 BAHX failure to explain typical BAHX reliability and maintenance issues and provide an overview of practical damage mitigation techniques.
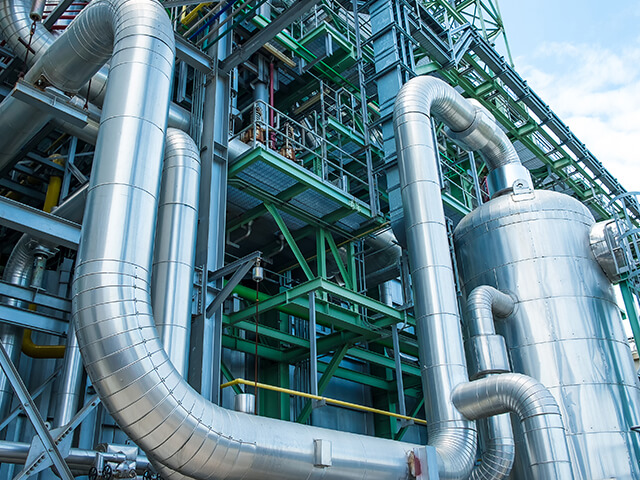
Leveraging Omega Creep Assessments to Extend Fired Heater Tube Remaining Life
Creep, a common damage mechanism across the refining industry, is commonly often found in fired heaters and boilers. In this article, Lucas offers a detailed description of an Omega creep test and shares the benefits of performing this analysis to accurately diagnose current damage and extend the remaining life of a facility’s fired heater tubes.
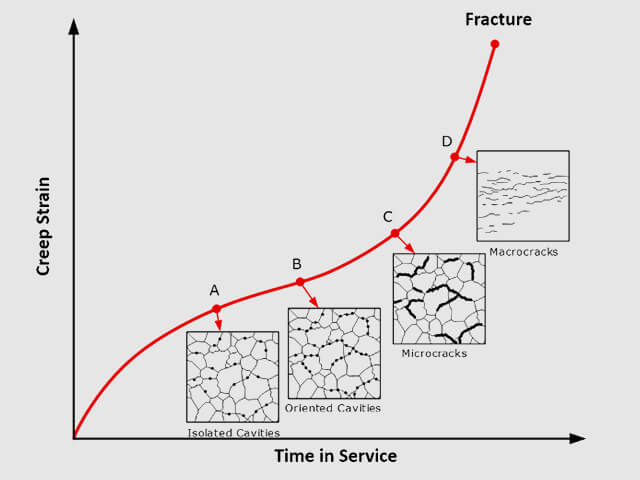
Commentary on the High-Temperature Behavior of Welds
Welds are often the weak links in pressure equipment and other structures, especially when operated at elevated operating temperatures. This article highlights the importance of understanding the high-temperature behavior of welds, specifically in relation to creep response, and discusses how creep testing helps to predict remaining life.
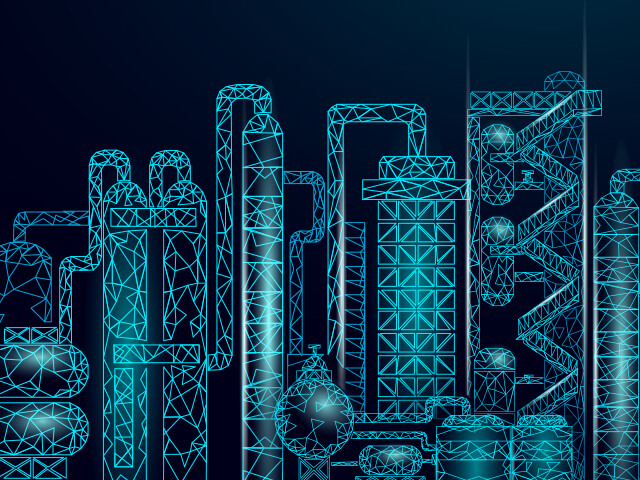
Leveraging Process Simulation for Informed Decision-Making
Process simulation models changes to a process, operations, or pressure relieving systems. Proactively simulating proposed changes at your facility will save money, improve safety process, and increase equipment reliability. In this article, you’ll read how investing in the long-term maintenance of your simulations will lead to better insights into the downstream effects of any changes and help you troubleshoot any process upsets.
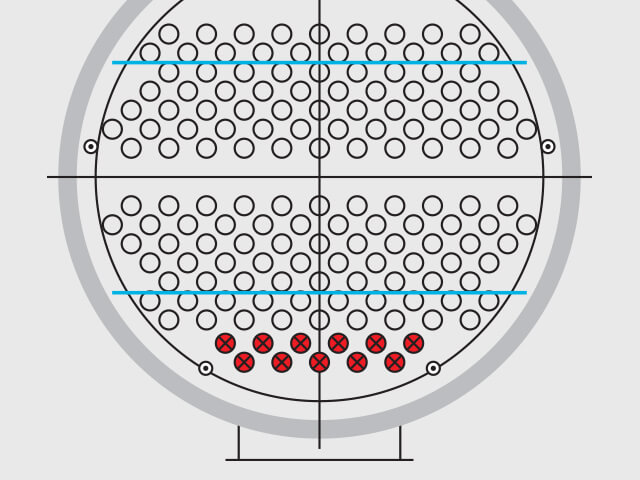
Managing Tube Rupture Failure Risks in Pressure Relief Systems
API 521 outlines the requirements for analyzing the credibility of a tube rupture and how to design overpressure protection in heat exchangers. Determining the credibility of a tube rupture can save a facility money on costly mitigation measures. In this article, you’ll learn about E2G’s proprietary tube rupture credibility assessment (TRCA) methodology and the four components needed to address API 521 requirements.
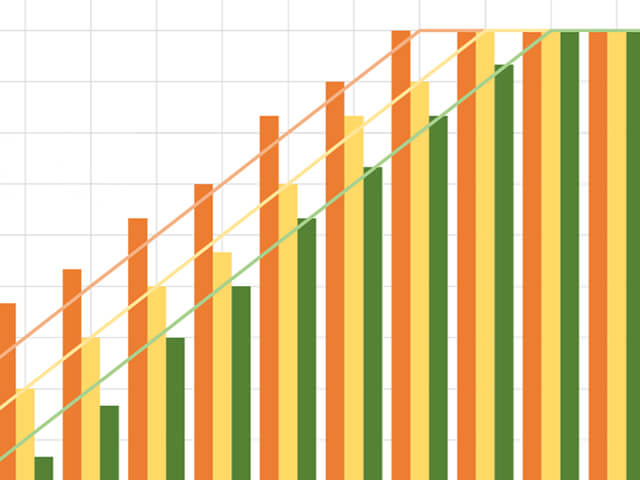
Large-Scale SFS Projects
Occupational Safety and Health Administration (OSHA) requires owner-users to maintain essential documentation authenticating adequate design and maintenance of pressure vessels and storage tanks. Unfortunately, it is not uncommon to find equipment operating in industry with minimal or no documentation. In this article, Bob Davis and Stephanie Dux discuss how large-scale SFS projects are an efficient and effective way to evaluate equipment on a defined schedule. SFS projects provide guidance on roles and responsibilities, methodologies, assumptions, and documentation of results.
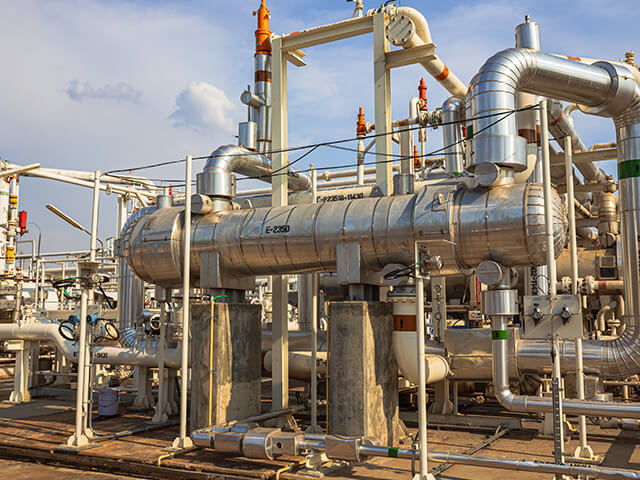
Basics of Rerating Equipment
Today, most in-service equipment remains in use for many years, or decades, beyond its intended design life. Throughout that extended service life, the process conditions can change, affecting equipment reliability. In this article, Matt Schaser discusses the importance of conducting rerates on equipment to meet jurisdictional requirements and use a variety of case studies to highlight some options available when performing a rerate assessment.
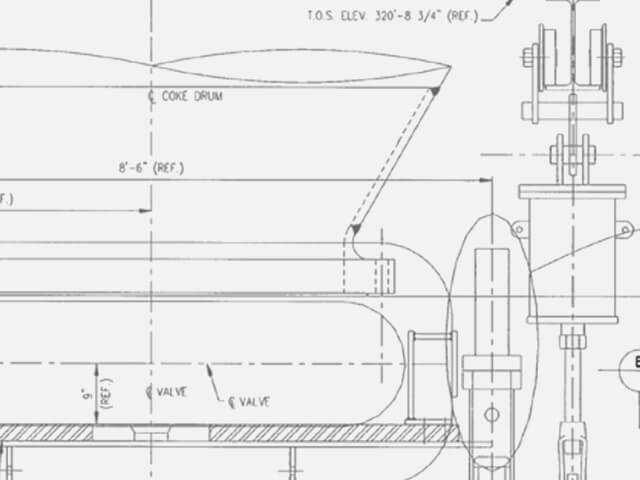
Leveraging Advanced Analysis for Coke Drum Reliability
Coke drums in delayed coker units present many reliability problems because they are subjected to unique types of damage mechanisms due to their operation. Thermal fatigue cracking is common in regions of high thermal stress due to frequent and severe thermal cycling. Bulging is also common because of this severe thermal cycling that creates hot and cold spots due to channeling effects in the coke formation that results in thermal ratcheting or progressive cyclic plastic strain accumulation.
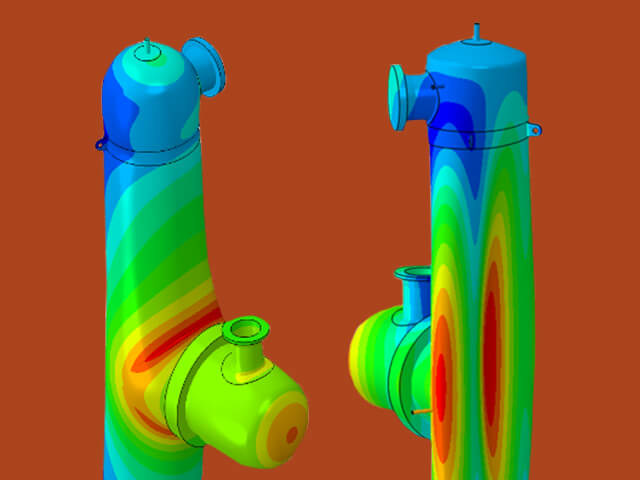
Fundamentals of Design by Analysis
Combining design by analysis (DBA) methods with modern computational approaches provides critical engineering tools for evaluating the structural integrity of in-service equipment and new equipment designs. To know which DBA technique to employ, it is essential to understand all possible failure modes based on equipment operation and loading scenarios. In this article, Phillip offers a high-level overview of modern DBA techniques and procedures for providing protection against plastic collapse, local failure, buckling, and cyclic failure.
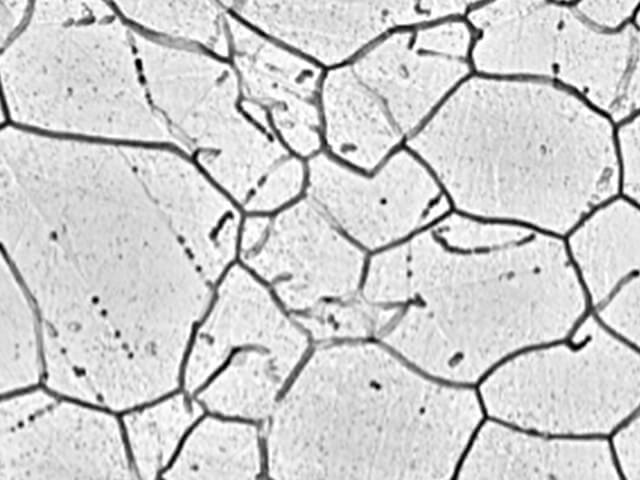
Understanding Fire Damage Assessments
When an industrial fire happens, it is important to understand what happened, why it happened, and how the equipment or plant may have been damaged from the heat. Engaging an experienced subject matter expert to assist with the damage assessment will help your plant determine the root cause of the fire and identify future prevention strategies. In this article, Paul provides an overview of the API 579 Part 11 fire damage assessment methodology and explains how proactively establishing a fire damage assessment methodology can save valuable time and resources.
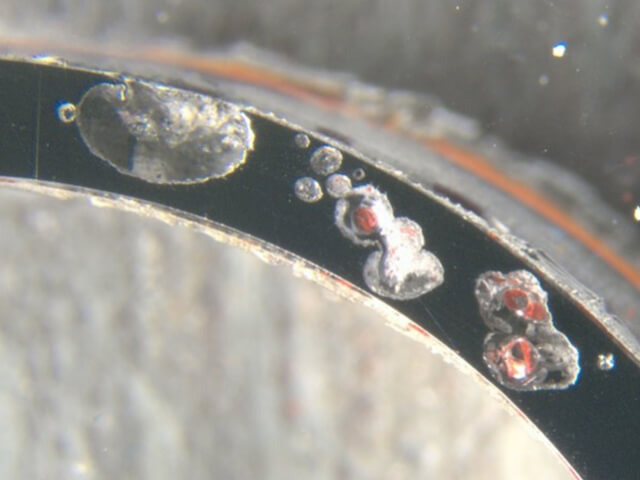
The Advantages of Performing Failure Analyses- The Light at the End of the Tube
A successful metallurgical failure analysis provides factual insight into the key mechanism(s) at play, as the metallurgy holds truths to be discovered. This article uses a variety of case studies to explain how the value of a failure analysis is uncovered from the analysis into the causes of the observed failure, future mitigation strategies, and interpretation of the physical findings into qualitative and/or quantitative results. Lucas explains how combining damage mechanism familiarity with engineering expertise will extract the full value from a failure analysis.
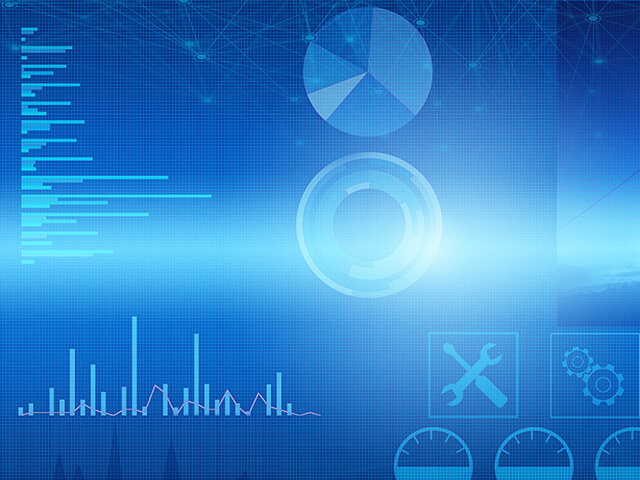
The Art of Database Maintenance: Optimizing IDMS QA/QC
We’ve all heard the term “garbage in, garbage out.” When managing an inspection data management system (IDMS), it’s important to implement a quality assurance (QA) and quality control (QC) process to keep the data clean and optimized. In this article, you’ll read how E²G has leveraged its expertise with developing QA/QC processes and automated QA tools to help our clients raise the bar on IDMS data quality.
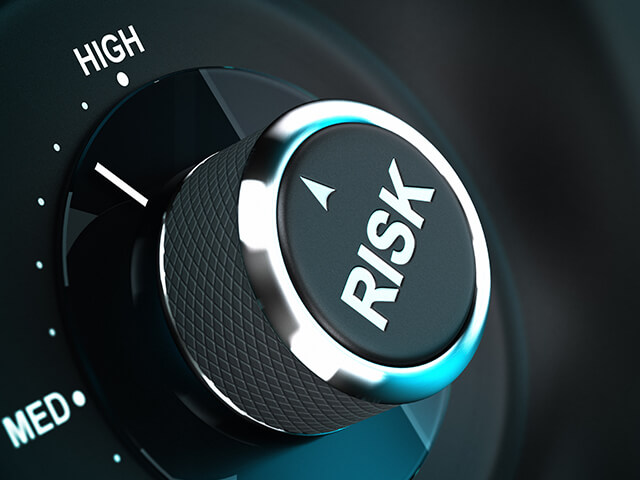
Uninspectable Risk
The purpose of RBI is to inspect all equipment and components as efficiently and targeted as possible; however, how do you perform RBI on an asset that will always call for inspection? In this article, you’ll read about an incredibly important and complex, although misunderstood, aspect of RBI — uninspectable risk. Lawrence Cleland provides a deep dive into uninspectable risk and discusses how to develop a well-considered asset management strategy to help you save money and reduce the number of unnecessary inspections.
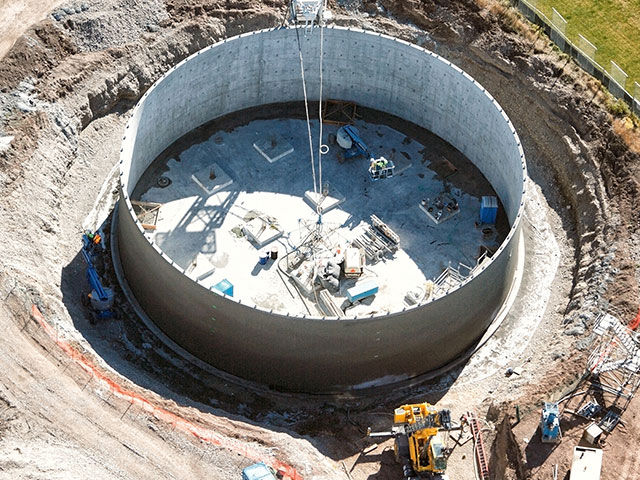
A Deep Dive into Aboveground Storage Tank Settlement Evaluation
Foundational settlement, particularly non-uniform settlement, poses a significant threat to the integrity and operational reliability of aboveground storage tanks. In this article, Katelyn and Derek take a detailed look into at the most common API 653 evaluation methods to provide insight into the limitations and use of the various techniques and show the potential benefit of conducting a detailed analysis for differential shell settlement and bottom edge settlement.

Buckling Evaluation of Pressure Equipment and Plant Structures
In any industrial facility or plant, buckling poses a significant risk to nearly all components under compressive stress. Several finite element analysis (FEA) tools are used to solve complex buckling issues; however, without fully understanding the underlying mechanics and other relevant factors, the results can be misleading. In this article, Derek and Matthew review the methodology and limitations of the ASME VIII-1, ASME VIII-2, and AISC 360 standards for assessing buckling in beams, columns, steel structures, and pressure vessels.
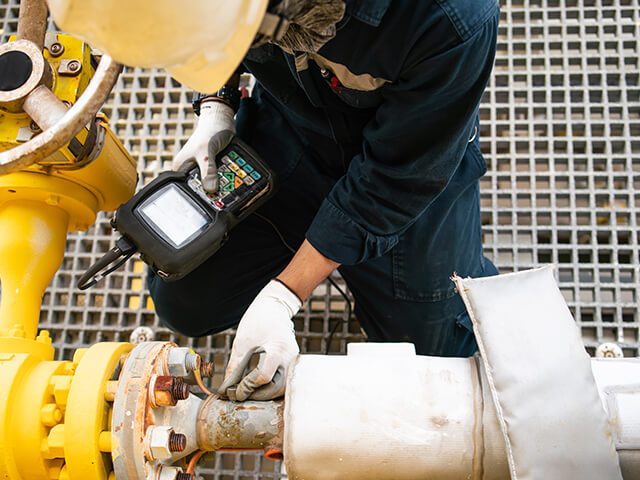
Proactive FFS for Volumetric Damage
Performing a proactive FFS assessment on equipment with volumetric wall loss can save both time and money during a turnaround. You can minimize inspection scope and outline a set of well-defined ‘goal posts’ for determining acceptability and identifying a targeted inspection list. In this article, the authors share multiple tips to proactively assess volumetric damage as it relates to the requirements of API 579-1/ASME FFS-1, Part 4 and Part 5.
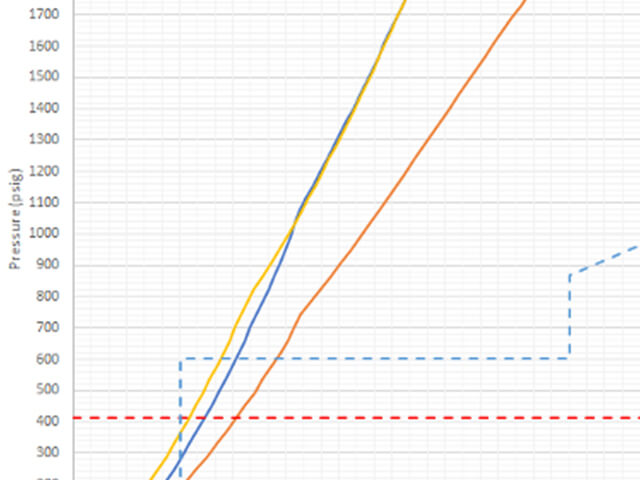
Proactive FFS: Advantages of Brittle Fracture Screening on Piping and Vessels
Proactively conducting brittle fracture assessments on higher-risk pressure equipment and piping, even if it was built relatively recently, will help prevent unexpected failures. This article identifies the three components that drive susceptibility to brittle fracture and includes two case studies to help demonstrate the benefits of using a fracture mechanics-based approach.
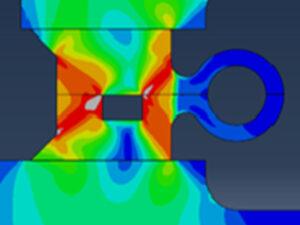
Improving Reliability of Bolted Flanged Joints
ASME VIII-1 Appendix 2 flange design rules states flanges should be sufficiently robust to withstand the stresses produced by operating loads; however, what happens if those flanges leak during operation?. Do you know what options are available to reduce or eliminate the potential risk of leakage in bolted flange joints? In this article, Bob Davis introduces several options to evaluate bolted flange designs with the goal of minimizing the risk of leakage without risking damage to any of the joint components.
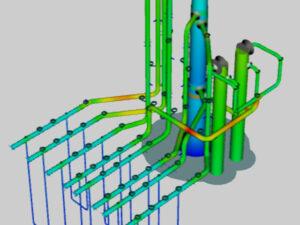
SIMFLEX-IV: A Modern Pipe Stress Engineering Solution
SIMFLEX-IV, the latest update to E2G’s cloud-based piping stress analysis software, will help you prevent potential failures by improving the structural integrity of piping systems and supporting structures. In a single run, you will be able to assess sustained, occasional, and displacement stresses at every data point throughout the piping system. This article introduces you to fast and easy ways to integrate advanced static and dynamic piping stress analysis into your daily workflow.
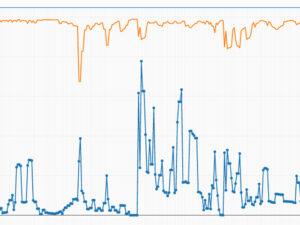
Hammered Pipe Still Standing: Is It Fit for Service?
Steam piping systems that are not adequately controlling condensate levels may experience a steam hammer event, which is when a slug of condensate is propelled at high velocity down the piping system. When the large dynamic slug force hits an elbow or pipe cap, it can displace the piping system or slide the pipe shoes off the structural members. In this case study, Kraig Shipley discusses a recent consulting project that used SIMFLEX-IV to determine if a steam header was still fit -for -service after a steam hammer event.
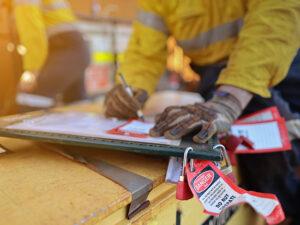
PSM and Mechanical Integrity in the Hazardous Materials Processing and Handling World
When well implemented, a mechanical integrity program will reduce failures, extend equipment life, increase operating limits, and optimize maintenance and inspection budgets. In this article, Jim McVay introduces several of the elements you need to consider when developing a successful mechanical integrity program and explains how everyone plays a role in the effective implementation.

Reduction of Nuisance Alarms by Implementing the Alarm Management Lifecycle, A Focus on Rationalization
We are all familiar with Aesop’s fable, “The Boy Who Cried Wolf.” Similarly, with alarm management, if you hear a false alarm too often, you may miss the opportunity to prevent a dangerous situation or equipment failure. In this article, Melissa Westbrook discusses the dangers of ignoring nuisance alarms and provides actionable insights into developing an alarm rationalization philosophy.
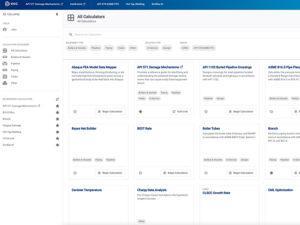
Launching the New Equity Engineering Cloud (eec) Platform
The newly launched eec platform delivers accurate engineering calculations using the speed and flexibility of the cloud. The refreshed interface and dashboard layout are streamlined to make it faster and easier to make informed decisions on safety and reliability. The eec remains your one-stop platform to help you manage risk and control inspection costs throughout a facility’s lifecycle.
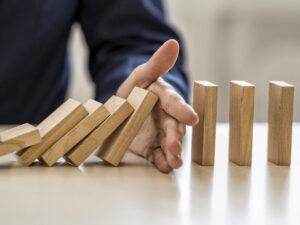
Manage the Damage
In this World Fertilizer article, Paul Kowalski explains that damage mechanism reviews (DMRs) are one of the first steps in developing many key process safety management (PSM), mechanical integrity (MI), and equipment reliability programmes in fertilizer processing units. Completing a DMR can help ensure long-term reliability of fixed equipment and piping, allow for quicker run, repair, and replace decisions to be made, and is a critical component for proper material selection.
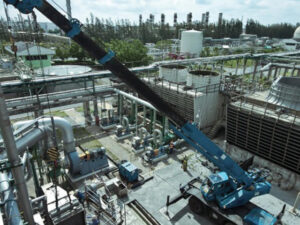
Equity Engineering Practices: Best Practices for Capital Projects, Repurposing Projects, and Lifecycle Management
The EEPs help owner/users manage equipment and facilities from “cradle to grave,” over the entire lifecycle of their equipment and infrastructure. In this article, Joel Andreani and Susie Szymanski explore how the history of the EEPs and E2G’s dedication to expanding the collections has helped owner/users improve operational reliability and reduce costs.
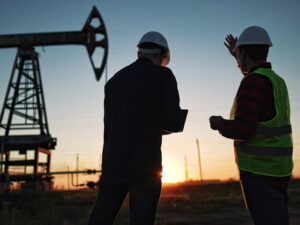
Capturing Corporate Memory with Internal Best Practices – Retaining Knowledge After the Great Retirement/Resignation
We knew the great retirement/resignation was coming; however, the last two years has expedited a rapid loss of technical knowledge. Think about your organization, if your experienced employees’ knowledge and expertise are not recorded, their 40-plus years of practical experience and knowledge will be lost. Read how the Equity Engineering Practices (EEPs) integrate legacy documents and employee knowledge to support effective asset lifecycle management.
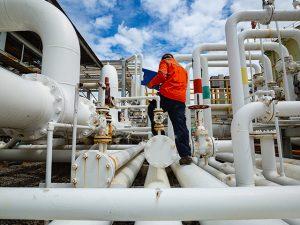
Is Advanced Statistical Analysis the Next Step in Your Piping Inspection Journey?
Advanced statistical analysis can provide measurable benefits and new insights into corrosion management, especially when the knowledge is shared across an organization. In this Inspectioneering Journal article, Chris Massengale and Robert Clarke discuss how the implementation of this advanced analysis with other best practices will provide a better understanding of corrosion risks, optimize maintenance costs, and create safer facilities.
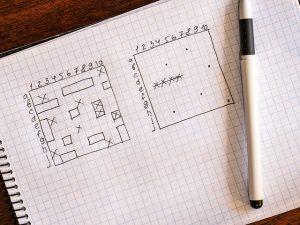
How Playing Battleship Helps with CML Optimization
As a child, many of us played the game Battleship. But did you know this game provides a great introduction to Bayesian updating and corrosion monitoring location (CML) optimization? Using the Battleship analogy, Branden Stucky introduces the Bayesian Optimized Asset Reliability (BOAR) assessment and provides insight into how to combine expert knowledge with collected data to identify corrosion rates.
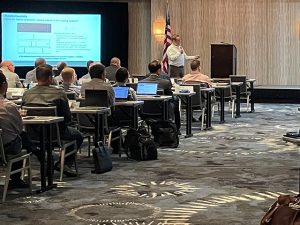
Let E2G’s SMEs Train Your Future SMEs!
Knowing the fundamentals of industry programs, codes and standards, and technology will prepare new engineers for long-term success. At E2G, we have developed a new training course that supports knowledge transfer between industry experts and junior engineers, plus fills the gap for those companies without a formal training program. This article expands upon the June 16th webinar in which Mark Harmody introduced the curriculum for the Fundamentals of Asset Lifecycle Management course (FALCM).
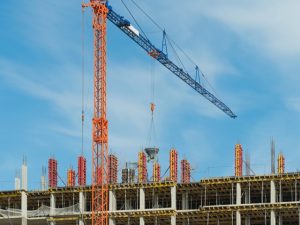
Updates to ASCE 7 and the Impact on Equipment Standards
The recent changes made to ASCE 7 will have a trickle-down impact on API and ASME codes, plus the International Building Code (IBC). In this article, Derek Slovenec and Joel Andreani discuss the most significant load changes (seismic, wind, tornado, snow, and rain) and the potential impact on ASME and API standards that reference ASCE 7.
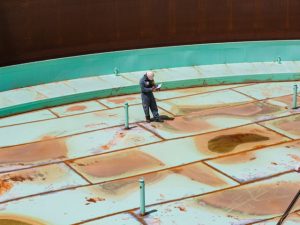
Fitness-for-Service of Aboveground Storage Tanks – Applicability of API 579
Fitness-for-Service (FFS) is a recognized industry practice for assessing equipment mechanical integrity when unanticipated damage is found and can often be used to extend service life while minimizing downtime and avoiding costly repairs. In this article, Katelyn Gustoff and Joel Andreani examine the applicability of using API 579-1/ASME FFS-1 (API 579) FFS and API 653 assessment standards with in-service ASTs.
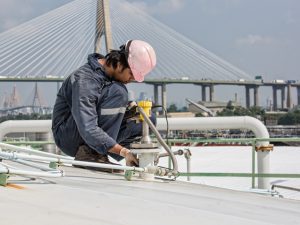
Level Measurement in Mature Atmospheric Storage Tanks
Mature storage tanks were typically constructed between 1950 to 1970. As the installation of remote monitoring solutions increases in mature tanks, maintenance personnel must start addressing the best way to make the required change or addition. In this article, Bart Smith explores the history of tank level management and measurement techniques and provides recommendations for updating instrumentation to improve safety and reliability.
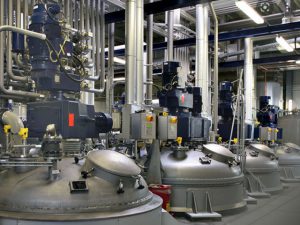
A Methodology for Difficult Level Application Evaluations
Harsh process conditions, extreme material properties, or limited infrastructure are contributing factors to difficult level applications. By implementing a consistent methodology for difficult level applications, you will achieve high uptime and system reliability. In this article, Melissa Westbrook outlines a simple documentation and methodical analysis to support new or existing instrumentation at your facility.
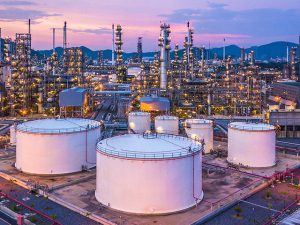
Aboveground Storage Tank Overfill Prevention – Updated Standards, Regulatory Focus, and E2G Services
This article discusses how the combination of the changes in the fifth edition of API 2350, Overfill Prevention for Atmospheric Storage Tanks in Petroleum Facilities (2020), and the adoption of this standard by various regulatory bodies has put additional requirements for overfill prevention on owners/operators of AST facilities.
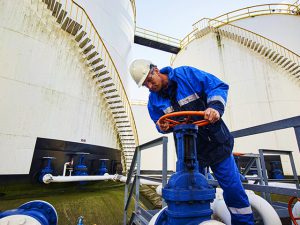
Prevention of Overfill for Atmospheric Storage Tanks
The 5th edition of the ANSI/API Overfill Prevention for Storage Tanks in Petroleum Facilities was recently released. In this article, read about the recent changes to API 2350 and an 11-step procedure that you can apply at your processing facility.
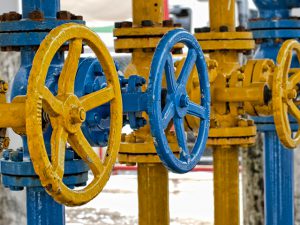
An Unfinished Chapter
This article, published in the September 2021 issue of World Fertilizer, discusses the improvements to the API codes and standards and how those changes impact the 3% rule.
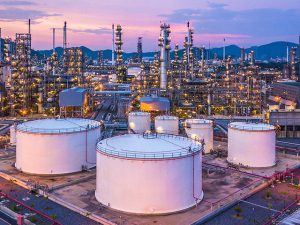
Asset Criticality Assessment: How to Implement and Improve Your Reliability Program
What is asset criticality and why is it important to your reliability program? This article outlines how to prepare for a criticality assessment, assemble the team, and perform the assessment.
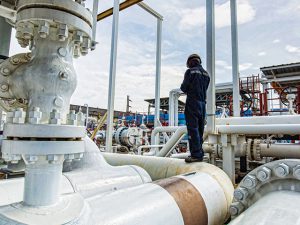
Application of API RP 691 Risk-Based Machinery Management to Existing Process Plants
Incorporate machinery risk management into a mechanical integrity program to prevent loss of containment, equipment failures, and a potential process safety event. This article reviews the risk management methods of API 691 and provides easy-to-follow recommendations.
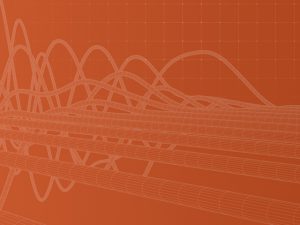
Mitigating Piping Vibration Risk: Case Studies on Using the Level 1, Level 2, & Level 3 FFS Approach
Piping vibration failures are not uncommon in the oil and gas, petrochemical, and chemical processing industries. In this webinar, Dr. Bifano discusses and compares the future API 579 Part 15 method to current industry approaches (ASME OM-3) and uses several case studies to help you identify, evaluate, and mitigate piping vibration.
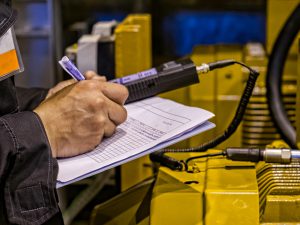
Identifying and Understanding the Risk of Acoustic-Induced Vibration Failures
Acoustic-induced vibration (AIV) is often more difficult to identify than other vibration mechanisms, such as flow-induced turbulence, slug flow, mechanical excitation from machinery, and acoustic pulsation. This article discusses ways to identify and mitigate AIV at a plant, plus how to proactively prevent AIV using design controls.
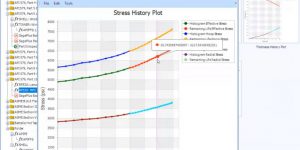
Case Study: Creep Assessment of a Heater Tube Using SagePlus™
High operating temperatures can lead to a variety of damage, including creep. During the SagePlus™ User Group Meeting, Matt S. Schaser shared a case study that estimated the remaining life of heater tubes operating at temperatures in the creep range.
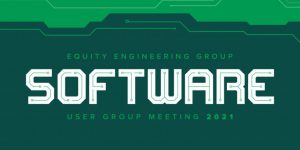
2021 SagePlus™ and API RBI User Group Round-Up
“Great effort to provide useful content. I got the feeling I was part of an embracing community working together for the
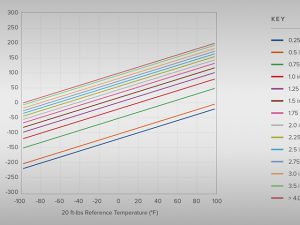
Establishing Fracture Mechanics Based on Minimum Allowable Temperatures for Low-Temperature Applications of ASME B31.3
Although rare, the consequences of brittle fracture are typically catastrophic, and preventing brittle fracture is essential when establishing fixed equipment life-cycle management strategies. This article discusses E2G’s proprietary Level 1 and Level 2 procedures for establishing minimum allowable temperatures (MATs) for low-temperature applications of ASME B31.3 piping.
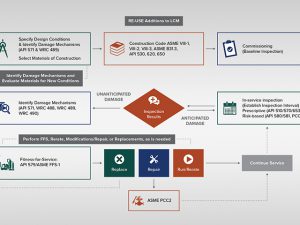
Renewable Energy & Other Changes in Service Scenarios: Evaluating Plant Assets for Re-Use
Read a comparison of a reuse project to FFS/SFS, addresses several repurposing questions, and explains the keys to conducting a successful conversion. In addition, be introduced to the upcoming changes to the Equity Engineering Practices (EEPs) that will deliver additional protocol documents to support safe and reliable operations.
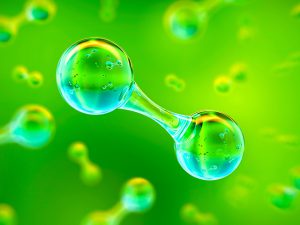
Converting Units to Process Renewable Feeds: Materials & Corrosion Concerns
In this article, Nathaniel Sutton examines the different metallurgical issues and corrosion challenges prevalent in the bio-oil and biomass oils markets and introduces several areas of consideration when converting a conventional petroleum processing unit over to renewable feeds.
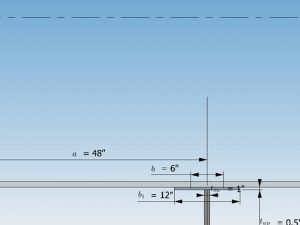
No Documentation, No Problem. OSHA Compliance is Still Feasible.
Conducting suitability-for-service (SFS) assessments helps owner-operators obtain OSHA compliance for any fixed equipment that lacks documentation. In this article, Brian Macejko highlights E2G’s six-step process, based on API 510 Pressure Vessels, that helps owner-operators comply with OSHA requirements.
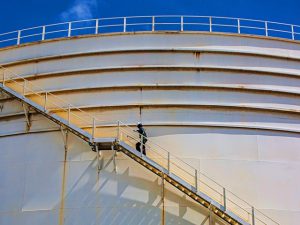
Tank RBI, Not Just an Inspection Deferral Tool
Learn how applying quantitative RBI principles to storage tanks will result in optimized inspection intervals and reduced risk of loss of containment. This article discusses the difference between qualitative and quantitative tank RBI and how tank RBI is a central part of a facility’s overall tank integrity management program (IMP).
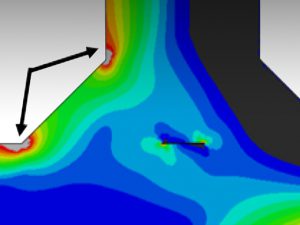
Fitness-for-Service for Aboveground Storage Tanks
This article explores applying the API 579-1/ASME FFS-1 (API 579) FFS standard to aboveground storage tanks and shares several case studies to illustrate how FFS techniques can help you make informed run-repair-replace decisions for a facility’s storage tanks.
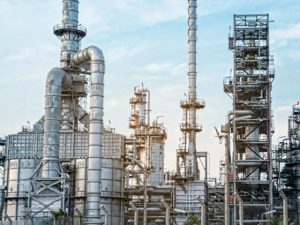
Special Emphasis Areas in a Mechanical Integrity Program
Implementing a mechanical integrity (MI) program at a processing facility is essential for maintaining safe and reliable operations. In this article, Joel Andreani investigates an important subset of an MI program: special emphasis mechanical integrity (SEMI) programs.
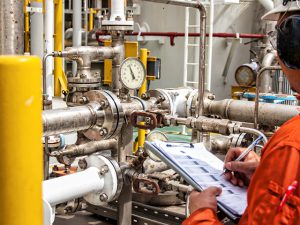
Improving Your Mechanical Integrity Program
Learn how to support the full life-cycle management of your assets by evolving your MI program to meet changing business and technological requirements. In this article, James Olson will highlight a variety of techniques that will proactively help you and your organization free up both time and resources.
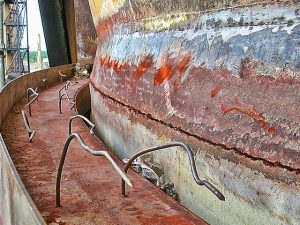
Turnarounds: Executing a Problem-Solving Team
A successful turnaround has five main stages: setting goals, project scoping, detailed planning, execution, and post-turnaround planning. This article focuses on the advantages of a problem-solving team to resolve equipment inspection discovery and efficiently minimize lost opportunity costs.
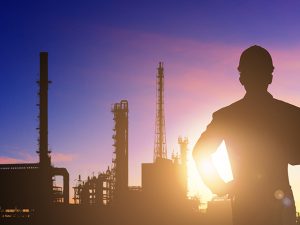
The Importance of Pre-Turnaround Reviews
A turnaround can cost hundreds of thousands or even millions of a dollars per day. In this article, you’ll learn how Risk-Based Inspection (RBI) helps to manage the costly impact of turnarounds through proper pre-planning to minimize the overall downtime.
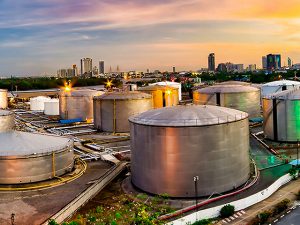
Evaluating a Tank Fixed Roof Structural Failure
Aboveground storage tanks are susceptible to damage from many factors, including environmental loads, process upset conditions, strength reduction due to metal loss, tank settlement, or some combination thereof. This damage often manifests as buckling of the tank shell, which is thin relative to its large surface area.
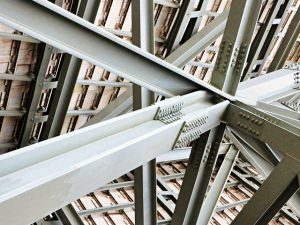
Q&A: Structural Integrity Programs
Aging or deteriorating structures, foundations, and other infrastructure cost U.S. businesses billions of dollars each year. Problems with structures and foundations are often a result of design flaws, construction defects, deteriorating conditions, extreme environmental events, and/or changes in applied loads.